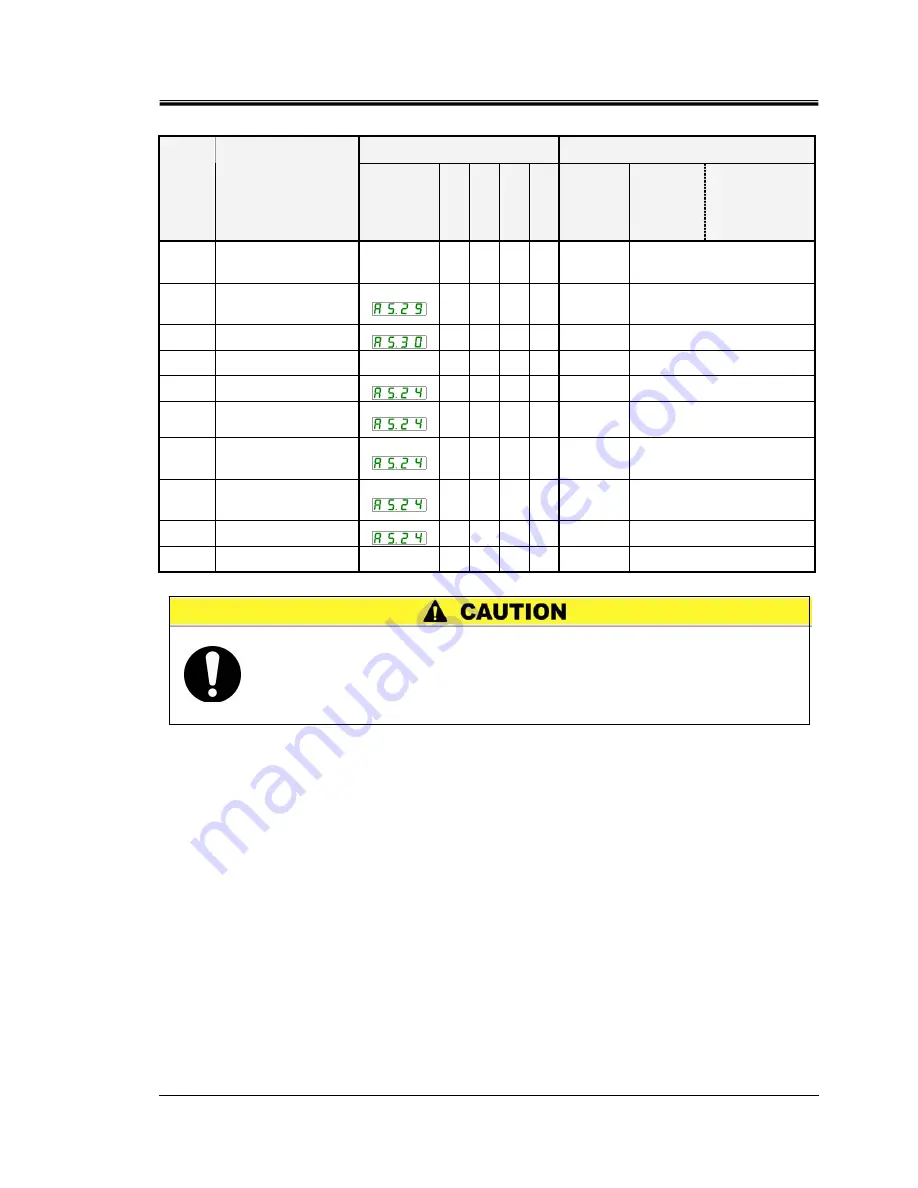
HRX-OM-Q026-B
Chapter 5 Display and setting of various functions
HRSH Series
5.20
Alarm customizing function
5-49
Table 5.20-4 Alarm setting and customizing (2/4)
①
Alarm operations
②
Alarm threshold and others
Code
Alarm name
Display
A.STP
A.R
UN
P.RUN
OFF Display
Default
setting
Settable
range
AL39
Internal unit fan
stoppage
- -
○
-
-
- -
AL40
Dust-proof filter
maintenance
-
○
-
●
- -
AL41 Power
stoppage
○
-
-
●
- -
AL42 Compressor
waiting
-
-
○
-
-
- -
AL43
Fan breaker trip
●
-
○
-
-
-
AL44
Fan inverter error
●
-
○
-
-
-
AL45
Compressor breaker
trip
●
-
○
-
-
-
AL46
Compressor inverter
error
●
-
○
-
-
-
AL47
Pump breaker trip
○
-
-
-
-
-
AL48
Pump inverter error
-
○
-
-
-
-
-
Changing the alarm operation to A.RUN or OFF from A.STP generates
alarms without stopping the product. Be sure to remove the cause of
the alarm immediately after the alarm occurred. Otherwise it may
cause a malfunction of the product.
Summary of Contents for HRSH150-A*-20 Series
Page 7: ...HRX OM Q026 B Contents HRSH Series Chapter 9 Product Warranty 9 1...
Page 8: ......
Page 177: ......