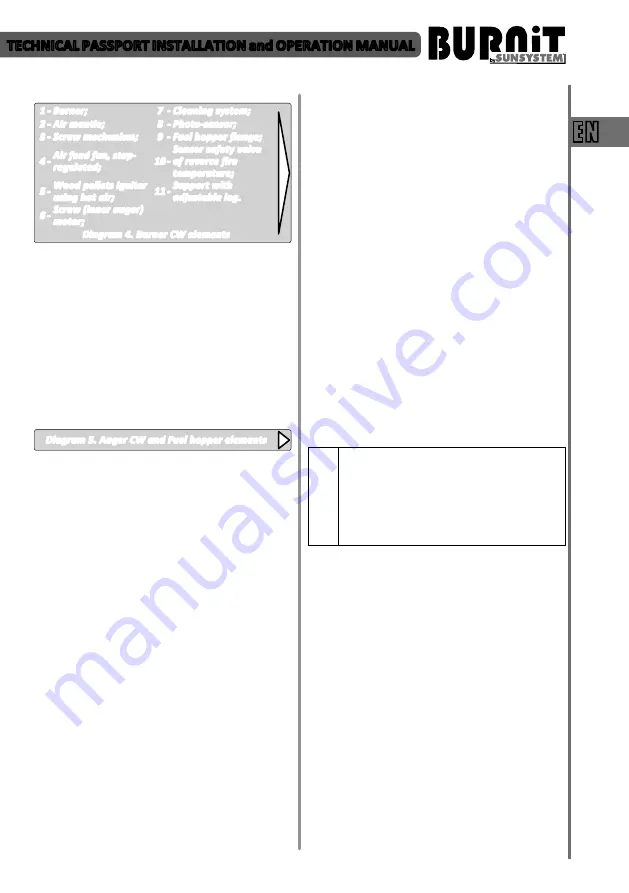
5
EN
TECHNICAL PASSPORT INSTALLATION and OPERATION MANUAL
Elements of pellet burner are:
1 - Burner;
7 - Cleaning system;
2 - Air mantle;
8 - Photo-sensor;
3 - Screw mechanism;
9 - Fuel hopper flange;
4 - Air feed fan, step-
regulated;
10 -
Sensor safety valve
of reverce fire
temperature;
5 - Wood pellets igniter
using hot air;
11 - Support with
adjustable leg.
6 - Screw (inner auger)
motor;
Diagram 4. Burner CW elements
2.4. Design of auger mechanism and fuel hopper (wood
pellets) /Diagram 5/
It consists of a spiral conveyor mounted to the axle, driven by
motor reducer, which is attached to the body of the auger.
Auger and fuel hopper are connected by medial flange.
Temperature safety valve
(3)
is connected to a water tank
(2)
and in case of reverce flame in auger, releace the water into
the medial flange
(4)
, located between auger
(5)
and fuel
hopper
(1)
and prevent fuel firing.
Convinient maintenance openings are provided on auger
mechanism and on medial flange.
The hopper hatch-cover remains to be closed during
operation of boiler.
The water tank
(2)
must be filled when boiler is operating.
Diagram 5. Auger CW and Fuel hopper elements
2.5. Boiler safety devices
Safe operation of boiler is ensured via a set of safety devices.
Combustion process is electronically regulated via step
modulation of burner performance according to power
needs, and also maintained in optimum working mode. Two
independent thermostats – that on the boiler (
STB type
) and
the one on the auger mechanism (
bimetallic thermostat set
at 80°С
) would stop the fuel feeding into the burner in case
of excess temperature load.
In addition, the burner has a supplementary heat safety
valve (
with sensor mounted on auger housing)
connected
to an extra water tank of volume 10 litres (mounted on the
back side of hopper housing and pipe-connected to auger
mechanism) capable to put out a backfire flame should one
emerge inside auger tube or hopper.
•
Fuse
. In case of electrical fault in the system of the burner
(short circuit, current overload, etc.), the overload is borne
by the electrical fuse fitted on the main control panel of the
burner (3,15 А).
•
Power interruption.
In case of power interruption, all
parameter settings are stored in the memory of the
controller. Upon the subsequent restart of the burner, the
controller resumes the execution of the program from the
point when the power interruption occurred.
3. FUELS
3.1. Wood pellets
All pellets are biomass manufactured from common low-
growing plants and trees. The most common household
type pellets are made of sawdust and milled wood chippings
which are waste material from wood used in the production
of logs, furniture and other products. Wood is the richest raw
material which does not have any impact on the production
costs of food products or ethyl alcohol (ethanol). The raw
material is processed under high-pressure and temperature
and is pressed to produce small-size cylindrical pellets. The
production process may utilize soft wood material (such as
softwood, pine), hardwood (oak) as well as recycled waste
wood. Wood pellets are produced in hammer mills or wood
pellet plants.
Advantages of wood pellets:
•
Convenient storage.
Pellet bags can be stored on a small
area in a dry garage, basement, service room or shed.
•
Easy loading.
In most cases the boiler hopper needs
loading only once a week – this depends on the hopper
capacity.
•
Better control of fuel quantity.
The small size of the pellets
allows for precise fuel feeding. On the other hand, the
supply of air for reaching optimal combustion efficiency is
easier to adjust since the fuel quantity in the combustion
chamber remains constant and predictable.
•
Fuel efficiency.
High combustion efficiency is also
determined by consistently low moister content of
pellets (consistently under 10% as opposed to 20% to
60% moisture content of the logs). Low moisture content,
controlled fuel portions and precise air setting means high
combustion efficiency and very low carbon oxides in the
flue gases.
i
When purchasing pellets, ask for conformity
declaration and certificate issued by an accredited
laboratory and make sure the fuel meets the
requirements indicated in the manual. If you
purchase large amount of pellets (bulk supply for
the entire heating season for example), ask your
supplier to provde accurate and true information
about the storage conditions.
We recommend to use pellet with size of
6 - 8 mm
. Density
600 - 750 kg/m³
heating value
4,7 - 5,5 kWh/kg
. Ash content
– less than
1%
and moisture content up to
8%
,
EN 14961-
2:2011
.
The optimal density of the pellets which guarantees their
quality is
605 - 700 kg
per cubic meter.
Pellet moisture content must not exceed 10%. Make sure
you store your fuel in a dry and well-ventilated place.
The optimal pellet ash content is
≤ 1%
. This also provides for
less frequent cleaning intervals for the burner.
The table below contains the parameters which we
recommend that you take into consideration when choosing
fuel for your burner.
Summary of Contents for BURNIT CombiBurn DC-A Series
Page 65: ...65 65 1 3 2 4 9 2 4 5 11 10 8 9 6 7...
Page 66: ...66 66 5 6 7 3 1 2 5 4...
Page 67: ...67 67 8...
Page 69: ...69 69 10 11...
Page 70: ...70 70 12...
Page 71: ......