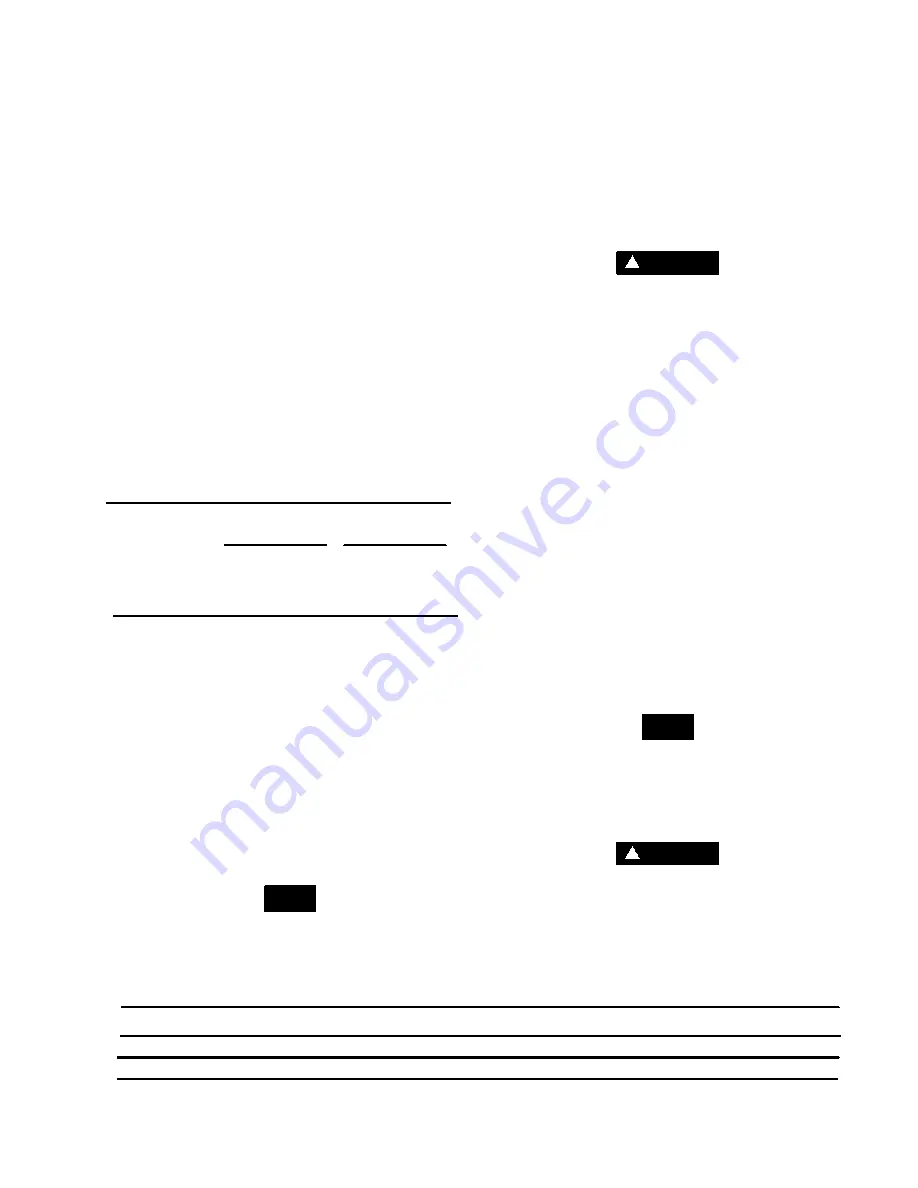
Section 2
INSTALLATION
5
2.1 LOCATION OF COMPRESSOR
The ES--11 Series compressor package may be
placed on any level surface capable of supporting its
weight and rigid enough to maintain a level com-
pressor frame. The compressor frame must be lev-
eled and secured with foundation bolts, and full uni-
form contact must be maintained between the frame
and foundation. No piping loads shall be transmitted
to the compressor at the external connections.
