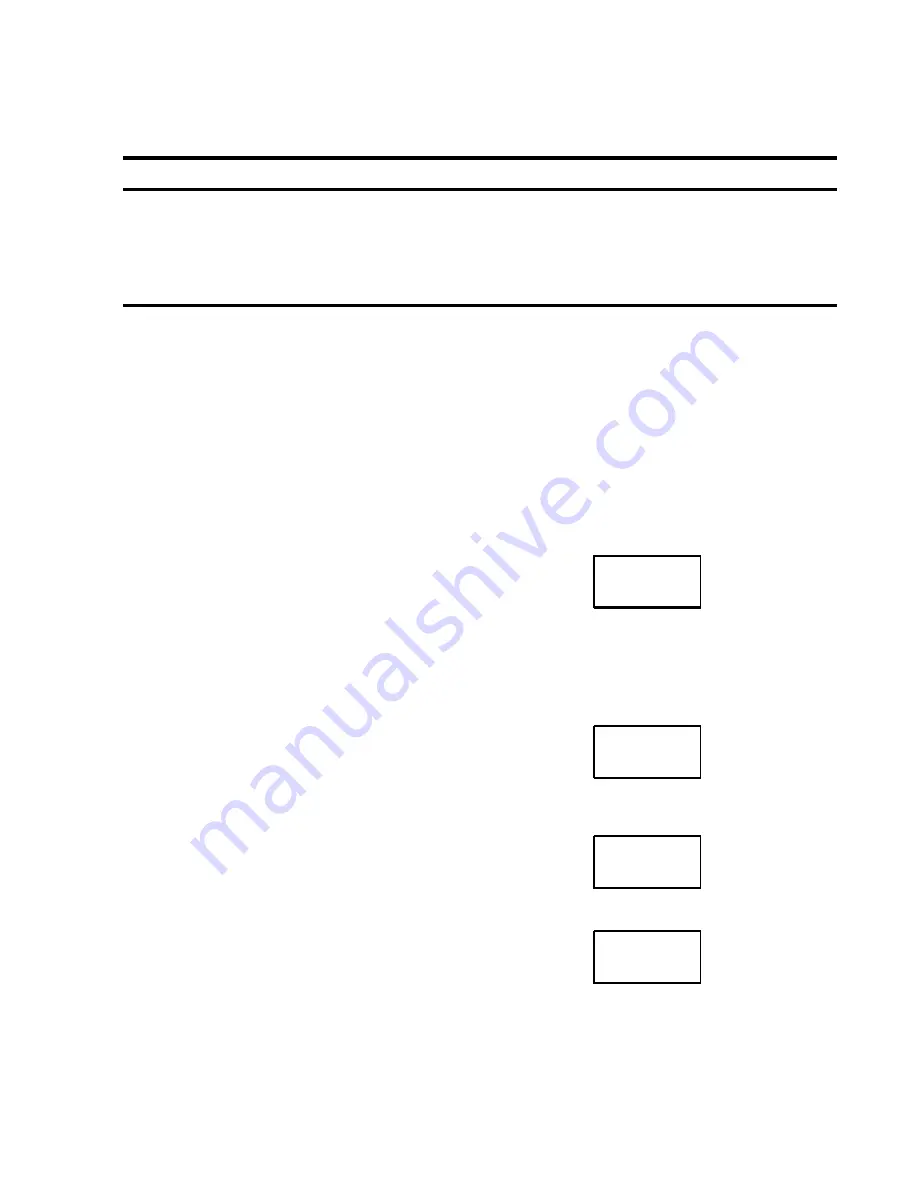
Section 5
COMPRESSOR OPERATION
19
5.2 PURPOSE OF CONTROLS -- STANDARD (CONTINUED)
CONTROL OR INDICATOR
PURPOSE
PRESSURE SWITCH
Senses service line pressure. When line pressure
reaches maximum setting the pressure switch signals
the solenoid valve to unload the compressor.
