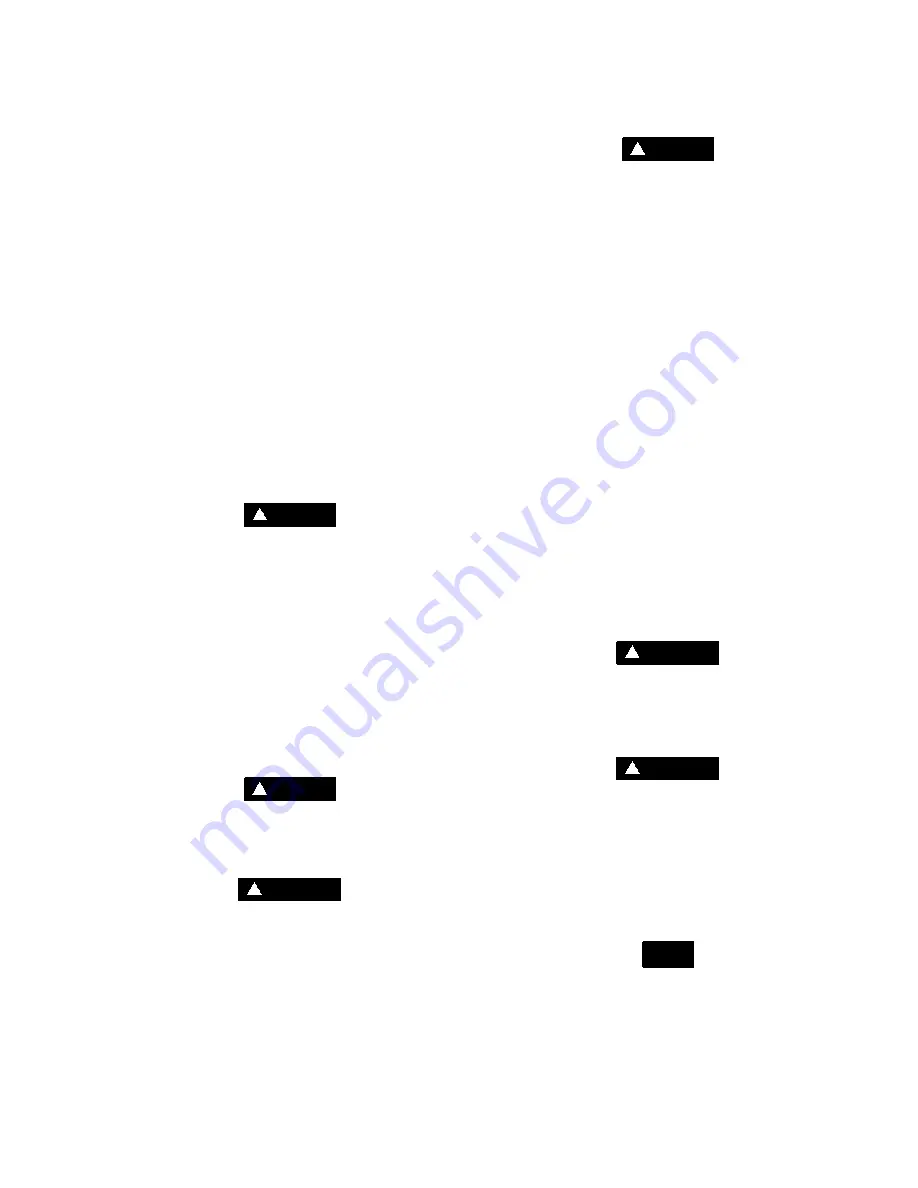
Section 7
MAINTENANCE
32
approximately 103 psig (7.1 bar) and 1.00 in. Hg
vacuum below the inlet.
4. Now close the service valve, line pressure will
start rising. When line pressure reaches 110
psig. (7.6 bar), the inlet valve will be closed to its
maximum position. The inlet vacuum at this point
will be around 25 in. Hg. The machine should un-
load at this point.
5. Open the service valve so the line pressure is 100
psig (6.9 bar). Machine is now set for operation.
