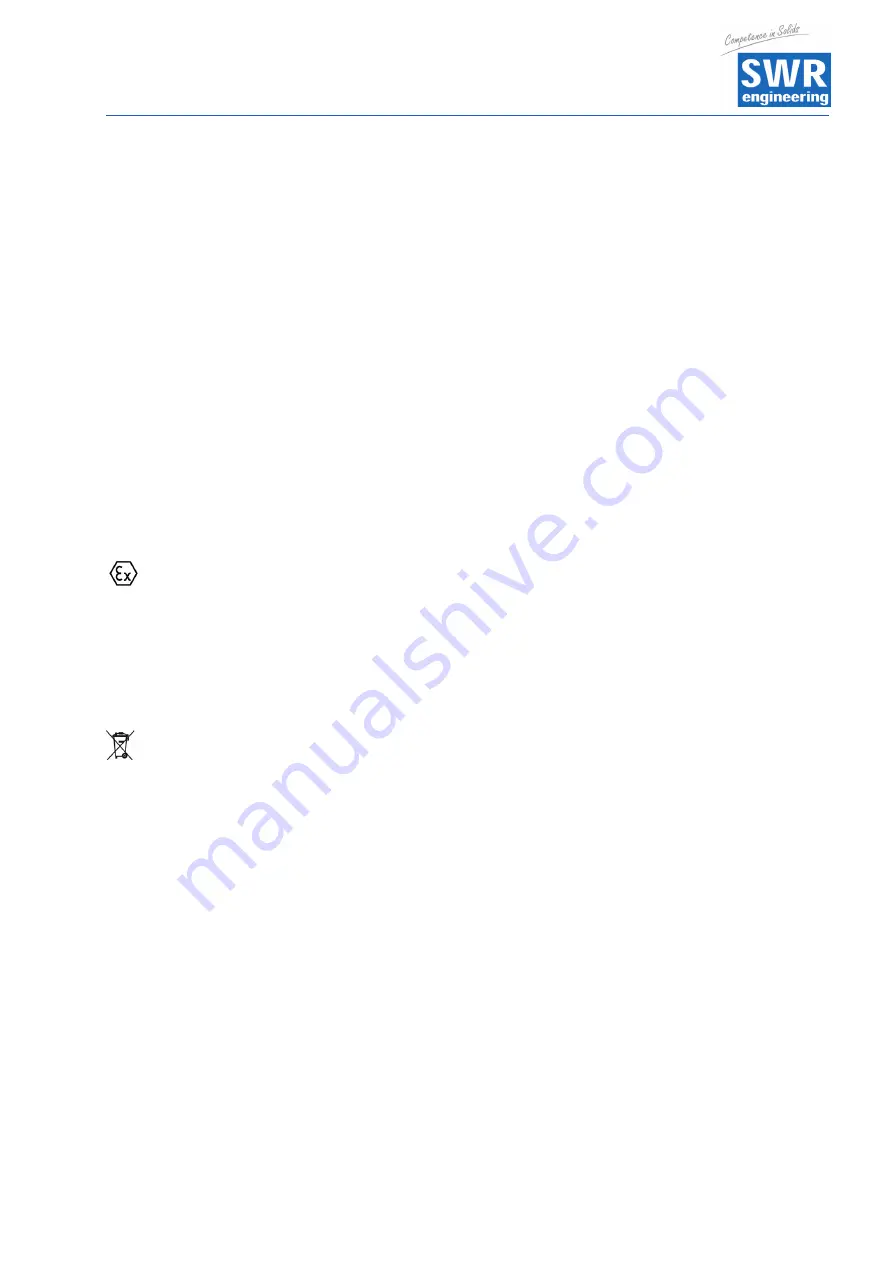
Operating Instructions
4
1. About this document
1.1 Function
This operating instructions provides you with the information you need for the installation, connection and
setup work and also contains important information about maintenance and troubleshooting.
You should therefore read it carefully before setup and keep it as an integral part of the product in the
immediate vicinity of the device so that it is accessible at all times.
1.2 Target group
This operating instructions is aimed at trained personnel.
The content of this manual must be made accessible to the personnel and implemented by them.
1.3 Symbols used
Information, Tip, Note
This symbol is used to mark helpful additional information.
Caution
Failure to observe this warning may result in faults or malfunctions.
Warning
Failure to observe this warning may result in personal injury and/or serious damage to the device.
Danger
Failure to observe this warning may result in serious personal injury and/or the destruction of the
device.
Applications in potentially explosive atmospheres
This symbol is used to mark special information for applications in potentially explosive atmospheres.
List
The initial dot denotes a list with no binding order.
Action
This arrow denotes a single action.
Action sequence
Preceding numbers denote actions to be performed in sequence.
Battery disposal
This symbol is used to mark special information for the disposal of batteries.
2. For your safety
2.1 Authorised personnel
All the actions described in this operating instructions may only be carried out by trained personnel who have
been authorised by the system owner/operator.
The requisite personal protection equipment must be worn at all times when work on and with the device.
2.2 Intended use
The Nico 15/30 is a sensor for the continuous measurement of fi ll levels.
Detailed information about its area of application is provided in the section entitled "
Product description
".
The device is only safe to use if it is used for the purpose for which it is intended and as described in the
operating instructions and any supplementary manuals.
2.3 Warning about misuse
If the device is not used correctly or is used for purposes other than that for which it is intended, it may cause
danger, for example the overfl ow of the vessel or damage to system parts due to incorrect installation or
setting.
●
→
1
r
!