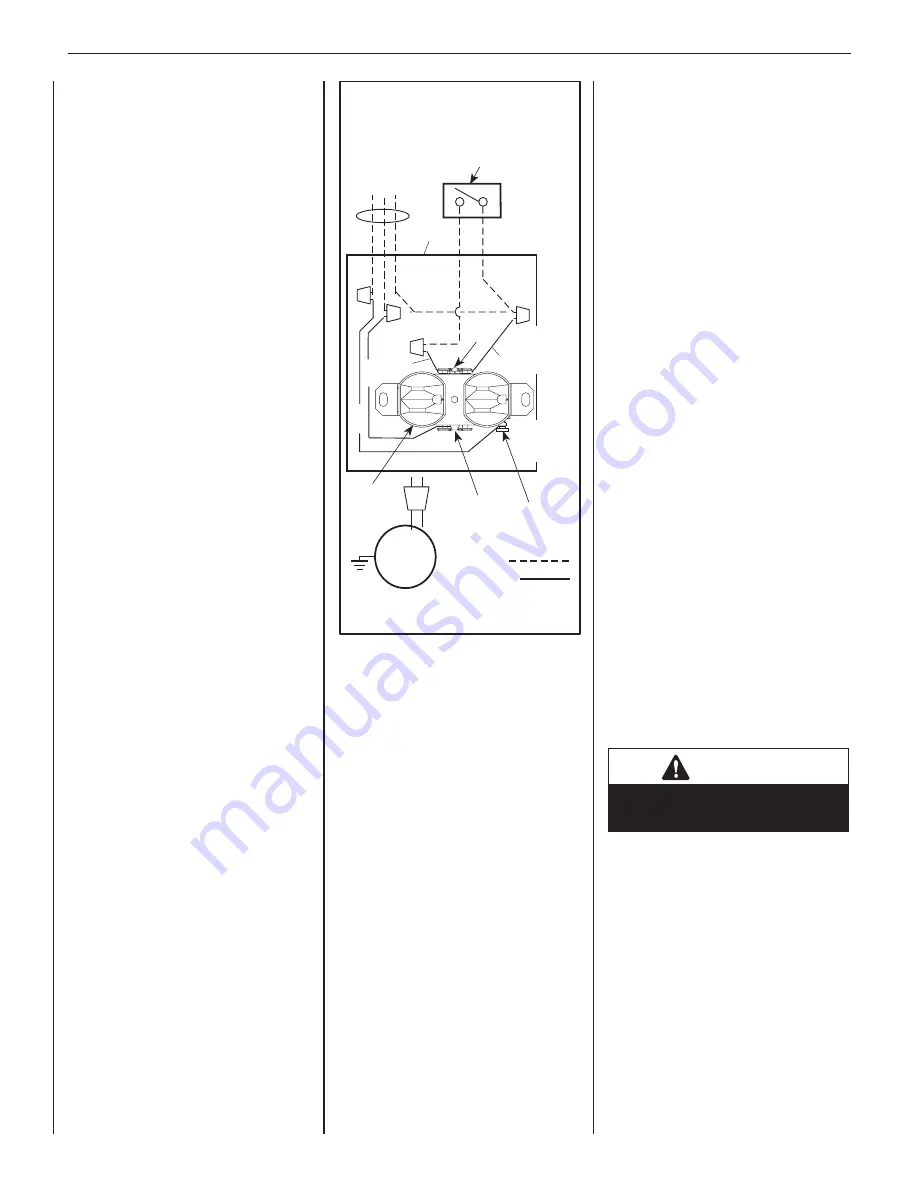
26
NOTE: DIAGRAMS & ILLUSTRATIONS ARE NOT TO SCALE.
SUPERIOR
®
• DIRECT-VENT GAS FIREPLACES (SDV35-N-2) • INSTALLATION INSTRUCTIONS
Note: Remote receiver should be located
in the wall, or if installed in the control
compartment, pulled all the way forward and
completely to the left or right against the
corner posts.
6.
If wall-mounted ON/OFF control or
thermostat is to be used, mount it in a
convenient location on a wall near the
fireplace.
7
. If an optional control is to be used, wire
it in the low voltage circuit as shown in
Figure 47.
Note: The supplied 15 feet of 2 conductor
wire has one end of each conductor
connected to the gas valve circuit and the
other end of each conductor placed loose
inside the bottom compartment.
8
. After the wiring is complete, replace the
cover plate.
BLOWER CONTROL CIRCUIT WIRING
120V, 60HZ, 1PH
Factory Wired
Ground
Field Wired
Junction Box
Tab Intact
Tab
Broken
Plug blower
into this
receptacle
ne
er
G -
dn
uor
G
* Wall-mounted
ON/ OFF Blower
Switch or Variable
Speed Control Switch.
Blower
eti
h
W -
lar
tu
eN 120 VAC - Blac
k
Green
Ground
Screw
Whit
e
Gree
n
Neutral
Side of
Receptacle
Hot
Side of
Receptacle
Red
Black
Figure 47: Detailed Junction
Box Wiring
This appliance is equipped with a gas flex line
for use (where permitted) in connecting the
unit to the gas line. A gas flex line is provided
to aid in attaching the direct vent appliance
to the gas supply. The gas flex line can only
be used where local codes permit. Refer to
Figure 47
for flex line description. The flex
line is rated for both natural and propane gas.
A manual shut off valve is also provided with
the flex line.
The gas control valve is located in the lower
control compartment.
To access the valve open the lower control
compartment door (
see Figure 48
) by
pushing in the right top corner of the door.
(The door is hinged at the bottom.) Remove
the bottom compartment door by sliding
the hinge pin, located at the door’s left side,
to the right until it disengages from the left
corner post hole. Pull the door diagonally to
the left, away from the fireplace.
The control valve has a 3/8 in.
(10 mm) NPT thread inlet port.
Secure all joints tightly using appropriate
tools and sealing compounds (ensure
propane resistant compounds are used
in propane applications). Optional: Seal
around the gas line to prevent cold air
leakage. Gas line holes and other openings
can be caulked or stuffed with unfaced
fiberglass insulation.
All codes require a shut-off valve mounted
in the supply line. The orientation of
the shut-off valve should face the front.
Figure 47
illustrates two methods for
connecting the gas supply. A sediment Trap
is recommended to prevent moisture and
debris in the gas line for damaging the valve.
FBK-250 Blower Kit
(See Figure 46 on Page 25)
An electrical outlet box is provided for the
installation of the
FBK-250
forced air blower
kit. Electrical power must be provided to this
box to operate this blower. The blower kit
has been factory installed according to the
installation instructions provided with the kit.
Note: The tab connecting the receptacles of
the outlet box must be broken in FBK-100
and FBK-200 blower kit applications. See
Figure 47
.
Step 7. CONNECTING GAS LINE
Make gas line connections. All codes require
a shut-off valve mounted in the supply
line.
Figure 48
illustrates two methods for
connecting the gas supply. The flex-line
method is acceptable in the U.S., however,
Canadian requirements vary depending on
locality. Installation must be in compliance
with local codes.
Step 6.
WIRING—STANDARD FORCED
AIR BLOWER KIT
FBK-100 and FBK-200 Kits
(See Figure 45 on Page 25)
An electrical outlet box is provided for the
installation of the
FBK-100
,
FBK-200
forced
air blower kit. Electrical power must be
provided to this box to operate this blower.
The blower kit has been factory installed
according to the installation instructions
provided with the kit.
WARNING
Never use an open flame to
check for leaks.
f i r e - p a r t s . c o m