Recheck the unload pressure by closing of the
service valve. Machine should unload via the
pressure switch at 110 psig (7.6 bar).
After the control pressures have been adjusted, the
“unloaded” sump pressure should be checked. It will
be necessary to shut the compressor down, remove
the pressure switch cover and disconnect one of the
two lead wires that are connected to the micro--
switch (contact block). After disconnecting the lead,
tape the exposed wire with electrician’s tape to
make sure that it does not come in contact with any
metallic surface.
DANGER
!
DO NOT touch the electrical contacts, terminal or
leads with any metallic object. Severe electrical
shock may occur.
With the lead taped, you may start the compressor
again. Allow the sump pressure to stabilize.
The sump pressure should read 30 to 35 psig (2.1 to
2.8 bar).
Once this is checked, shut the compressor down
once again and reconnect the taped lead and re-
place the pressure switch cover. At this time, start
the compressor and cycle the Control System sev-
eral times and re--check all pressure settings and
adjustments.
DANGER
!
DO NOT touch the pressure switch, electrical
contacts, terminal board or leads with any part of
the body or any uninsulated metallic object. Se-
vere electrical shock may occur.
WARNING
!
Before doing compressor maintenance, discon-
nect compressor from power source and lock out
power source. Isolate compressor from line pres-
sure by closing recommended discharge shut--
off valve and releasing all internal pressure from
compressor.
CONTROL SYSTEM ADJUSTMENT- SUPERVI-
SOR II
All components in the Control System are designed
and manufactured to close tolerances to help elimi-
nate any need for adjustments.
DANGER
!
DO NOT touch the electrical contacts, terminal or
leads with any part of the body or any uninsulated
metallic object. Severe electrical shock may oc-
cur.
PRESSURE VALVE ADJUSTMENT- SUPERVI-
SOR II
If pressure valve adjustment is required the adjust-
ment procedure below should be followed:
1. Start compressor.
2. Lower line pressure (P
2
) until machine goes on
load.
3. Loosen hex nut on the regulator valve to adjust
machine modulation. Adjust screw in or out until
on load/off load modulation of compressor takes
place.
4. Close service valve downstream from receiver
tank. The pressure will increase depending on
the regulator valve adjustment screw setting. Ad-
just screw until line pressure (P
2
) rises to the Su-
pervisor II preprogrammed off load setting. Tight-
en hex nut.
5. Open service valve and observe correct on load/
off load modulation.
INLET CONTROL VALVE
Ref er t o
F igur e 7 -- 5
. T he inlet c ont r ol v alv e nor m al
maintenance requires only the replacement of the
o--rings. Use repair kit no. 02250083--661 and fol-
low the procedure below for proper disassembly and
assembly procedures.
WARNING
!
Before doing compressor maintenance, discon-
nect compressor from power source and lock out
power source. Isolate compressor from line pres-
sure by closing recommended discharge shut--
off valve and releasing all internal pressure from
compressor.
WARNING
!
Assure that line pressure gauge on compressor
indicates “ZERO” pressure before any work is
done. Failure to comply can cause injury.
1. Remove access panels and air filter..
2. Identify and tag plastic lines connected to the inlet
adapter and disconnect.
3. Remove snap ring.
4. Remove inlet adapter and o--ring.
5. Remove inlet valve and spring.
6. Remove retaining ring.
NOTE
While removing the snap ring, push the spring re-
tainer down to overcome the force created by the
spring.
7. Remove retainer, piston and spring.
8. Inspect and clean all parts.
9. Oil and install new piston o--ring; reinstall piston
spring and retainer. Secure with retaining ring.
Summary of Contents for ES-11 SERIES
Page 6: ...NOTES...
Page 13: ...Section 2 INSTALLATION 7 Figure 2 1 Service Air Piping...
Page 14: ...8 NOTES...
Page 18: ...Section 4 COMPRESSOR SYSTEMS 12 Figure 4 1A Description of Components...