2.2 VENTILATION AND COOLING
Select a location to permit sufficient unobstructed
air flow in and out of the compressor to keep the op-
erating temperature stable. The minimum distance
that the machine should be from surrounding walls
and ceiling is what is needed for service and three
(3) feet (914mm) or more from the compressor fluid
cooler.
For water--cooled compressors, it is necessary to
check the cooling water supply. The proper water
f low s hould be as s hown in
Table 1
in t his s ec t ion.
40 hp (30kW)
50 hp (37kW)
GPM (LPM) @
70
_
F(21
_
C)
GPM (LPM) @
80
_
F(27
_
C)
5.3
(20)
7
(26)
9.3
(35)
TABLE 1 -- WATER FLOW REQUIREMENTS
5.3
(20)
Table 2
indic at es t he v ent ilat ion r equir em ent s nec -
essary to keep the compressor running at a normal
operating temperature. The fan air requirement is
the volume of air which must flow through the com-
pressor for proper ventilation. The specified heat
rejection requirement is the amount of heat that is
radiated by the compressor. This heat must be re-
moved to assure a normal operating temperature. It
is possible to use this heat for space heating, provid-
ing no additional pressure drop is created across the
fan. Consult a Sullair office for assistance in utilizing
this heat.
DO NOT
install a water--cooled or an air--cooled/af-
tercooled compressor where it will be exposed to
temperature less than 32
_
F (0
_
C)
NOTE
Be certain the watercooler drain plugs are in place
prior to start--up.
2.3 SERVICE AIR PIPING
Service air piping should be installed as shown in
F igur e 2 -- 1
. A s hut -- off v alv e s hould be ins t alled t o
isolate the compressor from the service line. Also
notice that the service line should be equipped with
water legs and condensate drains throughout the
system.
WARNING
!
“The Plastic Pipe Institute recommends against the
use of thermoplastic pipe to transport compressed
air or other compressed gases in exposed above
ground locations, e.g. in exposed plant piping.” (I)
Sullube 32 should not be used with PVC piping sys-
tems. It may affect the bond at cemented joints. Cer-
tain other plastic materials may also be affected.
(I) Plastic Pipe Institute, Recommendation B,
Adopted January 19, 1972.
2.4 FLUID LEVEL CHECK
A fluid sight glass on the sump housing serves as a
level indicator. During operation, the level should
not exceed 1/4 to 1/2 of the sight glass. With the
compressor shut down the level will rise to the bot-
tom of the fluid fill plug located above the sight glass.
2.5
ELECTRICAL PREPARATION- STANDARD
ELECTRO/MECHANICAL
Interior electrical wiring is performed at the factory.
Required customer wiring is minimal, but should be
done by a qualified electrician in compliance with
OSHA, National Electrical Code, and/or any other
applicable State, Federal and local electrical codes
concerning isolation switches, fused disconnects,
etc. Sullair provides a wiring diagram for use by the
installer.
NOTE
Customer must provide electrical supply power
disconnect within sight of machine.
A few electrical checks should be made to help as-
sure that the first start--up will be trouble--free.
WARNING
!
Lethal shock hazard inside. Disconnect all power
at source before opening or servicing.
1. Check incoming voltage. Be sure that compres-
sor is wired for the correct incoming voltage.
Motor hp (kW)
Heat Rejection BTU/hr (kcal/hr)
50hp (37kW)
40hp (30kW)
50hp (37kW)
40hp (30kW)
Water--cooled
Compressor Cooling Type
Air--cooled with Aftercool
120,000 (30,240)149,000 (37,550)
11202 (2822) 14000 (3530)
TABLE 2- VENTILATION REQUIREMENTS
Summary of Contents for ES-11 SERIES
Page 6: ...NOTES...
Page 13: ...Section 2 INSTALLATION 7 Figure 2 1 Service Air Piping...
Page 14: ...8 NOTES...
Page 18: ...Section 4 COMPRESSOR SYSTEMS 12 Figure 4 1A Description of Components...
