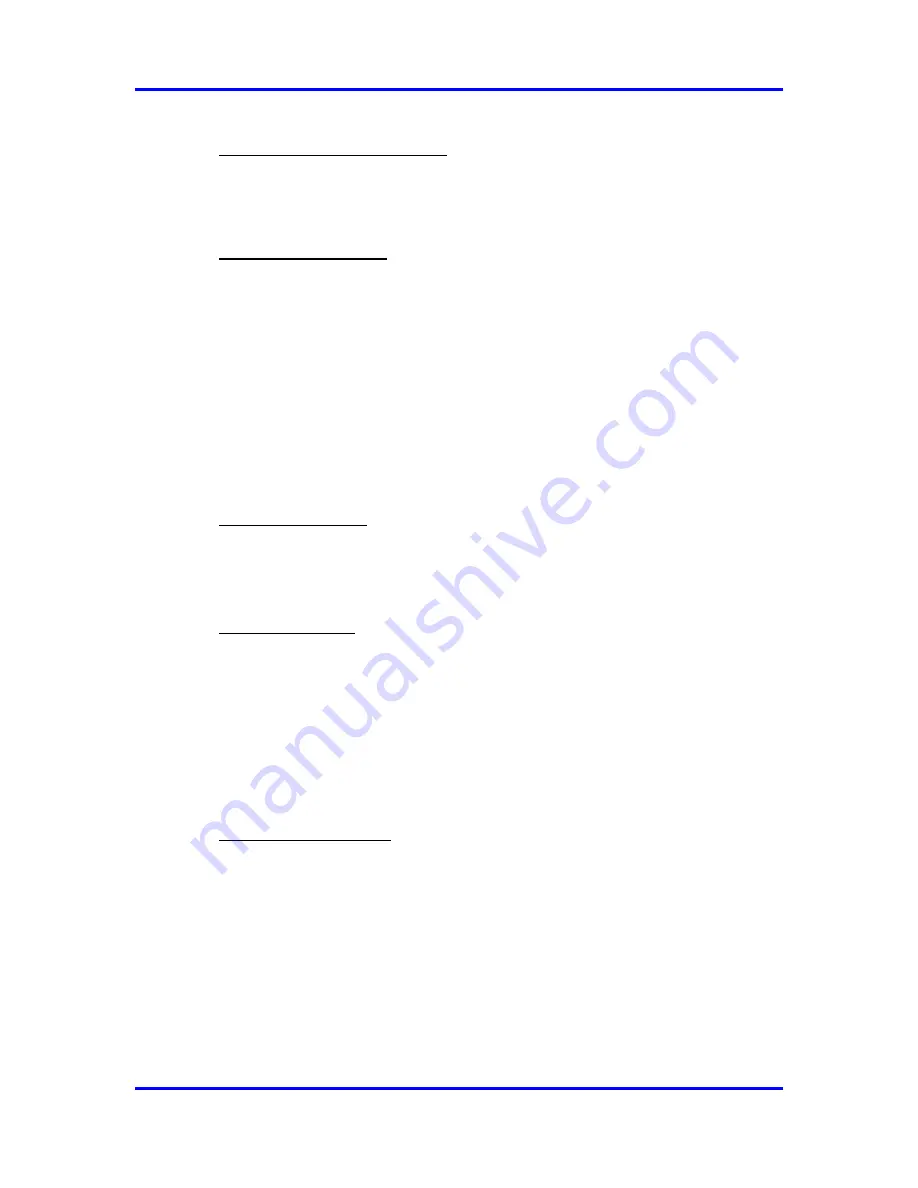
SERVOPRO CHROMA Gas Analyser
63
04400001A / Revision 7
10) Reload manufacturer settings
To return settings to the analyser factory configuration, click on this button.
Before using this function, please call Servomex for more information.
11) Range Configuration:
This is used to configure the relays on the I/O Board for the Peak Ranges. Change
the value of the combo box for the corresponding peak to change its state when
range 2 is active.
Use the
Lock Range
button to Lock or Unlock the analyser ranges. Press the
Lock Range
button to lock the range until the same button is pressed again (the
name label on the button will change).
The Lock Range function will be ignored
if the analyser is in auto-ranging mode.
Locking the ranges will disable the range
button in the
RUN-REAL TIME CHROMATOGRAM
menu
so that the
ranges cannot be changed even if manual ranging is ON.
12) Print configuration
This button is used to print the system configuration. For analysers with multiple
configurations, this function will only print the current system configuration
13) Change password
This button is used to set a new password for the SERVOPRO Chroma. This
password is used to quit the software or to access the
CONFIGURATION-
ADVANCED MENU
.
The default the general password for the analyser is its serial number. Click on
this button to change the password. A dialog window will request the current
password and will require the new password to be entered twice.
14) Change Configuration
If the analyser is supplied with multiple configurations to operate in different
background gases, the active configuration can be changed by clicking the
“
Change configuration
” button.
Changing the active configuration will upload
all the parameters according to the new selected configuration.