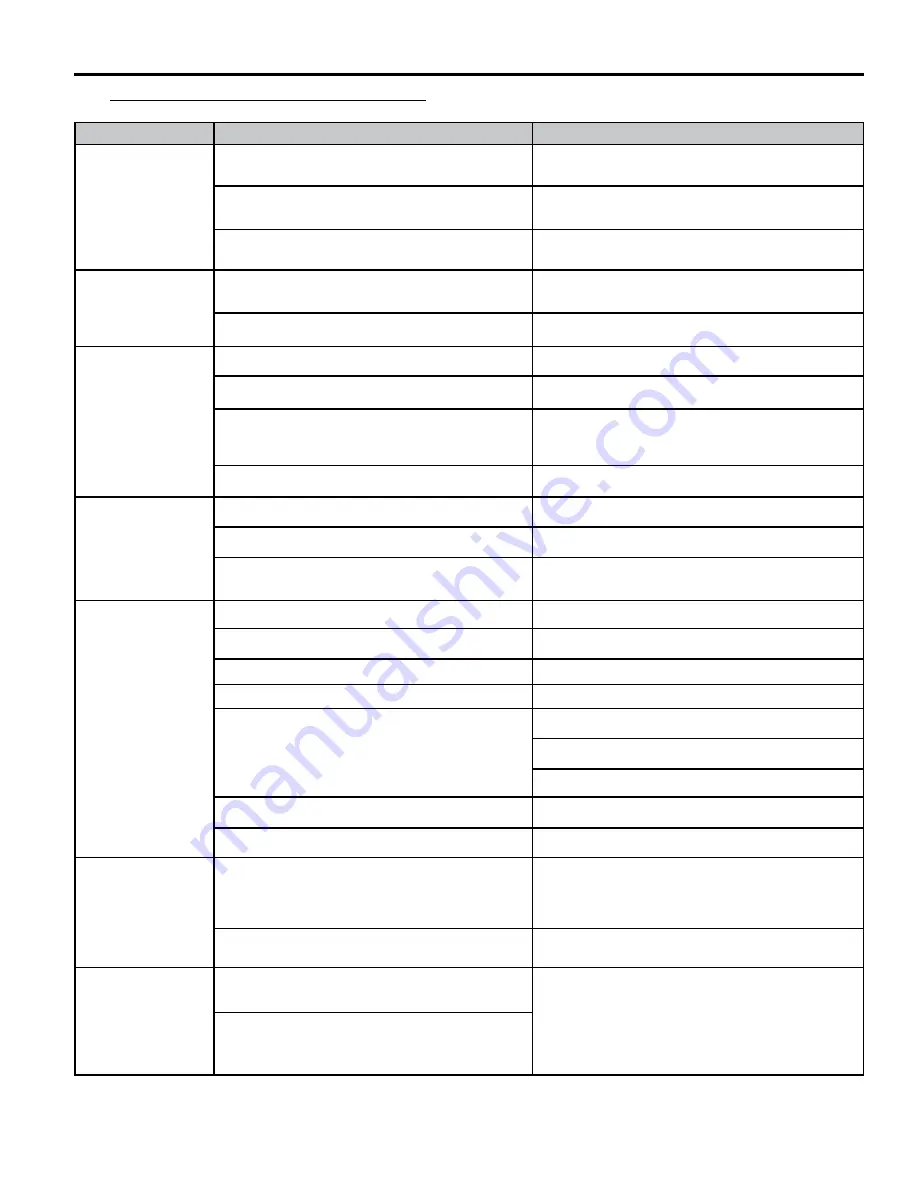
SECTION 4 - TROUBLESHOOTING
4.5
4.2. MECHANICAL TROUBLESHOOTING
PROBLEM
PROBABLE CAUSE
CORRECTION
8. Boom doesn’t
break away.
A. Outer boom fold switch not turned off.
Outer boom fold switch must be turned off for the break
away to function.
B. Blocking valve on outer boom fold cylinder not
working.
Verify that blocking valve is normally open.
C. Accumulator malfunction.
Check for nitrogen pressure in accumulator. Replace or
recharge.
9. Spray height is not
correct.
A. Hydraulic cylinder adjustment incorrect.
Activate vertical height circuit and raise or lower
booms.
