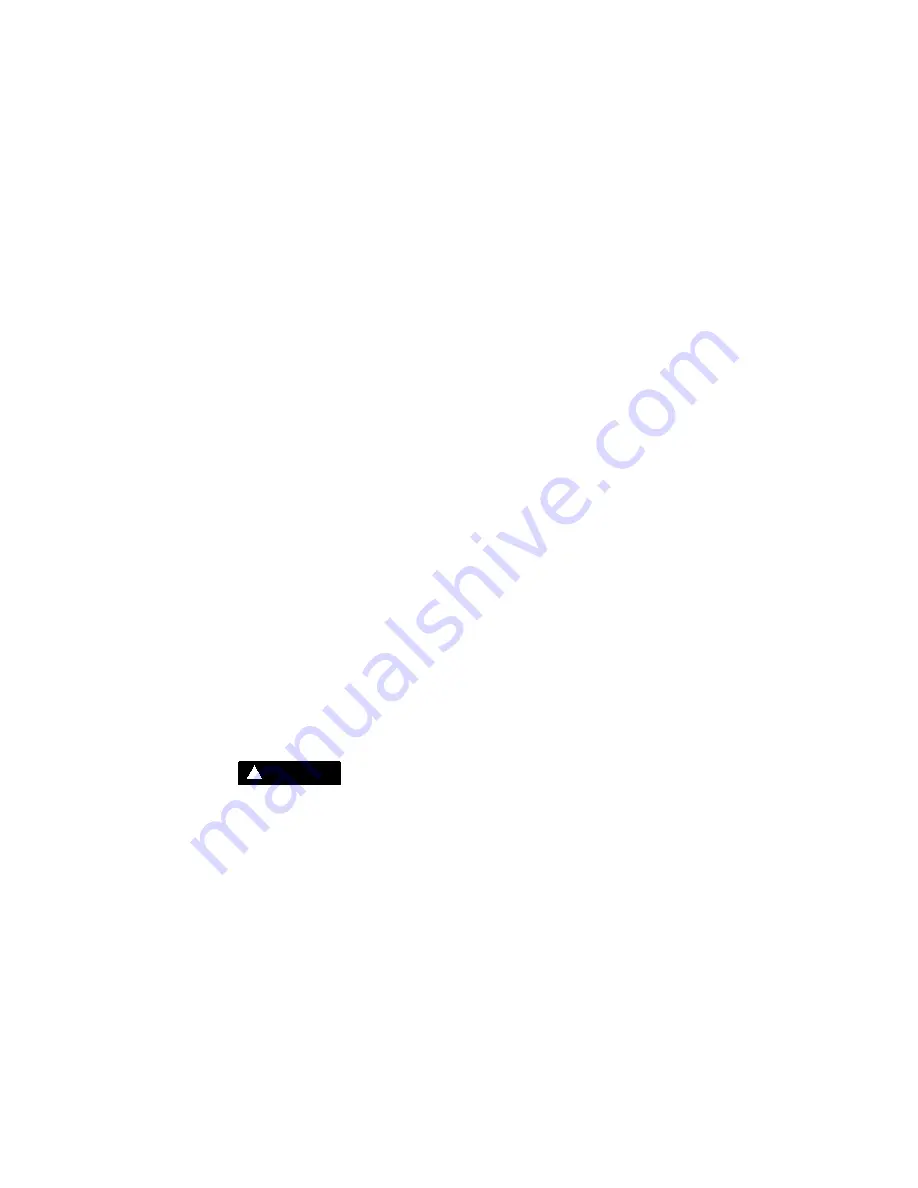
Section 4
COMPRESSOR SYSTEMS
11
4.1 INTRODUCTION
Your new Sullair flood--lubricated rotary screw air
compressor will provide you with improved reliability
and greatly reduced maintenance.
Compared with other types of compressors, the
Sullair rotary screw is unique in mechanical reliabil-
ity, with “no wear” and “no inspection” required of the
working parts within the compressor unit.
Read S ec t ion 7 ( M aint enanc e)
t o k eep y our c om -
pressor in top operating condition. Should any ques-
tions arise which cannot be answered in the follow-
ing text, call your nearest Sullair office or the Sullair
Corporation Service Department.
