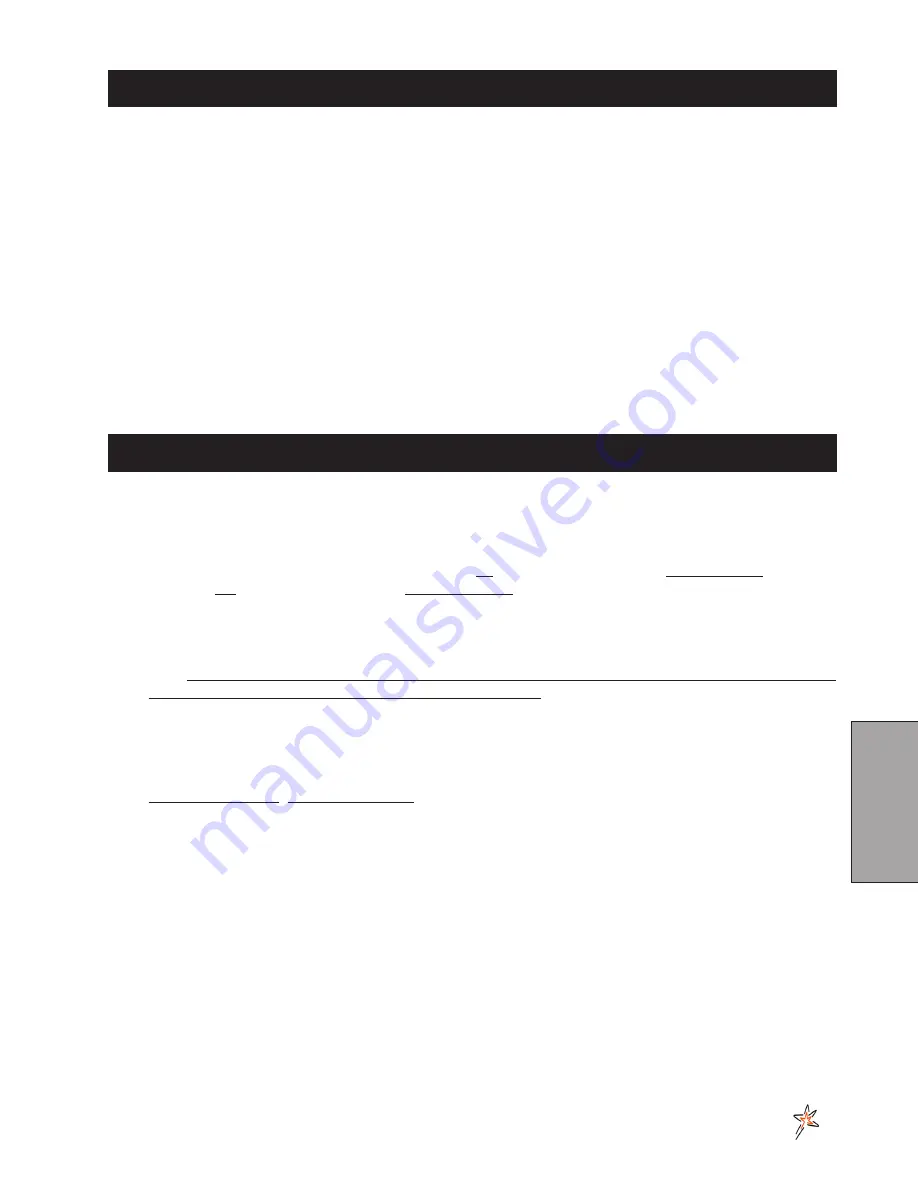
57
Accessories
26-008Q FLEX ACTION FIELD FINISHER PARTS LIST
REF# PART#
DESCRIPTION
QUANTITY
1 11-040
Spacer
3
/
4
" 2
2 HW-58
Washer
5
/
8
33
3
26-049
Mounting Bar
1
4
26-048
Flail Bar Strap
1
HB-38-16-150 Bolt
3
/
8
- 16 x 1
1
/
2
1
HNCL-38-16
Center Lock Nut
3
/
8
- 16
1
5 16-990
Spacer
1
6
HHP-18
Bridge Pin
1
/
8
1
7 43-146
Frame
1
8
18-297
Cap Plug
2
9
HMB-58-14
Machine Bushing
5
/
8
x 14GA
20
10
26-041
Rasp Flail
33
11
26-047
Leveler Bar
1
12
21-260
Clevis
2
13
26-115
Mesh Finisher
1
INSTALLATION INSTRUCTIONS
1. Install flail bar strap (Ref 4) to center of mounting bar (Ref 3) with chain on top of flail bar strap and
mounting bar bent away from you� Apply a light coat of lubricant to overall length of mounting bar�
2. Install one rasp flail (Ref 11) with knobby side down adjacent to sides of flail bar strap. Now install a flat
washer (Ref 2) so it sits adjacent with the outside of the rasp flail. Continue to install flails with knobby
sides down with washers between until you have
16
flails and washers on the
left hand side
of bar
strap and
17
flails and washers on the
right hand side
. Force all flails tightly toward bar strap.