BLOWDOWN VALVE
Vents sump pressure to the compressor inlet during
unload conditions and shutdown.
5.3 INITIAL START--UP PROCEDURE
The following procedure should be used to make the
initial start--up of the compressor:
1. Read the preceding pages of this manual thor-
oughly.
2. Jog motor to check for correct rotation of motor.
3. Be sure that all preparations and checks de-
scribed in the Installation section have been
made.
4. Crack open the shut off valve to the service line.
5. Start the compressor by turning the START/RUN/
STOP selector switch to the
“I” (START)
posi-
tion momentarily and release..
6. Check for possible leaks in piping.
7. Slowly close the shut--off valve and check that the
setting on the pressure switch is set correctly. If
set correctly, the compressor will unload at the
desired unload pressure. If adjustments are nec-
essary, see Control System Adjustments in the
Maintenance Section of the manual.
8. Observe the operating temperature. If the operat-
ing temperature exceeds 200
_
F (93
_
C), the
cooling system or installation environment
should be checked.
9. Observe maintenance indicators.
10. Open shut--off valve to service line.
11. Re--inspect the compressor for temperature and
leaks the following day.
5.4 SUBSEQUENT START--UP PROCEDURE
On subsequent start--ups, check that the proper lev-
el is visible in the fluid sight glass and turn the
START/RUN/STOP selector switch to the ”I”
START position momentarily and release. When the
compressor is running, observe the instrument pan-
el and maintenance indicators.
5.5 SHUTDOWN PROCEDURE
To shut the compressor down, simply turn the selec-
tor switch to the “O” STOP position.
5.6 GENERAL INTRODUCTION- SUPERVISOR II
Reference Supervisor II Section 6. While Sullair has
built into this compressor a comprehensive array of
controls and indicators to assure you that it is oper-
ating properly, you will want to recognize and inter-
pret the reading which will call for service or indicate
the beginning of a malfunction. Before starting your
Sullair compressor, read this section thoroughly and
familiarize yourself with the controls and indicators --
their purpose, location and use.
5.7 SUPERVISOR II PARAMETER SETUP
Pressing the program key enters parameter display
and edit mode. To move to the next parameter press
the program key. To increment a parameter press
the up arrow key or logo key. The logo key will incre-
ment by 10. To decrement the value press the down
arrow key.
The parameters are displayed in the following order:
S
Unload pressure
-- The pressure where
the machine is unloaded. For example if
this parameter is set to 110 psi (7.6 bar) the
machine will unload when the line pressure
is above 110 psi (7.6 bar).
UNLOAD
100 PSI
S
Load differential
-- The pressure differen-
tial below the unload pressure where the
machine is loaded. For example, if the un-
load pressure is set to 110 psi (7.6 bar) and
the load differential is set to 10 psi (.7 bar),
the machine will load when the line pres-
sure goes below 100 psi (6.9 bar).
LOAD
10 PSI
S
P1 Max
-- Maximum sump pressure. An
alarm and shut down will occur when the
sump pressure rises above this pressure.
P1 MAX
135 PSI
S
Wye to delta transition timer
-- For full
voltage starters this parameter is set to 0.
WYE DELT
10 SEC
S
Restart time
-- Time to wait after power up
before starting machine. This parameter is
used to keep several machines from start-
ing at the same time after power up, or to
delay start until other equipment is started.
If disabled the machine will not automatical-
Summary of Contents for ES-11 SERIES
Page 6: ...NOTES...
Page 13: ...Section 2 INSTALLATION 7 Figure 2 1 Service Air Piping...
Page 14: ...8 NOTES...
Page 18: ...Section 4 COMPRESSOR SYSTEMS 12 Figure 4 1A Description of Components...
Page 19: ...Section 4 COMPRESSOR SYSTEMS 13 AIR COOLED WATER COOLED Figure 4 1B Description of Components...
