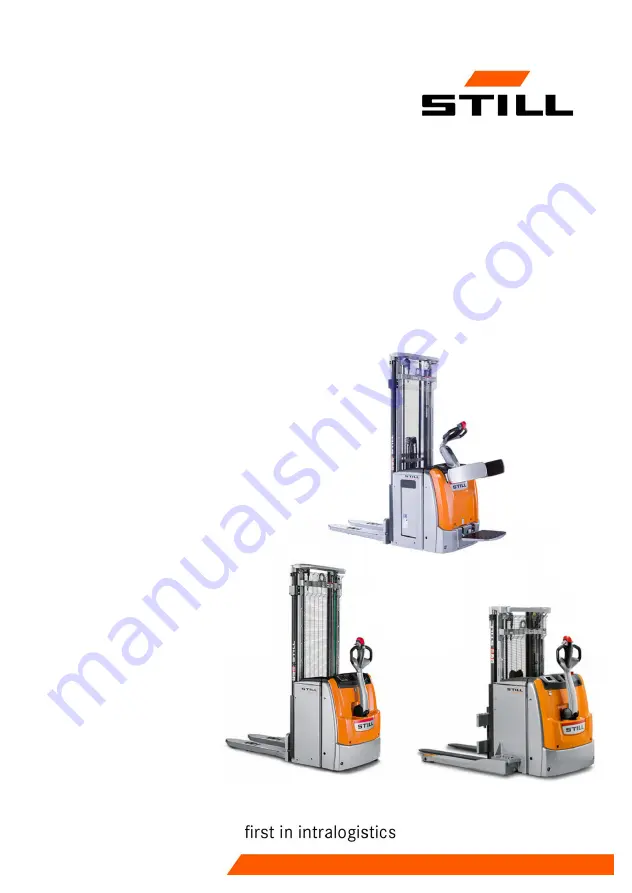
Pallet stacker
EXV 14 / 16 / 20
EXV 14i / 16i / 20i
EXV-SF 14 / 16 / 20
EXV-SF 14i / 16i / 20i
EXP 14 / 16 / 20
EXV 14D / 16D / 20D
EXV-SF 14D / 16D / 20D
Original instructions
0301 0303 0305 0323 0324 0325
0326 0327 0328 0329 0330 0331
0332 0333 0334 0335 0336 0337
0338 0339 0340
45758043484 EN - 11/2021 - 08
Summary of Contents for 0301
Page 2: ......
Page 4: ......
Page 10: ......
Page 11: ...1 Introduction ...
Page 23: ...2 Safety ...
Page 36: ...Safety 2 Safety devices 26 45758043484 EN 11 2021 08 ...
Page 37: ...3 Overview ...
Page 91: ...4 Use ...
Page 131: ...5 Maintenance ...
Page 148: ...Maintenance 5 Decommissioning 138 45758043484 EN 11 2021 08 ...
Page 149: ...6 Technical data ...
Page 166: ...EXP overall dimensions Technical data 6 EXP overall dimensions 156 45758043484 EN 11 2021 08 ...
Page 191: ......