Page 19: ...Section 4 COMPRESSOR SYSTEMS 13 AIR COOLED WATER COOLED Figure 4 1B Description of Components...
Page 22: ...Section 4 COMPRESSOR SYSTEMS 16 Figure 4 3 Pneumatic Control System Standard Supervisor II...
Page 30: ...24 NOTES...
Page 34: ...28 NOTES...
Page 40: ...Section 7 MAINTENANCE 34 Figure 7 6 Cooler Cleaning COOLER SHROUD COMPRESSOR ENCLOSURE COOLER...
Page 42: ...36 NOTES...
Page 48: ...42 NOTES...
Page 50: ...Section 9 ILLUSTRATIONS AND PARTS LIST 44 9 3 FRAME MOTOR COMPRESSOR AND PARTS...
Page 52: ...Section 9 ILLUSTRATIONS AND PARTS LIST 46 9 4 COMPRESSOR AND PARTS 44...
Page 54: ...Section 9 ILLUSTRATIONS AND PARTS LIST 48 9 4 COMPRESSOR AND PARTS 44...
Page 56: ...Section 9 ILLUSTRATIONS AND PARTS LIST 50 9 5 MOTOR AND PARTS...
Page 60: ...Section 9 ILLUSTRATIONS AND PARTS LIST 54 9 7 COOLING SYSTEM AND PARTS AIR COOLED...
Page 62: ...Section 9 ILLUSTRATIONS AND PARTS LIST 56 9 7 COOLING SYSTEM AND PARTS AIR COOLED...
Page 64: ...Section 9 ILLUSTRATIONS AND PARTS LIST 58 9 8 COOLING SYSTEM AND PARTS WATER COOLED...
Page 66: ...Section 9 ILLUSTRATIONS AND PARTS LIST 60 9 8 COOLING SYSTEM AND PARTS WATER COOLED...
Page 68: ...Section 9 ILLUSTRATIONS AND PARTS LIST 62 9 8 COOLING SYSTEM AND PARTS WATER COOLED...
Page 70: ...Section 9 ILLUSTRATIONS AND PARTS LIST 64 9 9 CONTROL BOX AND PARTS STANDARD NOTE...
Page 72: ...Section 9 ILLUSTRATIONS AND PARTS LIST 66 9 9 CONTROL BOX AND PARTS STANDARD NOTE...
Page 74: ...Section 9 ILLUSTRATIONS AND PARTS LIST 68 9 9 CONTROL BOX AND PARTS STANDARD NOTE...
Page 76: ...Section 9 ILLUSTRATIONS AND PARTS LIST 70 9 9A CONTROL BOX AND PARTS SUPERVISOR II NOTE...
Page 78: ...Section 9 ILLUSTRATIONS AND PARTS LIST 72 9 9A CONTROL BOX AND PARTS SUPERVISOR II NOTE...
Page 80: ...Section 9 ILLUSTRATIONS AND PARTS LIST 74 9 9B CONTROL PANEL AND PARTS ELECTRO MECHANICAL...
Page 82: ...Section 9 ILLUSTRATIONS AND PARTS LIST 76 9 10 CANOPY ACOUSTICAL PANELS AND PARTS...
Page 84: ...Section 9 ILLUSTRATIONS AND PARTS LIST 78 9 10 CANOPY ACOUSTICAL PANELS PARTS...
Page 86: ...Section 9 ILLUSTRATIONS AND PARTS LIST 80 9 11 DECAL GROUP 1 2 3 4 5 6 02250077 472 2A...
Page 88: ...Section 9 ILLUSTRATIONS AND PARTS LIST 82 9 11 DECAL GROUP 8 9 10 11 12 13 7...
Page 91: ...Section 9 ILLUSTRATIONS AND PARTS LIST 85 9 13 WIRING DIAGRAM FULL VOLTAGE SUPERVISOR II...
Page 93: ...Section 9 ILLUSTRATIONS AND PARTS LIST 87 9 15 WIRING DIAGRAM WYE DELTA 50 60 HZ SUPERVISOR II...
Page 97: ...NOTES...