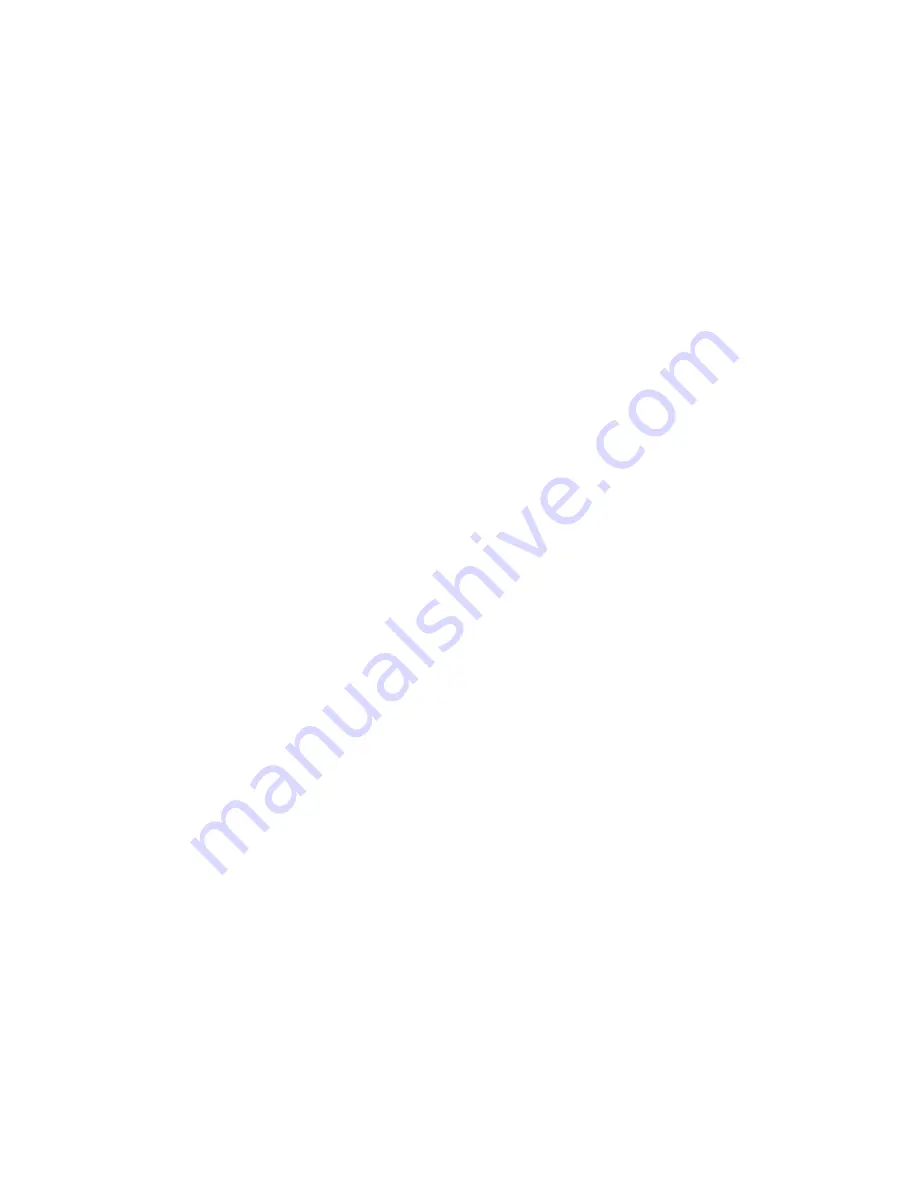
Issue 1
20
Daily
Alternator and Fan Belts - Inspect/Adjust/
Replace Cooling System Coolant Level - Check
Driven Equipment - Check
Engine Air Cleaner Service Indicator - Inspect
Engine Oil Level - Check
Fuel System Primary Filter/Water Separator -
Drain
Walk-Around Inspection
Every 50 Service Hours or Weekly
Fuel Tank Water and Sediment - Drain
Every 500 Service Hours or 1 Year
Battery Electrolyte Level - Check
Engine Air Cleaner Element (Dual Element) -
Clean/Replace
Engine Air Cleaner Element (Single Element) -
Inspect/Replace
Engine Ground - Inspect/Clean
Engine Oil and Filter - Change
Fuel System Primary Filter (Water Separator) drain
Element - Replace
Fuel System Secondary Filter - Replace
Hoses and Clamps - Inspect/Replace
Every 1000 Service Hours
Engine Valve Lash - Inspect/Adjust
Every 2000 Service Hours
Aftercooler Core - Inspect
Alternator - Inspect
Engine Mounts - Inspect
Starting Motor - Inspect
Turbocharger - Inspect
Water Pump - Inspect
Every 2 Years
Cooling System Coolant - Change
Every 3000 Service Hours
Fuel Injector - Test/Change
Every 3000 Service Hours or 2 Years
Cooling System Coolant (Commercial Heavy-Duty) -
Change
Every 4000 Service Hours
Aftercooler Core - Clean/Test
Every 6000 Service Hours or 3 Years
Cooling System Coolant Extender (ELC) - Add
Every 12 000 Service Hours or 6 Years
Cooling System Coolant (ELC) - Change
11.2 Light Load Operation
If an engine is operated on load less than 25-30% of its rated output, certain symptoms will be observed
which may be cause for concern. The engine is designed to run up to a maximum power and so the size of
the piston, the wall loading of the piston rings, etc are designed to cope with this.
When an engine is run at light load then the energy put into the cylinder is low and consequently the cylinder
pressure is lower and so is the temperature. The result is the piston is not such a good fit in the bore, with
increased clearance, allowing more oil to pass the piston and be burnt, which is indicated by high oil
consumption.
With lower pressures the sealing capacity of the rings is lower, also it is not ideal for bedding in the rings and
can cause bore glazing, which ruins all control.
On turbocharged engines oil will start to appear from the manifolds from the bearing arrangement in the
turbocharger.
Turbochargers are fitted to an engine to increase power by supplying more air to the cylinders. When running
a turbocharger, air is sucked in, which can have vacuum levels up to 500kPa, with pressure ratios of 3 : 1.
The compressor seals are designed to work most efficiently when the turbocharger compressor is operating
at its’ most efficient point. If the engine is running at low powers then the turbocharger is running at low speed
(no energy from the exhaust because the fuel inlet to the engine is low) and the inlet vacuum is low resulting
in poor turbocharger seal loading and pull over of oil from the bearing assembly. This oil is mixed with the air
and pumped into the manifolds where some separates from the air when it collides with the inside of the
manifold. If the joints are not air tight the oil will leak out.
Black smoke will be produced from the exhaust outlets, due to poor combustion at light load, as excess fuel is
pumped through into the exhaust system, resulting in soot being expelled into the exhaust system.
A further result is that abnormal carbon build-up on the valves, piston crowns and exhaust ports. Thus the
normal service interval between top overhauls may be reduced. Fuel dilution of the lubricating oil will also
occur.
It is therefore recommended that the following precautions are observed :-