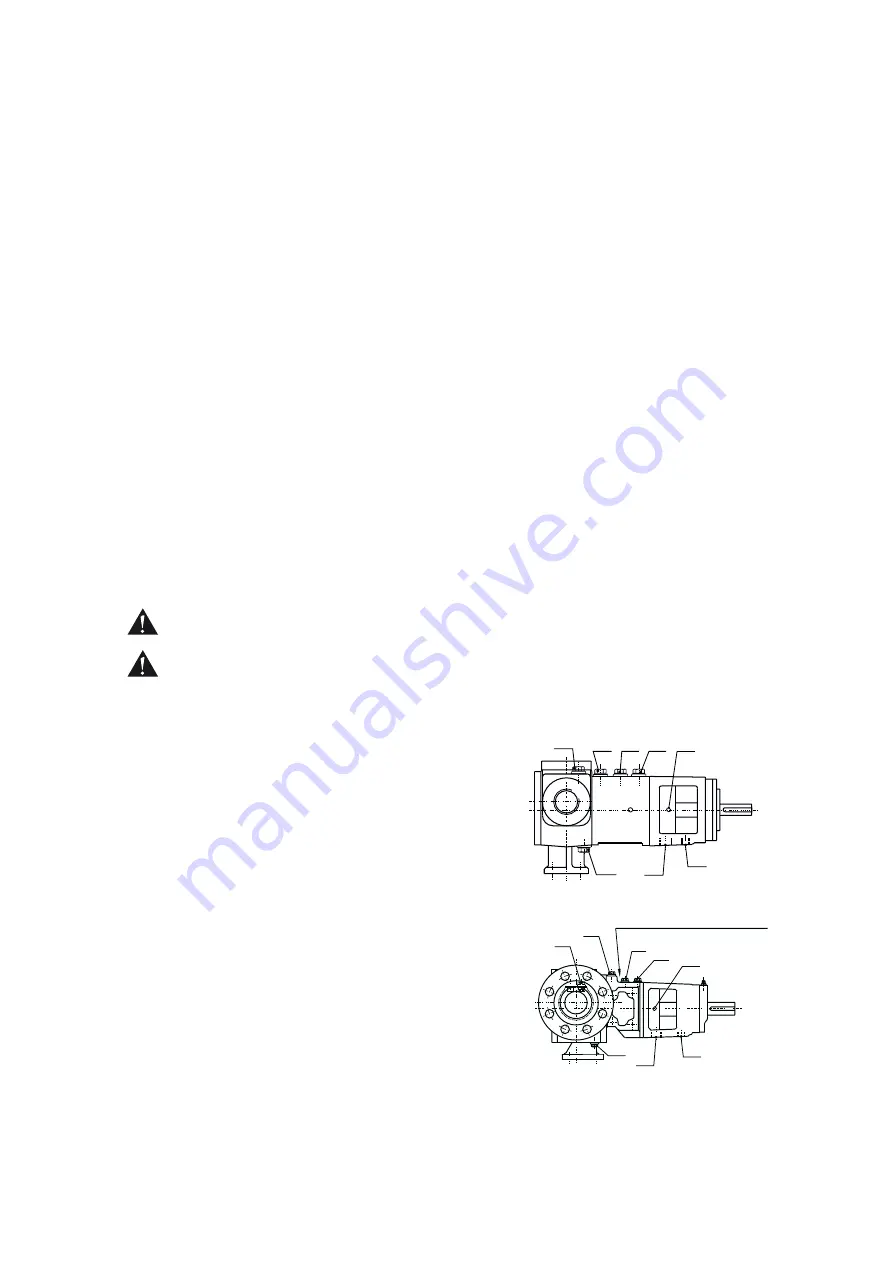
57
Be
Bk Bc Bd
Bj
1 ; 2
Bi
1 ; 2
Ba
Bk
de
Be
Bk
Bc Bd Bj
1 ; 2
Ba
de
Bb Bm
(TG H58-80 / TG H360-150)
A.0500.351 – IM-TGH/07.02 EN (10/2015)
3.21.2.6 External cleaning
• Keep the surface of the pump as clean as possible. This simplifies inspection, the attached
markings remain visible and grease nipples are not forgotten.
• Make sure cleaning products do not enter the ball bearing space. Cover all parts that must not
come into contact with fluids. In case of sealed bearings, cleaning products must not attack
rubber gaskets. Never spray the hot parts of a pump with water, as certain components may
crack due to the sudden cooling and the fluid being pumped may spray into the environment.
3.21.2.7 Electrical installation
• Maintenance operations on the electric installation may be performed only by trained and
qualified personnel and after disconnecting the electric power supply. Carefully follow the
national safety regulations.
Respect the above-mentioned regulations if performing work while the power supply is still
connected.
• Check if electrical devices to be cleaned have a sufficient degree of protection (e.g. IP54 means
protection against dust and splashing water but not against water jets). See EN 60529. Choose
an appropriate method for cleaning the electrical devices.
• Replace defective fuses only with original fuses of the prescribed capacity.
• After each maintenance session check the components of the electrical installation for visible
damage and repair them if necessary.
3.21.2.8 Draining of fluid
• Close off the pressure and suction lines as close as possible to the pump.
• If the fluid being pumped does not solidify, let the pump cool down to the ambient
temperature before drainage.
• For fluids that solidify or become very viscous at ambient temperature, it is best to empty the
pump immediately after shutting down by separating it from the piping. Always wear safety
goggles and gloves.
• Protect yourself with a protective cap. The fluid may spray out of the pump.
• Open the venting plugs Be, Bb, Bc and Bd.
• If no drain line is provided,
take precautions so that the liquid is
not contaminating the environment.
• Open the drain plug Ba at the bottom
of the pump housing.
• Let drain the liquid by gravity.
• Purge pump spaces with flush media or
cleaning liquid by connecting a purge
system to the following inlet openings:
- Ba, Be: the displacement part
- Ba, Bb: space behind rotor
- Ba, Bd: space behind bearing bush and first
mechanical seal in case of GS, GG and GC
shaft sealing versions
- Ba, Bc: space behind bearing bush and before the
mechanical seal box in case of GD shaft
sealing version
- Bc, Bd: packing area and lantern ring in case of PQ
shaft sealing version
• Re-assemble the plugs and close the valves, if any.
Summary of Contents for TG H15-50
Page 103: ...103 A 0500 351 IM TGH 07 00 EN 10 2015...
Page 105: ...105 A 0500 351 IM TGH 07 00 EN 10 2015...
Page 106: ...106 A 0500 351 IM TGH 07 00 EN 10 2015...
Page 107: ...107 A 0500 351 IM TGH 07 00 EN 10 2015...
Page 108: ...108 A 0500 351 IM TGH 07 00 EN 10 2015...
Page 109: ......