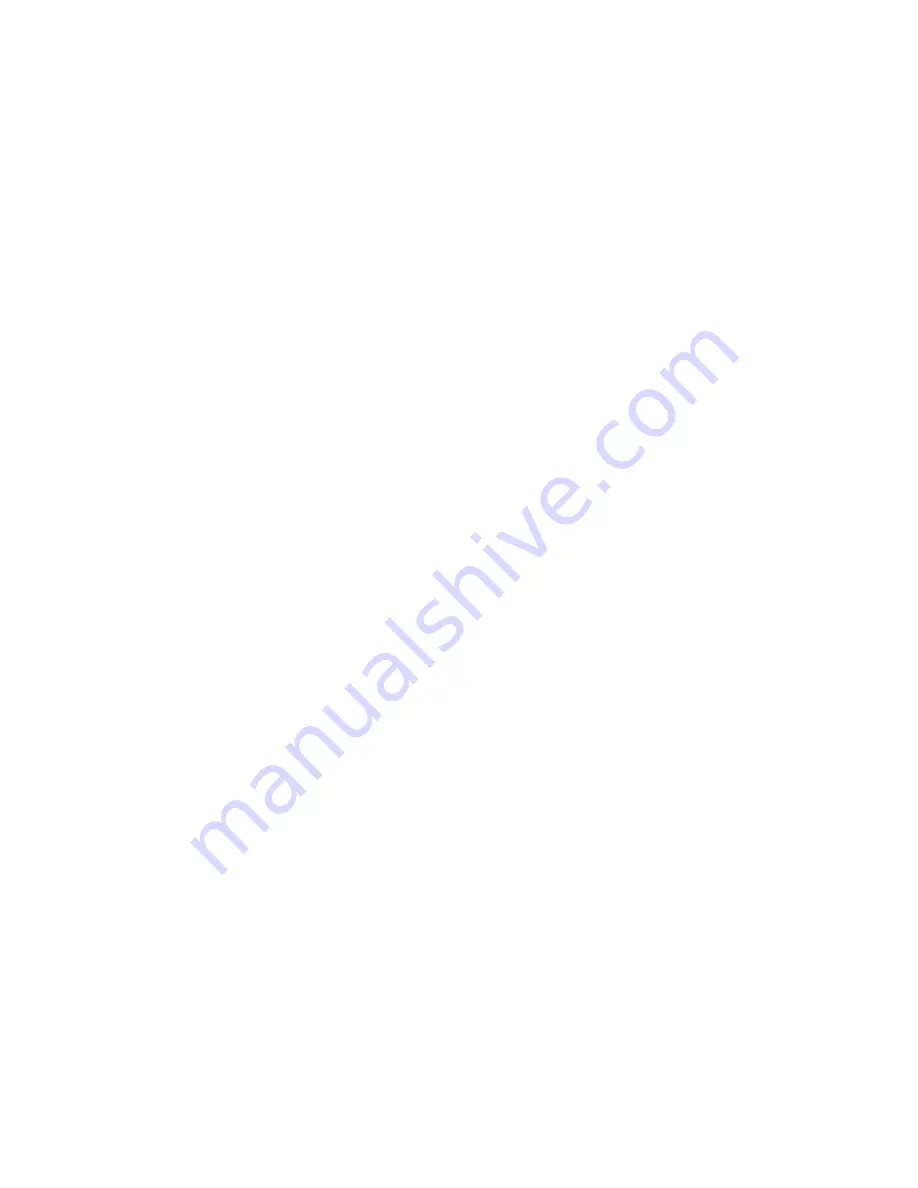
3
ABOUT THIS GUIDE
This document presents one approach to building the TTSH. There are other approaches that are perfectly
valid. This approach is designed to minimize the time for construction. These steps have been used to
successfully build a large number of TTSH units. Typical build time for the author, using this method, is
32 hours.
The TTSH is not a beginner’s project, and this guide assumes general knowledge of through hole
electronics construction on the part of the builder. It does not describe how to make solder joints, or how
to identify parts. It describes a certain order to install parts, and then test and calibrate the synth.
It cannot be overstated the importance of using a good quality, temperature-controlled soldering system
to build this project. There are 3175 solder connections to be made. Use of a craft grade iron will
exponentially increase the time to build, and result in countless connections of poor quality or non-
connections, and possible component damage. If your soldering skills are not well developed, you will
have gained proficiency by the end. If necessary, refer to videos on YouTube with explainers for through-
hole soldering technique, and the various fault scenarios to watch out for.
During the main board construction, the soldering is split into two phases. The first phase includes
immersible parts only. This is to facilitate a process using organic / water wash flux. This phase may also
be built with no clean flux.
This document lays out an approach to soldering that is considered best practice. When through hole
components are installed, the tailings for these parts are cut to length prior to soldering. The benefits of
this approach are two-fold. First, cutting after soldering can shock or damage solder joints. Second, waste
material removed and disposed of will not be contaminated with solder. This is of particular value if you
use solder containing lead.
Cutting and then soldering necessitates immobilizing components, or moving them into place as solder is
applied. Both methods are used here. The bulk of the solder joints will be formed using a backer board
to press components flush with the PCB. Various components are installed in groups, based on their
profile in relation to the PCB. For example, horizontally oriented resistors and diodes hug very close to
the board, and are installed in the first pass. This process will be described in detail further down.
Resistors and diodes that are vertically oriented, or located on the front side of the PCB (LED circuits) are
set aside at first, and installed later.
The board is silkscreened with component values, and not component numbers (ex: 1K, not R1). A
separate document has been produced showing the count of each component type and value (resistors,
diodes, capacitors and transistors) for each section of the synth. This will speed the builder up locating
footprints and installing the parts.
If you purchased the Synthcube kit, you received quantity 8 50mm M3 M-F nylon standoffs. These are
intended as stilts to raise the main board from your bench so through hole components can be stuffed.
These are used only during construction. If you purchased the BOM components yourself, it is
recommended you obtain these as well. Brass or aluminum standoffs work even better if you want to
spring for them.
Required non-kit items:
•
Temperature controlled Soldering system.