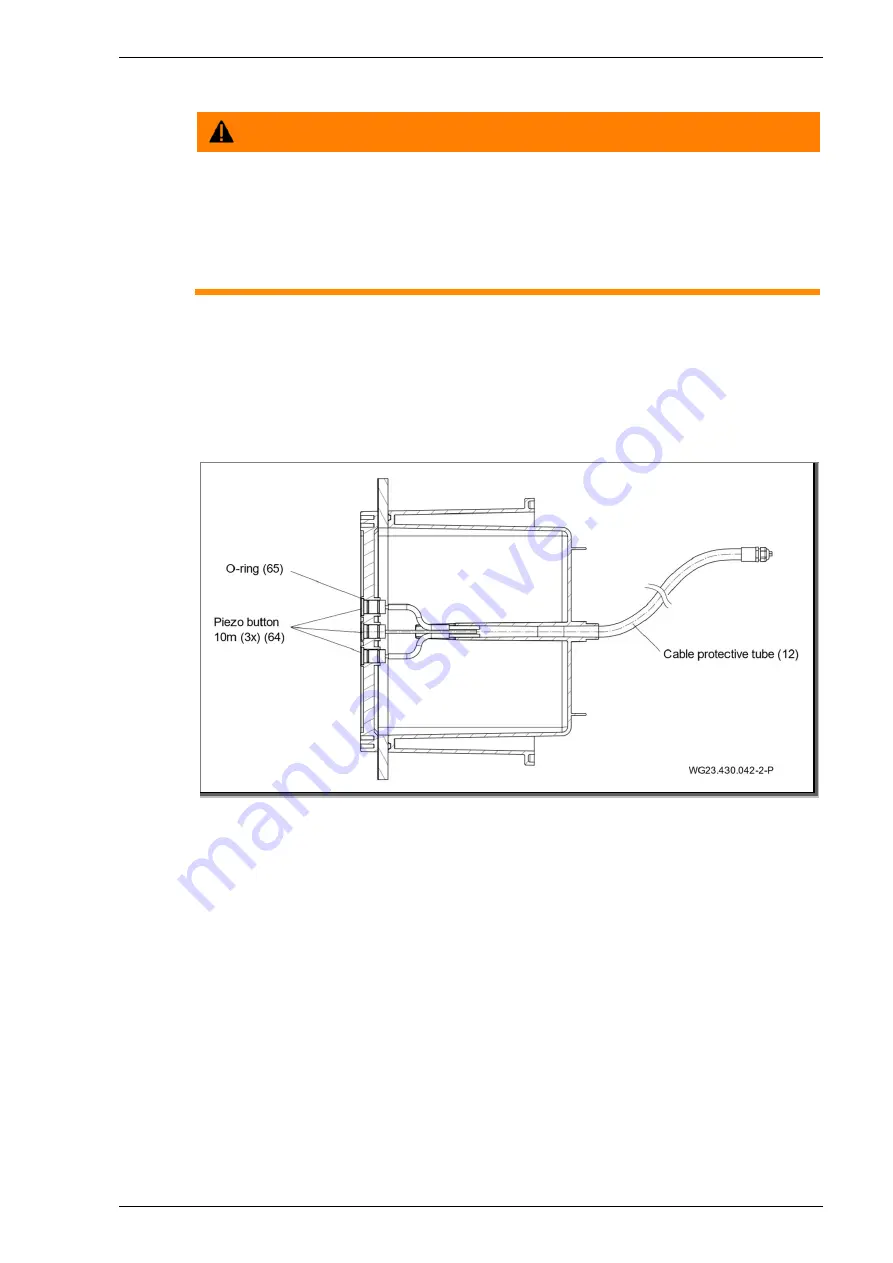
Installation
08|2020 EN
27
5.3
Final assembly (Qualified specialist)
WARNING
Risk of injury from sucking in/suction effect when the panel parts
are not installed!
All panel parts
must
be mounted.
All warranty and damage compensation rights will be voided for
damages due to noncompliance or incorrect installation.
5.3.1 Installing the piezo buttons
1. Feed the three cables through the cylindrical guide of the
plastic panel (5) and the installation housing (1).
2. Press in the piezo buttons (64) with two mounted O-rings
(65) each up to the stop.
3. Tighten the hexagon nut of the cable gland.
Fig. 12
Summary of Contents for BADU BADUJET Turbo Pro
Page 1: ...EN EN Translation of original operation manual Submerged counter swim unit ...
Page 20: ...Installation 20 EN 08 2020 Pool cutout for concrete pools formwork Fig 4 ...
Page 21: ...Installation 08 2020 EN 21 Installation of formwork for concrete pools Fig 5 ...
Page 34: ...Installation 34 EN 08 2020 5 4 4 Control cable wiring diagram Fig 18 ...
Page 49: ...Technical Data 08 2020 EN 49 10 2 Exploded drawing Fig 26 ...