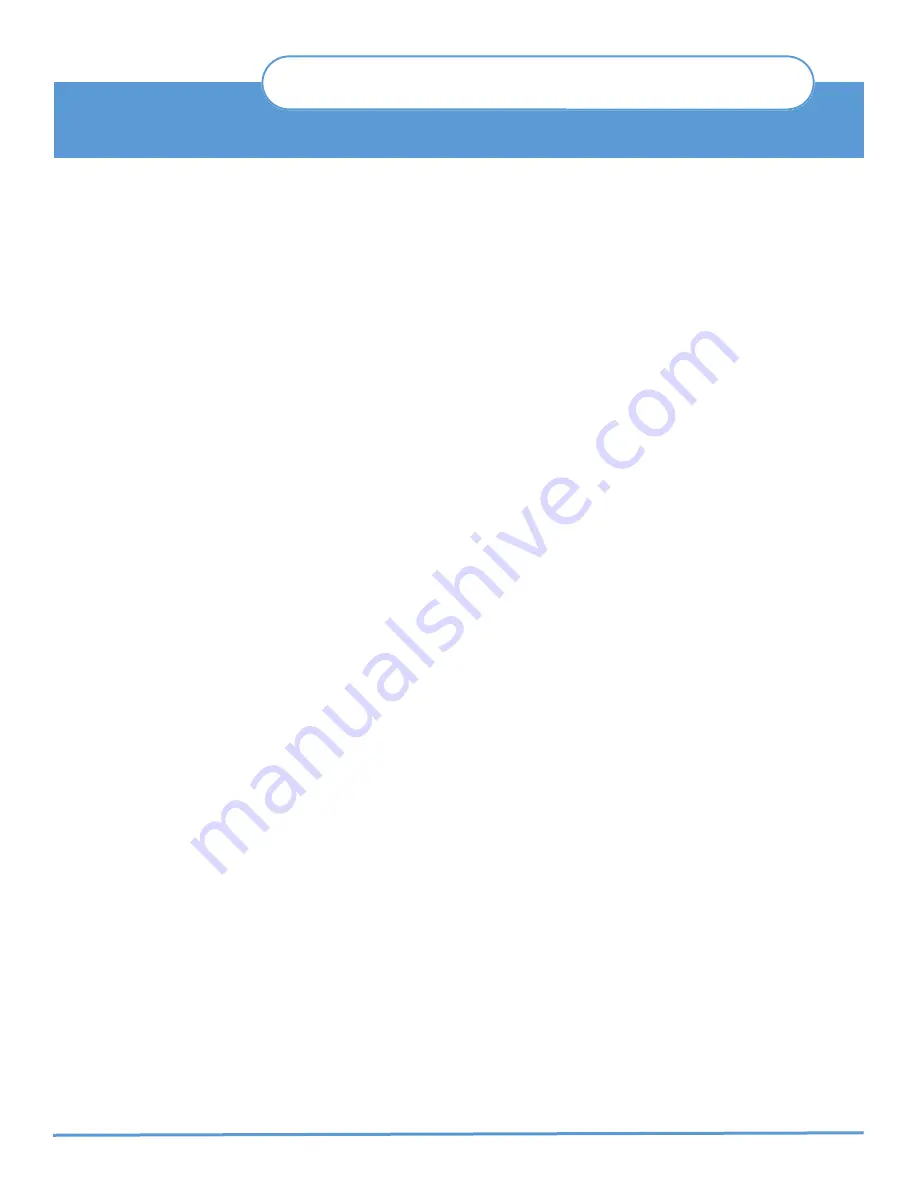
28
INTERMITTENT
PILOT
OPERATION
Ignition Process - Intermittent Pilot
1) Unlock system
2) Set desired parameters
3) Press the ON button
4) Pre-purge on Start-up- 60 second countdown displayed -
Green LED ON
5) Audible Alarm - 5 second countdown displayed -
Green LED ON
6)
Igniter - 8 second countdown displayed -
Green and Amber LED ON
7) Stage 1 Solenoid/Actuator valve opens - igniter remains on -
Green and Amber LED ON
8) Ignition is achieved, flame is sensed -
Green and Blue LED ON
9) Stage 2 solenoid valve opens - timing between solenoids expires -
Green and Blue LED ON
10) Unit is now running - Status code 00 -
Green and Blue LED ON
11) Process Temperature exceeds High Temp Set point - Stage 1 and Stage 2 solenoids close -
Green LED ON
12) Process Temperature reduced to Low Temp Set point -
Restart at step 5
Re-Ignition Process - No Flame Sensed
1) Once the system recognizes that no flame is sensed, the system will automatically begin the ignition
process.
2) Purge between ignition attempt - 120 second countdown -
Green LED ON
3) Reference step 5 - 12 in the “Ignition Process Section”
NOTE: If system fails to prove a flame on the fourth attempt, the system shuts down on code 12.
Blinking Red LED
Re-Ignition Process - Standby
1) System in Standby -
Blinking Green LED
2) Once the system resolves the Standby issue, the system will automatically begin the ignition process.
2)
Pre-purge on Start-up - 120 second countdown -
Green LED ON
3) Reference step 5 - 12 in the “Ignition Process Section”
Re-Ignition Process - Shutdown
1) The system requires manual reset in the event of a shutdown.
2) System in Shutdown -
Blinking Red LED
3)
Once the Shutdown issue is resolved, manual reset is required. Press the OFF and ON button to reset.
4)
Pre-purge on Start-up - 120 second countdown -
Green LED ON
5) Reference step 5 - 12 in the “Ignition Process Section”
Summary of Contents for BMS-350
Page 1: ...Proudly Made in the USA BMS 350 Installation and Operations Manual...
Page 18: ...18 INSTALLATION WIRING DIAGRAM...
Page 19: ...19 FUEL TRAIN DIAGRAMS Piloted Fuel Train Pilotless Fuel Train...
Page 29: ...29 INTERMITTENT PILOT OPERATION Flow Chart...
Page 31: ...31 STANDING PILOT OPERATION Flow Chart...