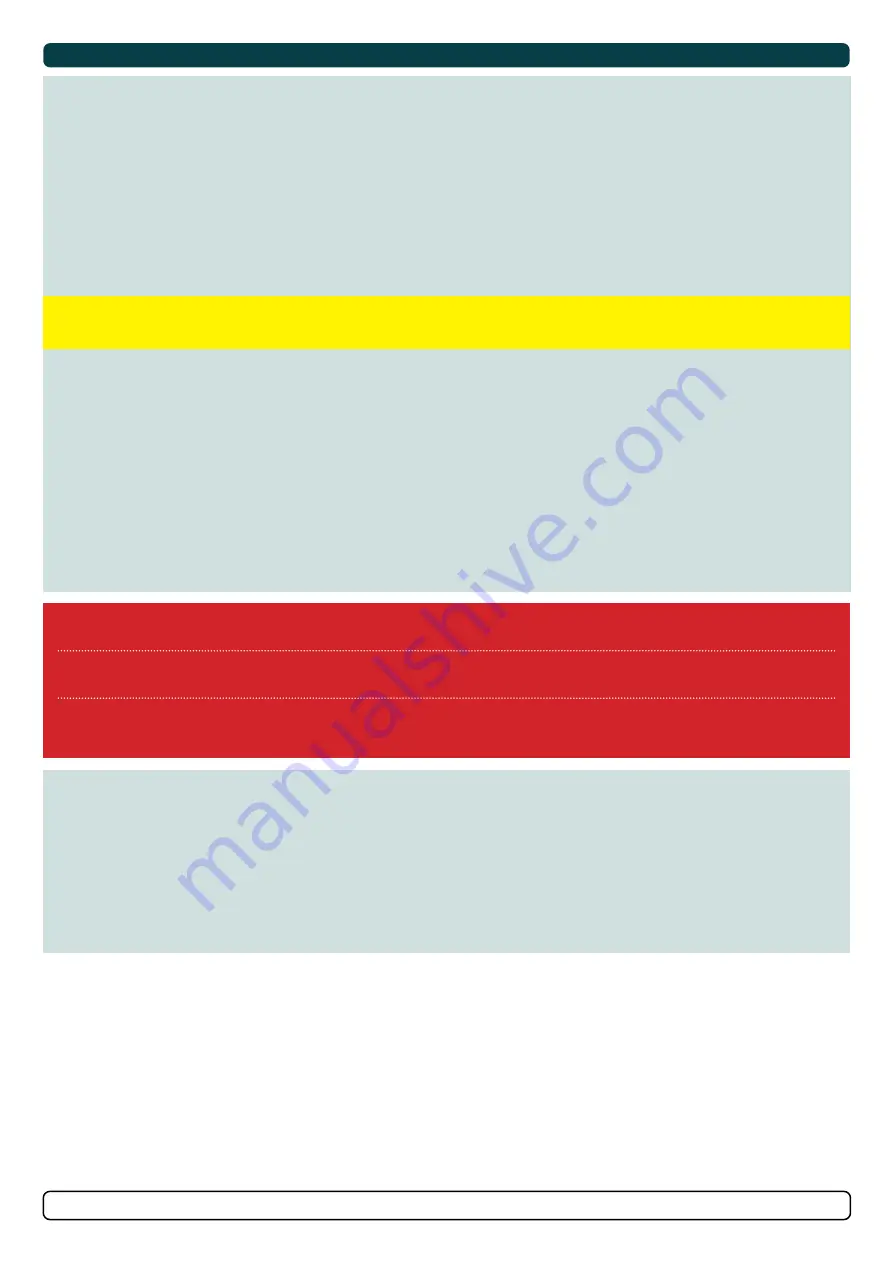
4
5251
5
2022
-
SPS-B
MC_0302
MC_0302
For stabiliser systems
Sleipner Motor AS is a manufacturing company of marine equipment and not a Naval Architectural company & therefore take no responsibility in
regards to the installation of our products onto seagoing vessels. This includes any requirement for the vessels:
• hull reinforcement.
• Change in the vessel’s stability.
• Dynamic performance.
• Weight and moment.
• Noise proofi ng.
• Watertight integrity after installation during normal operations or in the event of a collision.
It is the responsibility of the installer/boat builder to determine hull reinforcement requirements, ensuring that suffi cient strengthening measures
are in place & the vessel’s hull will withstand & maintain watertight integrity in the event of a collision of our product, impacting an object when the
vessel is underway.
For special yacht design stabilisers
Provide servicing access hatches to stabilizer actuator assemblies for the removal & installation of Stabilizer fi n shafts if & when required.
When the Stabilizer System ‘At Anchor’ function (optional) is installed, position and soundproof the hydraulic power pack (AC generator & pump), the
actuator assembly compartments and hydraulic hoses, to ensure excess noise will not disturb sleeping passengers.
Ensure provisions to maintain the yachts watertight integrity in the event of a fi n collision.
The stabilizer product includes heavy parts. Ensure suitable lifting and support equipment is available during installation & removal to prevent
material damage or personnel injury.
During yacht lifting operations:
•
Ensure the stabilizer fi ns are in the locked/neutral position.
•
Lifting personnel are informed that stabilizer fi ns are installed preventing the danger of snagging the lifting slings & damage to the yacht, its
equipment or injury to personnel.
Yacht transportation overland with road vehicles may require the removal of the stabilizer fi ns & shafts. Please contact Sleipner representatives for
instruction procedures.
Do not remove the equipment orifi ce protection blanks or covers until ready for use, preventing the ingress of undesired contamination.
(NB: Hydraulic operated equipment must be clean and debris free at all times.)
Avoid applying anti-corrosion protection lubricants to the hydraulic actuator cylinder rods as this can attract dirt and debris causing oil leaks due to
damaged seals. On completion of the installation and yacht launch thoroughly check for leakages & the yachts hull watertight integrity is maintained.
IMPORTANT
The installer must use the Hydraulic system manual and specifi c system manual as a supplement to ensure necessary knowledge to
complete the installation.
WARNING
Ensure electrical & hydraulic power is switched off before any servicing work is carried out on the stabilizer system.
With power, the Stabilizer systems with ‘at anchor’ function installed & ‘Auto’ selected can suddenly operate & move without
warning.
Hydraulic equipment (including Nitrogen pressure-fi lled accumulator) operates at high pressure. Ensure that all system pressure
is released before carrying out any servicing work. Never carry out any welding, soldering or mechanical work on the accumulator
unit.
MC_0440
General Installation Considerations and Precautions Guidelines