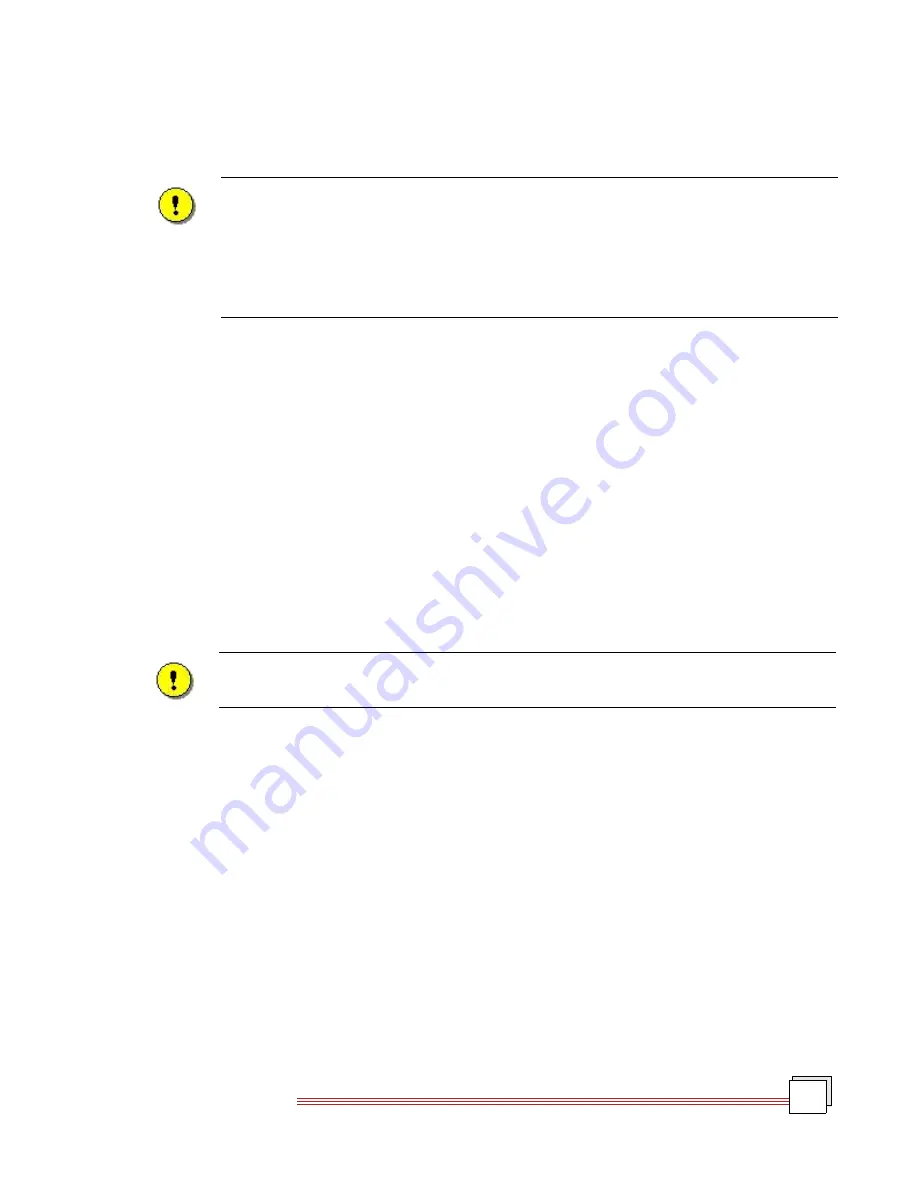
AR 2000 Operator’s Manual
97
Step 3: Positioning Gap and Pressure Cell Calibrations
Once the Pressure Cell cup and rotor have been installed, you will need to position the gap and perform the
calibrations as directed in this section.
CAUTION: The standard calibration routines used by Rheology Advantage for zero gap,
geometry inertia and bearing friction are not suitable for use with the pressure cell. When
the pressure cell is selected as the measuring geometry, these routines are either
disabled or are replaced by more appropriate routines. Do not attempt to use or calibrate
the pressure cell unless this geometry is selected.
1.
Ensuring that the pressure cell geometry is selected in the software, find the gap zero position. Do not request
the instrument to raise the head to the backoff distance. Set a gap of 3500 µm.
2.
When the Pressure Cell is the selected geometry on an AR2000 or AR2000ex, the
Gap Zero Mode of normal
force with a value of 5N will be used. This will override any other settings in Rheology Advantage software.
3.
Conduct the Bearing Friction Calibration. The bearing friction routine used when the Pressure Cell is selected
as the geometry is slightly different from the standard routine. The calibration should be conducted at a
geometry gap of 3500 µm. The bearing friction calibration must be done again when another measuring
system is used. A typical value for the Pressure Cell should be between 8 and 15 µN.m / (rad/s). This is about
ten times higher than for other geometries.
4.
Map the Air Bearing. Perform a rotational mapping at a gap of 3500 µm using the Standard mapping routine.
NOTE: DO NOT USE PRECISION OR EXTENDED MAPPING ROUTINES WITH THE PRES-
SURE CELL.
CAUTION: It is important that the bearing is re-mapped before any other measuring
system is used.
NOTE: When changing to other geometries, Rheology Advantage does not restore the previous
settings. However, the mapping table is cleared and the bearing friction is reset to zero. Any
functions that were previously unavailable are reactivated and the gap zero mode settings are
restored, because the settings were not overwritten.
5.
Check the Cell by running peak-hold test at 0.05 rad/s and a duration time of 126 sec. The peak-to-peak
residual torque should not be larger than 100 µN.m.
Summary of Contents for AR 2000
Page 24: ...AR 2000 Operator s Manual 24...
Page 30: ...AR 2000 Operator s Manual 30...
Page 34: ...AR 2000 Operator s Manual 34...
Page 66: ...AR 2000 Operator s Manual 66...
Page 84: ...AR 2000 Operator s Manual 84...
Page 120: ...AR 2000 Operator s Manual 120...
Page 126: ...AR 2000 Operator s Manual 126...
Page 128: ...AR 2000 Operator s Manual 128...
Page 132: ...AR 2000 Operator s Manual 132...
Page 134: ...AR 2000 Operator s Manual 134...