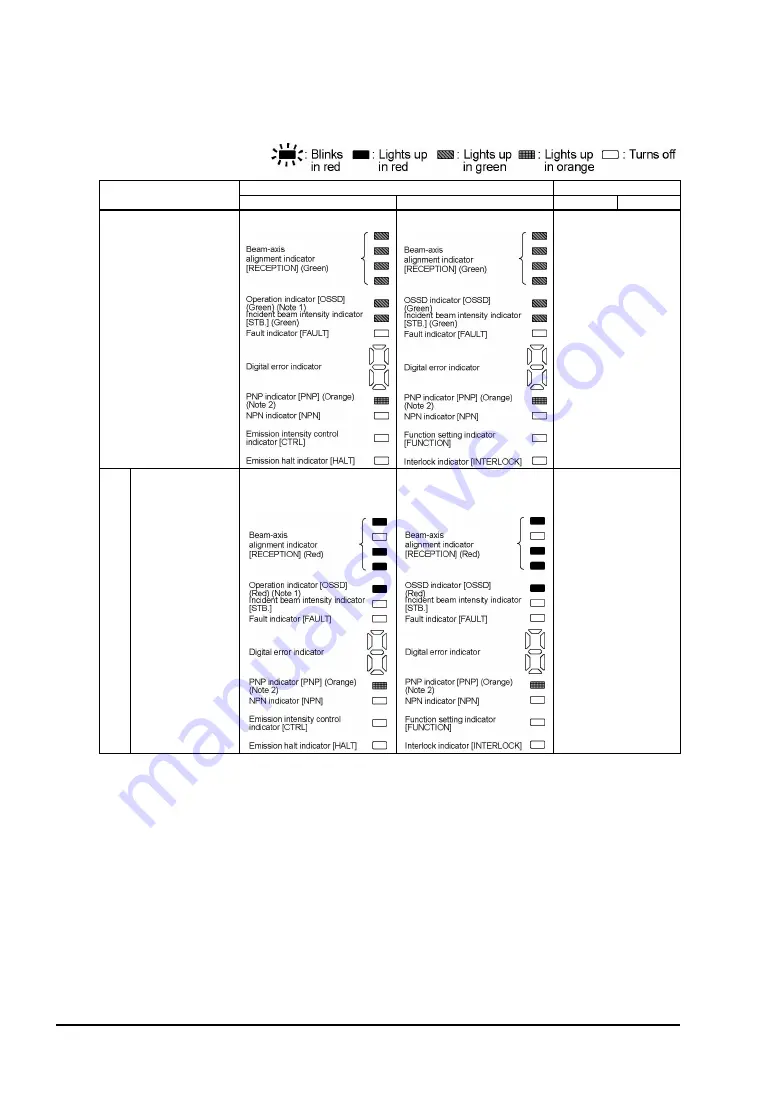
SUNX Limited MJE-SF4B01 No.0005-03V
- 60 -
2-6-3 Operation
1) Normal Operation
The status of the emitter / receiver indicators during normal operation is as described below.
Indicators Control
output
Device status
Emitter
Receiver
OSSD 1
OSSD 2
Beam received status
(all beams received)
Lights up in green
Lights up in green
ON
Be
am b
lo
c
k
e
d
stat
u
s
One or more
beams
blocked
Lights up in red
(OFF for beam blocked
channels)
Lights up in red
(OFF for beam blocked
channels)
OFF
Notes: 1) Since the color of the operation indicator changes according to the ON / OFF state of the control
output (OSSD 1, OSSD 2), the operation indicator is marked as OSSD on the sensor.
2) The status of the emitter / receiver indicators during operation above shows the case in PNP output
setting mode. In case of NPN output setting mode, the NPN indicator (orange) lights up.