Page 19: ...Section 4 COMPRESSOR SYSTEMS 13 AIR COOLED WATER COOLED Figure 4 1B Description of Components...
Page 22: ...Section 4 COMPRESSOR SYSTEMS 16 Figure 4 3 Pneumatic Control System Standard Supervisor II...
Page 30: ...24 NOTES...
Page 34: ...28 NOTES...
Page 40: ...Section 7 MAINTENANCE 34 Figure 7 6 Cooler Cleaning COOLER SHROUD COMPRESSOR ENCLOSURE COOLER...
Page 42: ...36 NOTES...
Page 48: ...42 NOTES...
Page 50: ...Section 9 ILLUSTRATIONS AND PARTS LIST 44 9 3 FRAME MOTOR COMPRESSOR AND PARTS...
Page 52: ...Section 9 ILLUSTRATIONS AND PARTS LIST 46 9 4 COMPRESSOR AND PARTS 44...
Page 54: ...Section 9 ILLUSTRATIONS AND PARTS LIST 48 9 4 COMPRESSOR AND PARTS 44...
Page 56: ...Section 9 ILLUSTRATIONS AND PARTS LIST 50 9 5 MOTOR AND PARTS...
Page 60: ...Section 9 ILLUSTRATIONS AND PARTS LIST 54 9 7 COOLING SYSTEM AND PARTS AIR COOLED...
Page 62: ...Section 9 ILLUSTRATIONS AND PARTS LIST 56 9 7 COOLING SYSTEM AND PARTS AIR COOLED...
Page 64: ...Section 9 ILLUSTRATIONS AND PARTS LIST 58 9 8 COOLING SYSTEM AND PARTS WATER COOLED...
Page 66: ...Section 9 ILLUSTRATIONS AND PARTS LIST 60 9 8 COOLING SYSTEM AND PARTS WATER COOLED...
Page 68: ...Section 9 ILLUSTRATIONS AND PARTS LIST 62 9 8 COOLING SYSTEM AND PARTS WATER COOLED...
Page 70: ...Section 9 ILLUSTRATIONS AND PARTS LIST 64 9 9 CONTROL BOX AND PARTS STANDARD NOTE...
Page 72: ...Section 9 ILLUSTRATIONS AND PARTS LIST 66 9 9 CONTROL BOX AND PARTS STANDARD NOTE...
Page 74: ...Section 9 ILLUSTRATIONS AND PARTS LIST 68 9 9 CONTROL BOX AND PARTS STANDARD NOTE...
Page 76: ...Section 9 ILLUSTRATIONS AND PARTS LIST 70 9 9A CONTROL BOX AND PARTS SUPERVISOR II NOTE...
Page 78: ...Section 9 ILLUSTRATIONS AND PARTS LIST 72 9 9A CONTROL BOX AND PARTS SUPERVISOR II NOTE...
Page 80: ...Section 9 ILLUSTRATIONS AND PARTS LIST 74 9 9B CONTROL PANEL AND PARTS ELECTRO MECHANICAL...
Page 82: ...Section 9 ILLUSTRATIONS AND PARTS LIST 76 9 10 CANOPY ACOUSTICAL PANELS AND PARTS...
Page 84: ...Section 9 ILLUSTRATIONS AND PARTS LIST 78 9 10 CANOPY ACOUSTICAL PANELS PARTS...
Page 86: ...Section 9 ILLUSTRATIONS AND PARTS LIST 80 9 11 DECAL GROUP 1 2 3 4 5 6 02250077 472 2A...
Page 88: ...Section 9 ILLUSTRATIONS AND PARTS LIST 82 9 11 DECAL GROUP 8 9 10 11 12 13 7...
Page 91: ...Section 9 ILLUSTRATIONS AND PARTS LIST 85 9 13 WIRING DIAGRAM FULL VOLTAGE SUPERVISOR II...
Page 93: ...Section 9 ILLUSTRATIONS AND PARTS LIST 87 9 15 WIRING DIAGRAM WYE DELTA 50 60 HZ SUPERVISOR II...
Page 97: ...NOTES...