3. After all 33 flails have been installed, place one spacer (Ref 1) to each end of mounting bar adjacent to
washer�
4� Install leveler bar (Ref 11) to mounting bar, with curved leveler bar resting on top on the smooth sides of
flails.
If all flails and washers do not fit snugly at this time, remove leveler bar and install enough
machine bushings by the spacer to ensure a snug fit. T
hen reinstall leveler bar�
5. Lay the frame (Ref 7) on the floor or bench with welded tabs facing up. Install ends of assembled
mounting bar, with knobby sides of flails up, into welded tabs on each end of frame and secure with
1
/
8
x
1 cotter pin�
6. Install flail bar strap (Ref 4) to center tab on frame with
3
/
8
-16 x 1
1
/
2
bolt and
3
/
8
-16 center lock nut�
Loose fit is required
� Do not over tighten�
7. Flip assembly over so knobby sides of flails are now facing down. Connect Finisher to the Quick Hitch
frame, locking securely in the locking mechanism, as illustrated�
8� Install bar strap chain over welded pin on frame� Install leveler bar chain on to pin and secure in place
with bridge pin. Use last bridge pin and clevis pin to hitch field finisher to your machine.
OPERATING INSTRUCTIONS
Running attachment with all flails down, flat on the surface, will provide a leveling function. Running attach
-
ment partially raised and flails at a 20° - 40° angle in relation to the level surface, will provide a finishing
function. The flails increase down pressure for desired finish. Drive in wide circular patterns and increase or
decrease ground speed to achieve desired finish.
Summary of Contents for Sand Star Zee 45-501-A
Page 18: ...16 Diagrams HYDRAULIC DIAGRAM ...
Page 20: ...18 Parts ZTR MAIN DRAWING ...
Page 24: ...22 Parts SEAT PANEL DRAWING ...
Page 26: ...24 Parts CONTROL PANEL GAS TANK DRAWING ...
Page 28: ...26 Parts ROLL BAR OIL TANK DRAWING ...
Page 30: ...28 Parts CENTER LIFT LINKAGE DRAWING ...
Page 32: ...30 Parts ELEC HYD REAR LIFT DRAWING ...
Page 34: ...32 Parts REAR HITCH DRAWING ...
Page 36: ...34 Parts ENGINE DRAWING ...
Page 38: ...36 Accessories 45 510 LIGHT KIT DRAWING ...
Page 40: ...38 Accessories 45 502 40 ALUMINUM PLOW DRAWING ...
Page 42: ...40 Accessories 45 502 40 ALUMINUM PLOW DRAWING ...
Page 44: ...42 Accessories 45 503 84 RAKE ASSEMBLY DRAWING ...
Page 46: ...44 Accessories 45 504 FLIP DOWN GRADER BLADE DRAWING ...
Page 48: ...46 Accessories 45 505 SPRING TINE SCARIFIER DRAWING ...
Page 50: ...48 Accessories 45 506 SAND CULTIVATOR DRAWING ...
Page 52: ...50 Accessories 45 507 SCARIFIER DRAWING ...
Page 54: ...52 Accessories 45 509 SCARIFIER DRAWING ...
Page 56: ...54 Accessories 26 007Q PROFESSIONAL INFIELD FINISHER DRAWING ...
Page 58: ...56 Accessories 26 008Q FLEX ACTION FIELD FINISHER DRAWING ...
Page 62: ...60 Accessories 42 392Q 84 213CM Pro Brush TOURNAMENT RAKE DRAWING ...
Page 64: ...62 Accessories Fig 1 Fig 3 Fig 2 42 392Q 84 213CM Pro brush TOURNAMENT RAKE DRAWING ...