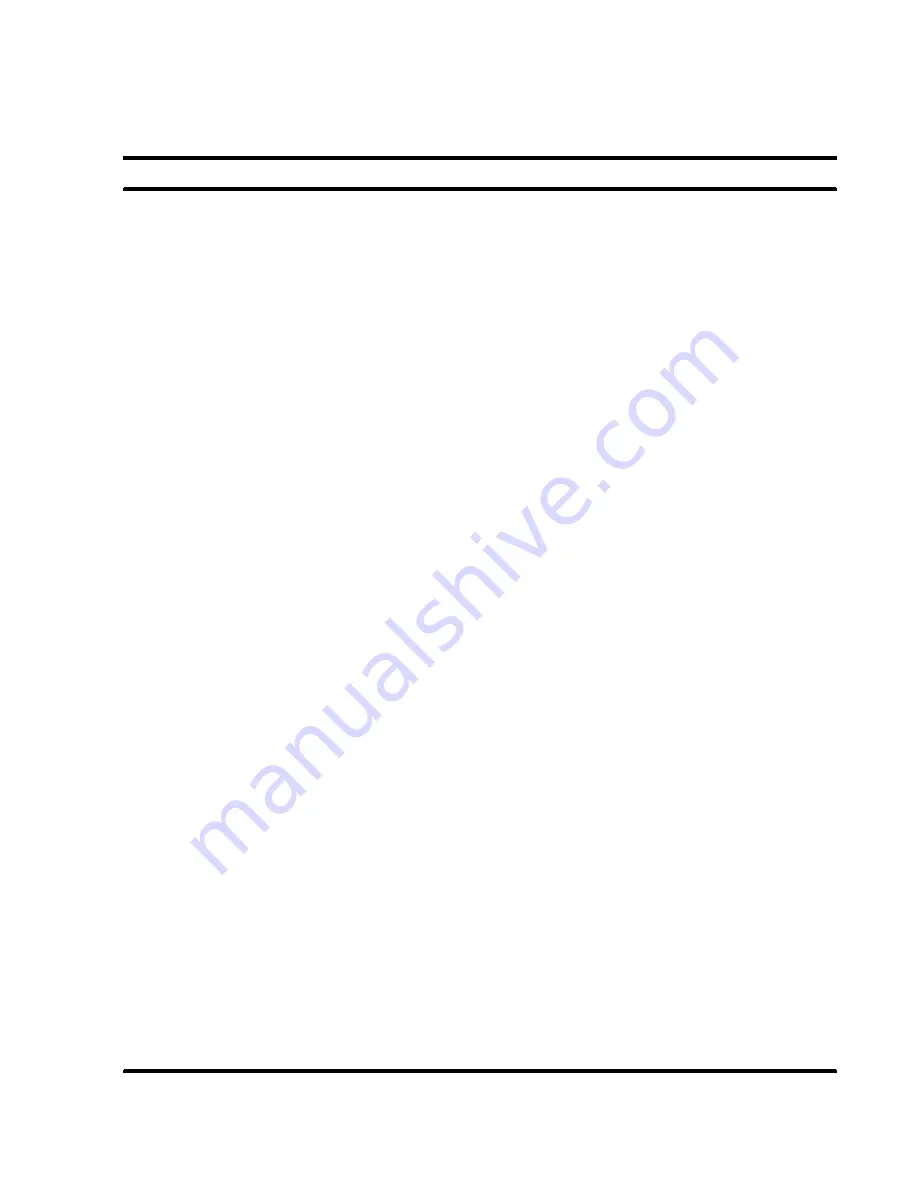
Section 5
COMPRESSOR OPERATION
18
5.2 PURPOSE OF CONTROLS -- STANDARD (CONTINUED)
CONTROL OR INDICATOR
PURPOSE
LINE PRESSURE GAUGE
Continually monitors service line air pressure.
DISCHARGE TEMPERATURE GAUGE
Monitors temperature of the air/fluid mixture dis-
charged from the compressor unit. For air--cooled
compressors normal reading is approximately 185
_
F
(85
_
C ) with a 70
_
F (21
_
C) ambient temperature.
FLUID FILTER MAINTENANCE GAUGE
Indicates when a filter element change is required.
FLUID SEPARATOR MAINTENANCE GAUGE
Indicates when separator element change is required.
AIR FILTER MAINTENANCE INDICATOR
Shows red when air filter element servicing is required.
This indicator must be manually reset after servicing
filter.
PRESSURE REGULATOR
Opens a pressure line between the sump and air inlet
valve allowing the inlet valve to regulate air delivery ac-
cording to demand.
FLUID LEVEL SIGHT GLASS
Indicates fluid level in the sump. Proper level is not to
fall below the center of the sight glass. Check level
when compressor is shut down.
DO NOT OVERFILL.
COOLER BYPASS VALVE
Regulates flow of fluid to and around the cooler.
Designed to maintain a minimum operating
temperature of 185
_
F (85
_
C); used for fast
warm--up on start--up.
MINIMUM PRESSURE/CHECK VALVE
Maintains minimum of 50 psig (3.4 bar) in the compres-
sor sump. Valve piston restricts receiver air discharge
from receiver/sump when pressure falls to 50 psig (3.4
bar). Also incorporated in this valve is a terminal check
valve which prevents line pressure backflow into the
sump during unload conditions and after shutdown.
DISCHARGE TEMPERATURE SWITCH
Shuts the compressor down when the discharge tem-
perature exceeds 240
_
F (116
_
C).