B. Booms not level.
Adjust inner boom top clevis to level booms. Refer to
section 2.5.
10. Booms do not
go into transport
rests.
A. Sprayer is on uneven terrain.
Move sprayer to level location.
B. Inner boom spring cushion is out of adjustment.
Adjust inner boom fold spring cushion. Refer to sec-
tion 2.4 and see note.
C. Inner boom spring cushion assembly is out of
adjustment.
Adjust inner boom fold spring cushion assembly. Refer
to section 2.6.
D. Inner boom eyebolt bent or broken.
Adjust or replace inner boom eyebolt.
11. Booms do not
self-level.
A. Travel speed too fast for terrain.
Loosen bolts so boom can move as needed.
B. Swing arms are not greased.
Lubricate swing arms and parallel links.
C. Wear plates are rubbing guides hard.
Check for worn pivot bolts or adjust boom wear plate
guides.
12. Booms contact
ground often.
A. Terrain too rough or uneven.
Slow down to allow sprayer time to react.
B. Terrain too rough for suspended boom.
Raise booms.
C. Sprayer and tractor unstable.
Spread out wheel c-c’s to gain stability.
D. Booms do not self level.
See problem 11 above.
E. Boom suspension does not work properly.
Check and adjust accumulator pressure.
Correct parallel link binding.
Grease parallel link pivots.
F. Improper tire pressure.
Adjust tire pressures to specifications.
G. Booms are not level in spray position.
Level both booms and recheck.
13. Innter booms
won’t fold out
A. Malfunctioning Safety Switch Circuit
a) Check Safety Switch above RH Part 2 Fold Cylinder
for proper adjustment.
b) Check connector in wiring harness located by RH
Tip Lift Cylinder.
B. Broken Eye-Bolt (operator isn’t able to see this
from the cab)
Replace broken Eye-Bolt.
14. Outer booms
won’t fold in
A. Weak or non-functioning solenoid on either or
both part 2 fold cylinders
Verify voltage and correct operation of all 4 solenoids
in this circuit. 2 on main block & on on each cylinder.
B. Low voltage from tractor (this circuit takes more
power than any of the other circuits because it’s
using 4 solenoids at the same time)
Summary of Contents for ULTIMATE NT
Page 12: ...1 6 SECTION 1 SAFETY 14 PN 8Z0290 SINGLE TANK PLUMBING DECAL 13 PN 8Z0288 RINSE TANK DECAL ...
Page 26: ... 2 12 ...
Page 27: ... 2 13 ...
Page 46: ...SECTION 3 MAINTENANCE 3 4 NOTES ...
Page 54: ...SECTION 5 ELECTRICAL 5 2 ...
Page 55: ...SECTION 5 ELECTRICAL 5 3 BOOM FOLD TIPLIFT END NOZZLE HEIGHT VERTICAL ...
Page 56: ...SECTION 5 ELECTRICAL 5 4 ...
Page 57: ...SECTION 5 ELECTRICAL 5 5 ...
Page 58: ...SECTION 5 ELECTRICAL 5 6 ...
Page 59: ...SECTION 5 ELECTRICAL 5 7 ...
Page 60: ...SECTION 5 ELECTRICAL 5 8 ...
Page 116: ...SECTION 8 PARTS 8 42 ...
Page 120: ...SECTION 8 PARTS 8 46 ...
Page 154: ...SECTION 8 PARTS 8 81 SECTION 8 PARTS ...
Page 162: ...SECTION 8 PARTS 8 89 SECTION 8 PARTS ...
Page 163: ...8 90 SECTION 8 PARTS SECTION 8 PARTS ...
Page 164: ...SECTION 8 PARTS 8 91 SECTION 8 PARTS ...
Page 165: ...SECTION 8 PARTS 8 92 SECTION 8 PARTS ...
Page 166: ...SECTION 8 PARTS 8 93 SECTION 8 PARTS ...
Page 167: ...SECTION 8 PARTS 8 94 SECTION 8 PARTS ...
Page 168: ...SECTION 8 PARTS 8 95 SECTION 8 PARTS ...
Page 169: ...SECTION 8 PARTS 8 96 SECTION 8 PARTS ...