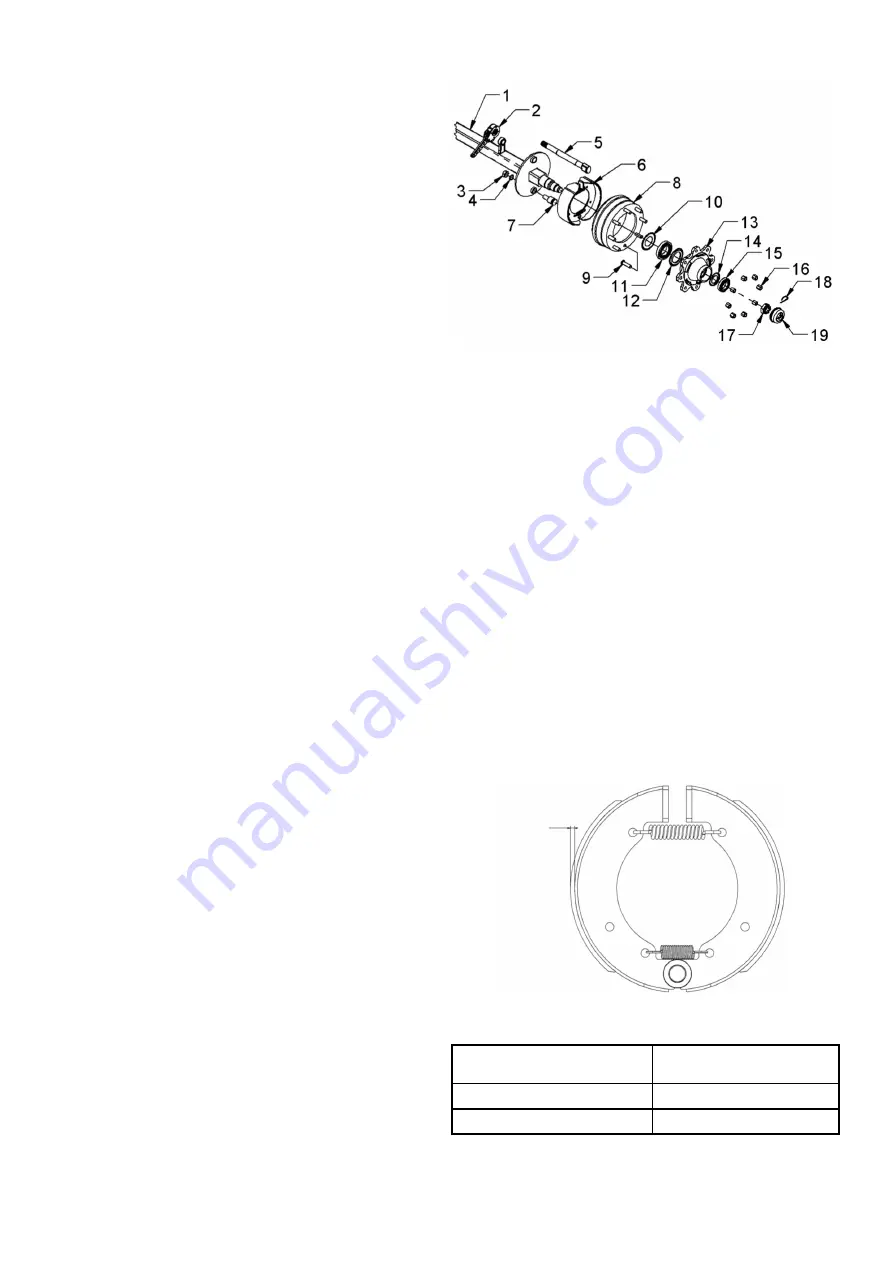
Reassembly :
1
Grease the spindle lightly.
2
Refit the oil seal or wheel bearing seal (ensure that the
seal is the right way round), a punch makes it easier to
fit the wheel bearing seal and avoids damaging the
seal.
3
Apply a generous coating of grease to the large bearing
cage and rollers, making sure that the grease
penetrates all round the rollers and under the cage.
4
Fit the interior cone of the large bearing on the spindle,
it is important to take care not to damage the cage of
the bearing, use a tube apply pressure only to the cone
to prevent damage to the cage or the rollers.
5
Apply a 15 mm (small axles) or 20 mm (large axles)
layer of grease all around and right across the large
and small bearing cups that are still in the hub.
6
If the hub does not have grease retaining plates, put a
large amount of grease in the centre of the hub to act
as a reservoir.
7
Slide the hub/drum assembly over the spindle and the
brake shoes keeping the hub perfectly straight and
aligned until it is in contact with the oil seal at the back
of the spindle.
8
Apply a generous layer of grease to the small bearing
cage and rollers and fit the assembly to the spindle.
9
Fit the castle nut and adjust it as described above (See
paragraph 13.18 wheel bearings).
10
Lock the castle nut with a hair
-
pin clip or new split
cotter pin as appropriate.
11
For hubs without grease retaining plates, fill the hubcap
with grease.
12
Refit the hubcap.
13.20 Handbrake (where fitted)
The central spindle of the handbrake lever will need
greasing every 3
months.
Cables should be inspected for damage or fraying and
replaced as necessary.
13.21 Service Brake Maintenance
13.21.1 Initial Checks
The brakes should be tested before using for the first time
and after the first laden journey :
Check the actuator and return spring mountings, check the
actuator stroke and return travel and check that the road
and parking brakes operate and release correctly.
Check the fulcrum nuts are tight and the elastic pins
retaining the nuts are fitted.
Check for air or oil leaks in the braking system.
Key
Figure 14. Braking components
13.21.2 Checking brake shoes for wear
The brakes should be checked for wear every 2 months or
after 1000 hours use.
It is likely that the linings are worn when the actuator travel
has increased significantly.
Check the thickness of the brake linings, they should be
replaced if they are below the minimum thickness
Figure 15. Minimum brake lining thickness.
Table 9. Minimum brake lining thickness.
Lining
thick-
Brake Size mm
Minimum lining thickness
300 x 60
2 mm
406 x 120
5 mm
27
1
Axle
11
Inner Bearing
2
Adjustable Brake Lever
12
Inner Seal
3
Locking Nut
13
Hub
4
Locking Washer
14
Outer Seal
5
Cam Shaft
15
Outer Bearing
6
Brake Shoe
16
Wheel Nut
7
Fulcrum
17
Crown Nut
8
Brake Drum
18
Sprung Pin
9
Wheel Stud
19
Hub Cap
10
Seal
Summary of Contents for Tomahawk 7100
Page 1: ...30417 10100 11 19 30970 10345 31725 11338 10056 3694 TMKBXOP1119A...
Page 38: ...NOTES 35...
Page 39: ...36 NOTES...
Page 40: ......