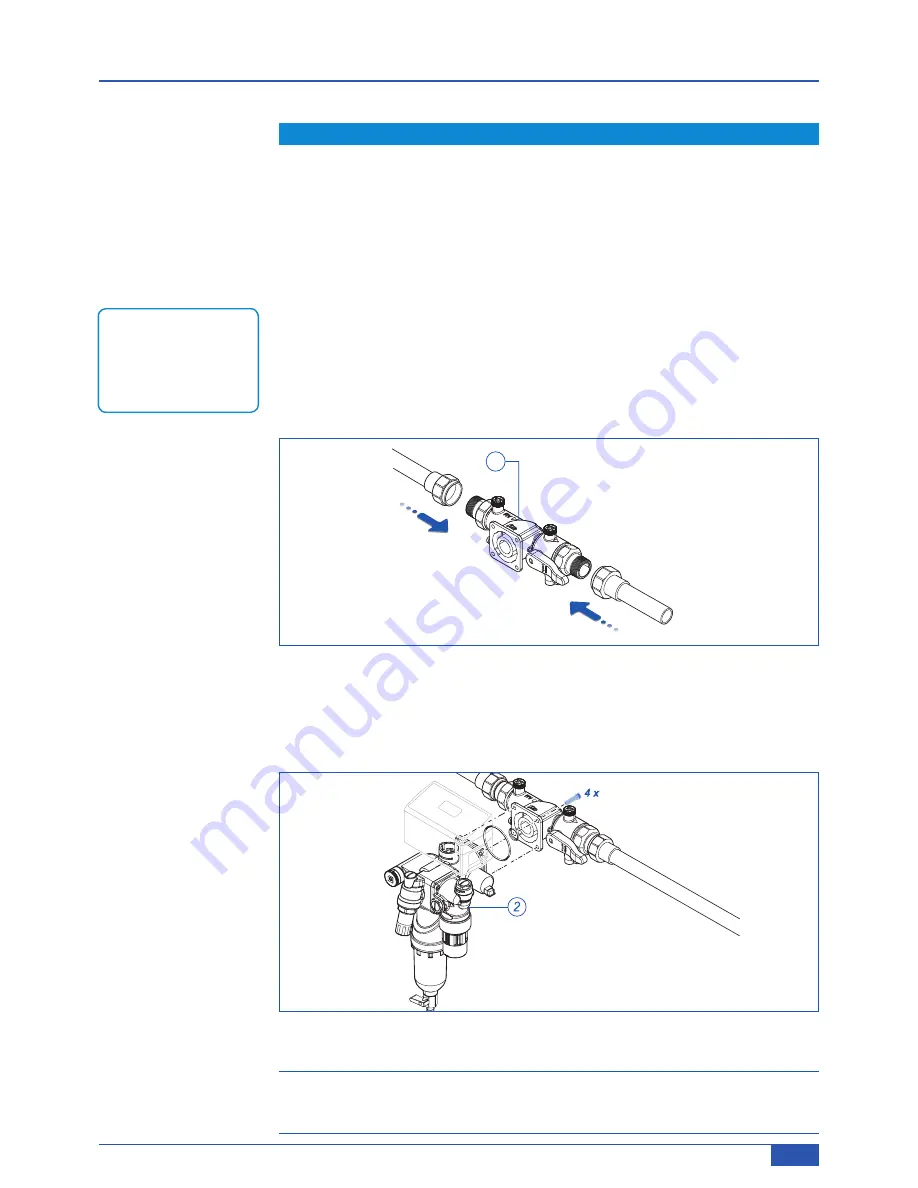
Installation and commissioning
5.2 Installation
Install the fully automatic filling system upstream of the heating system and make
sure it is readily accessible .
►
Thoroughly flush the pipe prior to installation.
►
Turn off the water supply prior to starting the installation work.
5.2.1
Installation of the connection flange
Mount the device only in potable water installations in accordance with DIN
1988, upstream of and close to the heating system.
►
Remove the connection flange from the fully automatic filling system.
►
Mount the connection flange (1) in the potable water installation with standard
transition pieces .
1
Fig. 8:
Mounting of the connection flange
5.2.2
Installation of the fully automatic filling system
►
Fit the fully automatic filling system (2) with the four hexagonal socket screws
and the two O-rings to the connection flange.
Fig. 9: Mounting of the fully automatic filling system
When connecting the tundish of the BA backflow preventer to
►
the sewer, observe the current version of the standard DIN EN
12056.
Note:
Install the connection
flange without applying
stresses! Observe the
correct direction of flow!
17