PRESSURE RELIEF VALVE
Protects compressor by venting compressed air in ex-
cess of 200 psig (13.8 bar) to atmosphere.
MODULATING INLET VALVE
Regulates the amount of air allowed to enter the air
compressor. This regulation is determined by the
amount of air being used at the service line. Also acts
as a check valve to prevent reverse compressor rota-
tion at shut down.
SOLENOID VALVE
Bypasses the pressure regulator valve causing the in-
let valve to close when the compressor reaches maxi-
mum operating pressure. Also activates blowdown
valve.
WATER REGULATING VALVE
Regulates the amount of cooling water used in the
(water--cooled only)
cooler to keep the the compressor running at a normal
operating temperature of 185
_
F (85
_
C).
SUMP PRESSURE GAUGE
The sump pressure gauge is used to determine at start--
up whether proper electrical connections were made for
motor rotation. An immediate pressure reading indicates
proper rotation of the compressor unit. It can also be
used to verify a pressure drop in the system.
Summary of Contents for ES-11 SERIES
Page 6: ...NOTES...
Page 13: ...Section 2 INSTALLATION 7 Figure 2 1 Service Air Piping...
Page 14: ...8 NOTES...
Page 18: ...Section 4 COMPRESSOR SYSTEMS 12 Figure 4 1A Description of Components...
Page 19: ...Section 4 COMPRESSOR SYSTEMS 13 AIR COOLED WATER COOLED Figure 4 1B Description of Components...
Page 22: ...Section 4 COMPRESSOR SYSTEMS 16 Figure 4 3 Pneumatic Control System Standard Supervisor II...
Page 30: ...24 NOTES...
Page 34: ...28 NOTES...
Page 40: ...Section 7 MAINTENANCE 34 Figure 7 6 Cooler Cleaning COOLER SHROUD COMPRESSOR ENCLOSURE COOLER...
Page 42: ...36 NOTES...
Page 48: ...42 NOTES...
Page 50: ...Section 9 ILLUSTRATIONS AND PARTS LIST 44 9 3 FRAME MOTOR COMPRESSOR AND PARTS...
Page 52: ...Section 9 ILLUSTRATIONS AND PARTS LIST 46 9 4 COMPRESSOR AND PARTS 44...
Page 54: ...Section 9 ILLUSTRATIONS AND PARTS LIST 48 9 4 COMPRESSOR AND PARTS 44...
Page 56: ...Section 9 ILLUSTRATIONS AND PARTS LIST 50 9 5 MOTOR AND PARTS...
Page 60: ...Section 9 ILLUSTRATIONS AND PARTS LIST 54 9 7 COOLING SYSTEM AND PARTS AIR COOLED...
Page 62: ...Section 9 ILLUSTRATIONS AND PARTS LIST 56 9 7 COOLING SYSTEM AND PARTS AIR COOLED...
Page 64: ...Section 9 ILLUSTRATIONS AND PARTS LIST 58 9 8 COOLING SYSTEM AND PARTS WATER COOLED...
Page 66: ...Section 9 ILLUSTRATIONS AND PARTS LIST 60 9 8 COOLING SYSTEM AND PARTS WATER COOLED...
Page 68: ...Section 9 ILLUSTRATIONS AND PARTS LIST 62 9 8 COOLING SYSTEM AND PARTS WATER COOLED...
Page 70: ...Section 9 ILLUSTRATIONS AND PARTS LIST 64 9 9 CONTROL BOX AND PARTS STANDARD NOTE...
Page 72: ...Section 9 ILLUSTRATIONS AND PARTS LIST 66 9 9 CONTROL BOX AND PARTS STANDARD NOTE...
Page 74: ...Section 9 ILLUSTRATIONS AND PARTS LIST 68 9 9 CONTROL BOX AND PARTS STANDARD NOTE...
Page 76: ...Section 9 ILLUSTRATIONS AND PARTS LIST 70 9 9A CONTROL BOX AND PARTS SUPERVISOR II NOTE...
Page 78: ...Section 9 ILLUSTRATIONS AND PARTS LIST 72 9 9A CONTROL BOX AND PARTS SUPERVISOR II NOTE...
Page 80: ...Section 9 ILLUSTRATIONS AND PARTS LIST 74 9 9B CONTROL PANEL AND PARTS ELECTRO MECHANICAL...
Page 82: ...Section 9 ILLUSTRATIONS AND PARTS LIST 76 9 10 CANOPY ACOUSTICAL PANELS AND PARTS...
Page 84: ...Section 9 ILLUSTRATIONS AND PARTS LIST 78 9 10 CANOPY ACOUSTICAL PANELS PARTS...
Page 86: ...Section 9 ILLUSTRATIONS AND PARTS LIST 80 9 11 DECAL GROUP 1 2 3 4 5 6 02250077 472 2A...
Page 88: ...Section 9 ILLUSTRATIONS AND PARTS LIST 82 9 11 DECAL GROUP 8 9 10 11 12 13 7...
Page 91: ...Section 9 ILLUSTRATIONS AND PARTS LIST 85 9 13 WIRING DIAGRAM FULL VOLTAGE SUPERVISOR II...
Page 93: ...Section 9 ILLUSTRATIONS AND PARTS LIST 87 9 15 WIRING DIAGRAM WYE DELTA 50 60 HZ SUPERVISOR II...
Page 97: ...NOTES...