4.2 DESCRIPTION OF COMPONENTS
Ref er t o F igur es
4 -- 1A
and
4- 1B
. T he c om ponent s
and assemblies of the ES--11 Series air compressor
are clearly shown. The complete compressor con-
sists of an
integrated compressor system, inlet
system, discharge system, cooling and lubrica-
tion system, control system instrumentation
and optional
Supervisor II control system.
The compact design of the ES--11 Series air com-
pressor provides easy access to all serviceable
components.
4.3 INTEGRATED COMPRESSOR SYSTEM, FUNC-
TIONAL DESCRIPTION
Ref er t o
F igur e 4 -- 2
. T he int egr at ed c om pr es s or in-
cludes
compressor unit
,
cooling and lubrication
system,
and
drive motor
. The Sullair compressor
unit is a single--stage positive displacement lubri-
cated type compressor. This unit is equipped with
tapered roller bearings on the discharge and cylin-
drical roller bearings on the inlet end for high load
carrying capacity. This unit provides continuous
pulse--free air compression to meet your needs.
With a Sullair compressor there will be no mainte-
nance or internal inspection of the compressor.
WARNING
!
DO NOT remove caps, plugs and/or other compo-
nents when compressor is running or pressur-
ized.
Stop compressor and relieve all internal pressure
before doing so.
Fluid is injected into the compressor unit and mixes
directly with the air as the rotors turn, compressing
the air. The fluid flow has three main functions:
1. As coolant, it controls the rise of air temperature
normally associated with the heat of compres-
sion.
2. It seals the leakage paths between the rotors and
the stator and also between the rotors them-
selves.
3. It acts as a lubricating film between the rotors al-
lowing one rotor to directly drive the other, which
is an idler.
The air/fluid mixture discharges directly into the fluid
management system.
The fluid cooler bypass valve helps assure proper
cooling by directing the fluid to the fluid cooler when
discharge temperature reaches the thermostat tem-
perature setting.
During start--up in cool ambient conditions, the cool-
er pressure drop may cause the filter bypass valve
to open up, assuring adequate fluid supply to the
compressor.
All fluid entering the compressor unit passes
through the replaceable fluid filter element. This re-
placeable filter element contains a built--in bypass
valve. Under conditions of restricted flow through
the element, the bypass valve helps ensure ade-
quate compressor fluid flow, as well as helps pre-
vent element failure.
4.4 COMPRESSOR COOLING AND LUBRICATION
SYSTEM, FUNCTIONAL DESCRIPTION
Ref er t o F igur es
4 -- 1A
,
4 -- 1B
and
4 -- 2
. T he c ooling
and lubrication system consists of a
fan
,
radiator--
type cooler
,
main line filter
,
cooler bypass valve
,
inlet filter
and
interconnecting piping and tub-
ing
.
The fluid flows from the receiver/sump to the ther-
mal valve. The standard thermal valve has a nomi-
nal t em per at ur e of 185
_
F (85
_
C) , 195
_
F (91
_
C) f or
175 psig (12 bar) compressors. At low tempera-
tures, the fluid passes through the thermal valve, the
filter and directly to the compressor unit.
As the discharge temperature rises above 185
_
F
(85
_
C) for standard compressors, 195
_
F (91
_
C) for
175 psig (12 bar) compressors, due to the heat of
compression, the thermal valve begins to close and
a portion of the fluid then flows through the cooler;
from the cooler to the filter, and on to the compres-
sor unit.
For the water--cooled models, a shell and tube heat
exchanger and water--flow regulating valve are sub-
stituted for the radiator--type cooler and cooler by-
pass valve listed above.
4.5 AIR INLET SYSTEM, FUNCTIONAL DE-
SCRIPTION
The compressor inlet system consists of a dry--type
air filter and an air control valve. Reacting on a pres-
sure signal, the valve closes the intake for unloaded
operation. The valve also acts as a check valve
upon shutdown.
4.6 CONTROL SYSTEM, FUNCTIONAL DE-
SCRIPTION- STANDARD ELECTRO/MECHANI-
CAL
Ref er t o
F igur e 4 -- 3
. T he pur pos e of t he c om pr es s or
control system is to regulate the compressor air in-
take to match the amount of compressed air being
used. At approximately 10 psig (.7 bar) air line over
pressure, the control system will automatically blow
down the compressor and greatly reduce the unload
power consumption. The control system consists of
Summary of Contents for ES-11 SERIES
Page 6: ...NOTES...
