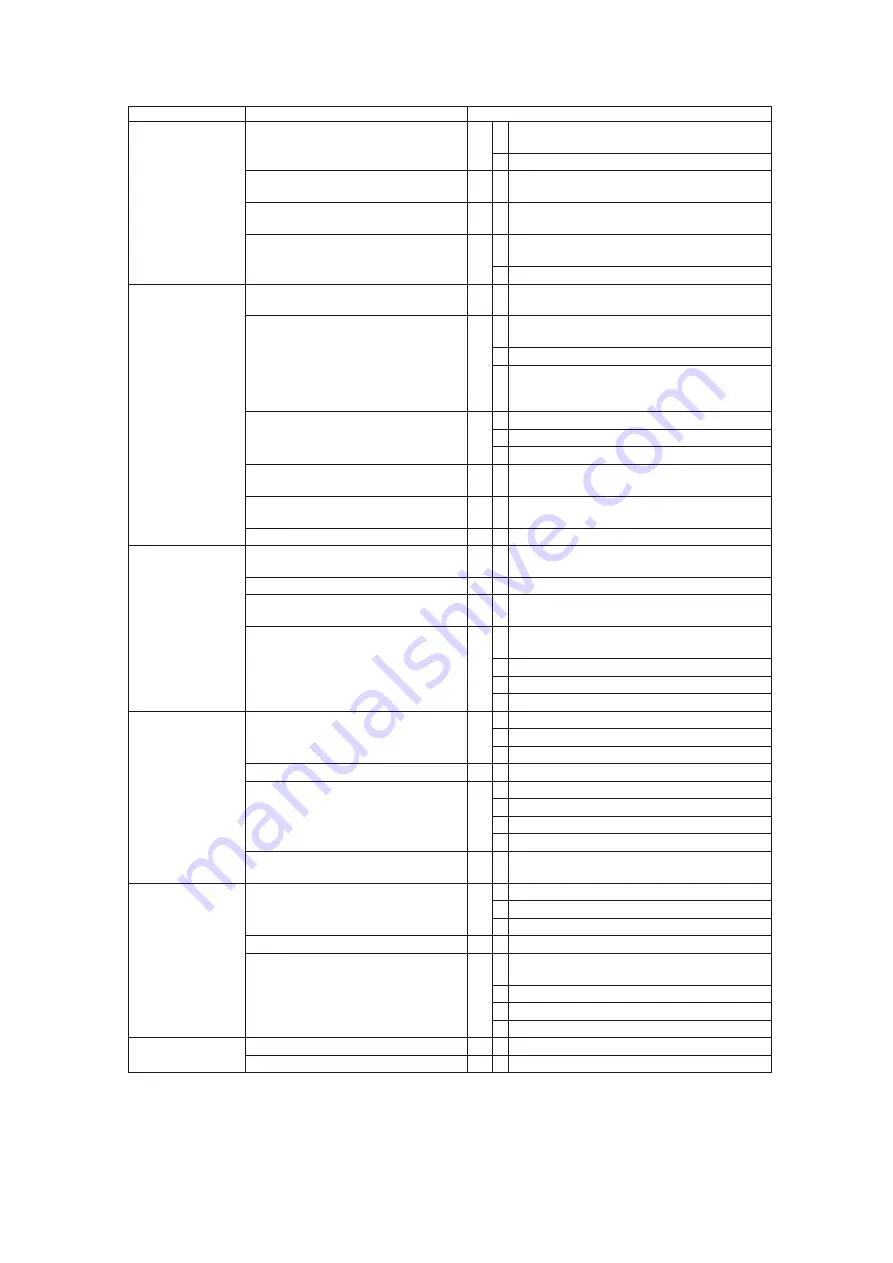
54
A.0500.351 – IM-TGH/07.02 EN (10/2015)
Symptom
Cause
Remedy
Not enough capacity Viscosity too low
17 • Increase pump speed.
Attention!
Do not exceed
maximum speed and check NPSHr.
• If necessary, install a larger pump.
•
• If pump is heated by means of heating jackets or
electrical heating, reduce the heating input.
Axial clearance
18 • Check axial clearance and correct.
See section 3.21 Maintenance instructions.
Gases come free
19 • Increase pump speed.
Attention!
Do not exceed
maximum speed and check NPSHr.
• Install a larger pump
Pump too noisy
Pump speed too high
20 • Reduce pump speed.
If necessary, install a larger pump.
Cavitation
21 • Reduce difference between pump and suction
tank level.
• Increase suction pipe diameter.
• Reduce length and simplify suction pipe (use as
few elbows and other fittings as possible).
Also see section 3.18 Installation.
Back pressure too high
22 • Increase pipe diameter.
• Reduce working pressure.
• Check accessories (filter, heat exchanger, etc.).
Coupling misalignment
23 • Check and correct alignment.
Also see section 3.18 Installation.
Vibration of base plate or pipings
24 • Make base plate heavier and/or fix base plate/
pipe work better.
Ball bearings damaged or worn
25 • Replace ball bearings.
Pump consumes
too much power or
becomes hot
Pump speed too high
26 • Reduce pump speed.
If necessary, install a larger pump.
Gland packing too tight
27 • Check or replace gland packing.
Coupling misalignment
28 • Check and correct alignment.
Also see section 3.18 Installation.
Viscosity too high
29 • Increase axial clearance.
See section 3.21 Maintenance instructions.
• Heat pump.
• Reduce pump speed.
• Increase discharge pipe diameter.
Rapid wear
Back pressure too high
30 • Increase pipe diameter.
• Reduce working pressure.
• Check accessories (filter, heat exchanger, etc.)
Solid matter in liquid
31 • Filter liquid.
Pump runs dry
32 • Correct liquid supply.
• Provide level switch or dry running protection.
• Heat up liquid.
• Stop or reduce air sucking.
Corrosion
33 • Change pump materials or application
parameters.
Motor overloading
Back pressure too high
34 • Increase pipe diameter.
• Reduce working pressure.
• Check accessories (filter, heat exchanger, etc.).
Gland packing too tight
35 • Check and replace gland packing.
Viscosity too high
36 • Increase axial clearance.
See section 3.21 Maintenance instructions.
• Heat pump.
• Reduce pump speed.
• Increase discharge pipe diameter.
Pump leak
Gland packing leaks excessively
37 • Check or replace gland packing.
Mechanical seal leaks
38 • Replace mechanical seal.
Summary of Contents for TG H15-50
Page 103: ...103 A 0500 351 IM TGH 07 00 EN 10 2015...
Page 105: ...105 A 0500 351 IM TGH 07 00 EN 10 2015...
Page 106: ...106 A 0500 351 IM TGH 07 00 EN 10 2015...
Page 107: ...107 A 0500 351 IM TGH 07 00 EN 10 2015...
Page 108: ...108 A 0500 351 IM TGH 07 00 EN 10 2015...
Page 109: ......