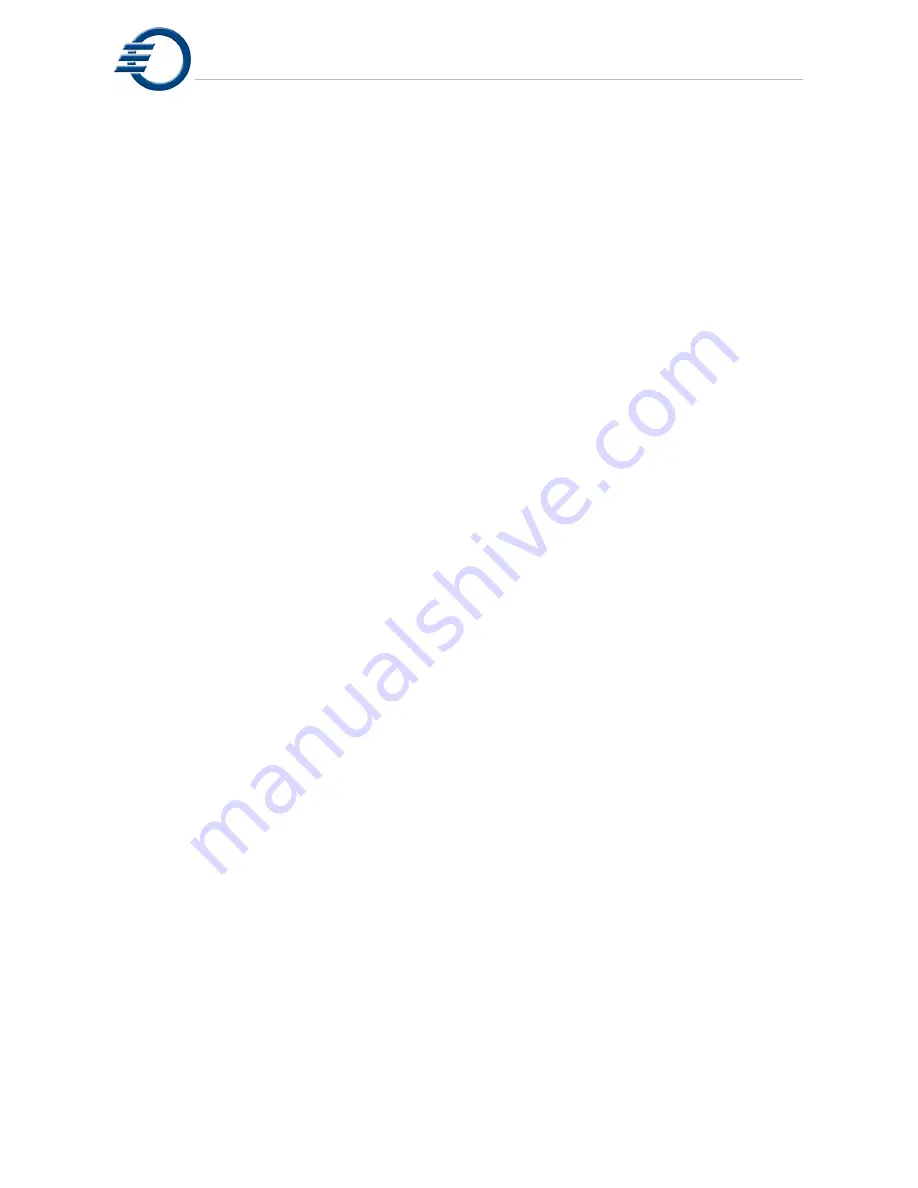
Post
Processing
58
4. Check the model every 15 minutes to evaluate its progress. It may be necessary to adjust
the heater control up or down slightly to maintain the bath within the ideal de-waxing range
of 50°C - 55°C without exceeding the 55°C maximum bath temperature. It may also be
necessary to flip or rotate certain designs to facilitate faster, more efficient de-waxing.
(Tweezers are a good tool for this.)
5. De-waxing is complete when the last residue of 3Z Support has dissolved off the model.
The slowest sections to dissolve are those that are in the least amount of contact with fresh
VSO, e.g. deep holes, channels, corners, etc.
6. It may be necessary to rotate or turn over certain models in order to allow them to de-wax
completely. Do this gently using tweezers or tongs or by hand (Wearing gloves is
recommended.)
7. Periodically during the de-waxing process lift the strainer out of the bath to inspect the
models. It is recommended also to raise and lower the strainer in and out of the bath a few
times in order to rinse the models of any debris that may be accumulating in the basket or
on the models.
8. Once the model is free of 3Z Support, gently remove the model(s) from the VSO bath and
place it on a paper towel to dry. (Small tweezers are a good tool for this.)
9. Turnoff the Heater Stirrer device unless you have additional models to de-wax.
10. At this time the models can be cleaned using soft bristled brushes and/or compressed air
depending on the robustness of the model geometry.
11.5 Post Processing Tool Kit Suggestions
Soft brushes of various sizes (¼”, ½” and 1” wide) with natural bristles for general parts
cleaning
Pipe cleaners (1 package) for cleaning small holes
Small picks (dental style probes) for cleaning small holes and tight spots
Syringe bulb (2” diameter “rubber” material) for spraying heated solvent in holes and
tight spots
Alcohol swabs for cleanup and polishing parts
Clear acrylic nail polish for mending and gluing parts
Soft shop paper towels for cleanup and drying
Wire strainer to isolate small parts in solvent bath
Canned or compressed air to blow off excess solvent
Rubber gloves (100 nitrile medical exam gloves) for working at length in solvent
Magnifying glass or 10X eye loupe for inspecting parts and offset calibration results
Drill bits (various sizes- size 16 to ¼”) to remove wax material from models
11.6 Model Evaluation
1. Use the following factors to evaluate model quality performance:
a. Printhead offset calibration is successful: Result is a good surface finish
b. Printhead volume calibration is correct: Result is sufficient build and support material in
the model, e.g., no voids on top surfaces or ‘spikes’ on bottom surfaces.
Summary of Contents for 3Z Max
Page 1: ...I 3zseries User Manual Part Number 840180 Rev F August 2013...
Page 5: ...VI...
Page 13: ...Cautions XIV...
Page 23: ...Power on Procedure 10...
Page 33: ...Job Finish 20...
Page 39: ...Maintenance and Printer Status 26 Figure 7 1 Printhead Screens...
Page 51: ...Printer Subordinate Systems 38...
Page 61: ...Connecting the Printer 48 Figure 10 9 Starting Windows 7 Control Panel...
Page 66: ...Connecting the Printer 53 Figure 10 15 Windows XP Network Connection Properties...
Page 67: ...Connecting the Printer 54...
Page 73: ...Post Processing 60...
Page 77: ...Technical Specifications 64...