Page 13: ...Section 2 INSTALLATION 7 Figure 2 1 Service Air Piping...
Page 14: ...8 NOTES...
Page 18: ...Section 4 COMPRESSOR SYSTEMS 12 Figure 4 1A Description of Components...
Page 19: ...Section 4 COMPRESSOR SYSTEMS 13 AIR COOLED WATER COOLED Figure 4 1B Description of Components...
Page 22: ...Section 4 COMPRESSOR SYSTEMS 16 Figure 4 3 Pneumatic Control System Standard Supervisor II...
Page 30: ...24 NOTES...
Page 34: ...28 NOTES...
Page 40: ...Section 7 MAINTENANCE 34 Figure 7 6 Cooler Cleaning COOLER SHROUD COMPRESSOR ENCLOSURE COOLER...
Page 42: ...36 NOTES...
Page 48: ...42 NOTES...
Page 50: ...Section 9 ILLUSTRATIONS AND PARTS LIST 44 9 3 FRAME MOTOR COMPRESSOR AND PARTS...
Page 52: ...Section 9 ILLUSTRATIONS AND PARTS LIST 46 9 4 COMPRESSOR AND PARTS 44...
Page 54: ...Section 9 ILLUSTRATIONS AND PARTS LIST 48 9 4 COMPRESSOR AND PARTS 44...
Page 56: ...Section 9 ILLUSTRATIONS AND PARTS LIST 50 9 5 MOTOR AND PARTS...
Page 60: ...Section 9 ILLUSTRATIONS AND PARTS LIST 54 9 7 COOLING SYSTEM AND PARTS AIR COOLED...
Page 62: ...Section 9 ILLUSTRATIONS AND PARTS LIST 56 9 7 COOLING SYSTEM AND PARTS AIR COOLED...
Page 64: ...Section 9 ILLUSTRATIONS AND PARTS LIST 58 9 8 COOLING SYSTEM AND PARTS WATER COOLED...
Page 66: ...Section 9 ILLUSTRATIONS AND PARTS LIST 60 9 8 COOLING SYSTEM AND PARTS WATER COOLED...
Page 68: ...Section 9 ILLUSTRATIONS AND PARTS LIST 62 9 8 COOLING SYSTEM AND PARTS WATER COOLED...
Page 70: ...Section 9 ILLUSTRATIONS AND PARTS LIST 64 9 9 CONTROL BOX AND PARTS STANDARD NOTE...
Page 72: ...Section 9 ILLUSTRATIONS AND PARTS LIST 66 9 9 CONTROL BOX AND PARTS STANDARD NOTE...
Page 74: ...Section 9 ILLUSTRATIONS AND PARTS LIST 68 9 9 CONTROL BOX AND PARTS STANDARD NOTE...
Page 76: ...Section 9 ILLUSTRATIONS AND PARTS LIST 70 9 9A CONTROL BOX AND PARTS SUPERVISOR II NOTE...
Page 78: ...Section 9 ILLUSTRATIONS AND PARTS LIST 72 9 9A CONTROL BOX AND PARTS SUPERVISOR II NOTE...
Page 80: ...Section 9 ILLUSTRATIONS AND PARTS LIST 74 9 9B CONTROL PANEL AND PARTS ELECTRO MECHANICAL...
Page 82: ...Section 9 ILLUSTRATIONS AND PARTS LIST 76 9 10 CANOPY ACOUSTICAL PANELS AND PARTS...
Page 84: ...Section 9 ILLUSTRATIONS AND PARTS LIST 78 9 10 CANOPY ACOUSTICAL PANELS PARTS...
Page 86: ...Section 9 ILLUSTRATIONS AND PARTS LIST 80 9 11 DECAL GROUP 1 2 3 4 5 6 02250077 472 2A...
Page 88: ...Section 9 ILLUSTRATIONS AND PARTS LIST 82 9 11 DECAL GROUP 8 9 10 11 12 13 7...
Page 91: ...Section 9 ILLUSTRATIONS AND PARTS LIST 85 9 13 WIRING DIAGRAM FULL VOLTAGE SUPERVISOR II...
Page 93: ...Section 9 ILLUSTRATIONS AND PARTS LIST 87 9 15 WIRING DIAGRAM WYE DELTA 50 60 HZ SUPERVISOR II...
Page 97: ...NOTES...