Page 22: ...Section 4 COMPRESSOR SYSTEMS 16 Figure 4 3 Pneumatic Control System Standard Supervisor II...
Page 30: ...24 NOTES...
Page 34: ...28 NOTES...
Page 40: ...Section 7 MAINTENANCE 34 Figure 7 6 Cooler Cleaning COOLER SHROUD COMPRESSOR ENCLOSURE COOLER...
Page 42: ...36 NOTES...
Page 48: ...42 NOTES...
Page 50: ...Section 9 ILLUSTRATIONS AND PARTS LIST 44 9 3 FRAME MOTOR COMPRESSOR AND PARTS...
Page 52: ...Section 9 ILLUSTRATIONS AND PARTS LIST 46 9 4 COMPRESSOR AND PARTS 44...
Page 54: ...Section 9 ILLUSTRATIONS AND PARTS LIST 48 9 4 COMPRESSOR AND PARTS 44...
Page 56: ...Section 9 ILLUSTRATIONS AND PARTS LIST 50 9 5 MOTOR AND PARTS...
Page 60: ...Section 9 ILLUSTRATIONS AND PARTS LIST 54 9 7 COOLING SYSTEM AND PARTS AIR COOLED...
Page 62: ...Section 9 ILLUSTRATIONS AND PARTS LIST 56 9 7 COOLING SYSTEM AND PARTS AIR COOLED...
Page 64: ...Section 9 ILLUSTRATIONS AND PARTS LIST 58 9 8 COOLING SYSTEM AND PARTS WATER COOLED...
Page 66: ...Section 9 ILLUSTRATIONS AND PARTS LIST 60 9 8 COOLING SYSTEM AND PARTS WATER COOLED...
Page 68: ...Section 9 ILLUSTRATIONS AND PARTS LIST 62 9 8 COOLING SYSTEM AND PARTS WATER COOLED...
Page 70: ...Section 9 ILLUSTRATIONS AND PARTS LIST 64 9 9 CONTROL BOX AND PARTS STANDARD NOTE...
Page 72: ...Section 9 ILLUSTRATIONS AND PARTS LIST 66 9 9 CONTROL BOX AND PARTS STANDARD NOTE...
Page 74: ...Section 9 ILLUSTRATIONS AND PARTS LIST 68 9 9 CONTROL BOX AND PARTS STANDARD NOTE...
Page 76: ...Section 9 ILLUSTRATIONS AND PARTS LIST 70 9 9A CONTROL BOX AND PARTS SUPERVISOR II NOTE...
Page 78: ...Section 9 ILLUSTRATIONS AND PARTS LIST 72 9 9A CONTROL BOX AND PARTS SUPERVISOR II NOTE...
Page 80: ...Section 9 ILLUSTRATIONS AND PARTS LIST 74 9 9B CONTROL PANEL AND PARTS ELECTRO MECHANICAL...
Page 82: ...Section 9 ILLUSTRATIONS AND PARTS LIST 76 9 10 CANOPY ACOUSTICAL PANELS AND PARTS...
Page 84: ...Section 9 ILLUSTRATIONS AND PARTS LIST 78 9 10 CANOPY ACOUSTICAL PANELS PARTS...
Page 86: ...Section 9 ILLUSTRATIONS AND PARTS LIST 80 9 11 DECAL GROUP 1 2 3 4 5 6 02250077 472 2A...
Page 88: ...Section 9 ILLUSTRATIONS AND PARTS LIST 82 9 11 DECAL GROUP 8 9 10 11 12 13 7...
Page 91: ...Section 9 ILLUSTRATIONS AND PARTS LIST 85 9 13 WIRING DIAGRAM FULL VOLTAGE SUPERVISOR II...
Page 93: ...Section 9 ILLUSTRATIONS AND PARTS LIST 87 9 15 WIRING DIAGRAM WYE DELTA 50 60 HZ SUPERVISOR II...
Page 97: ...NOTES...