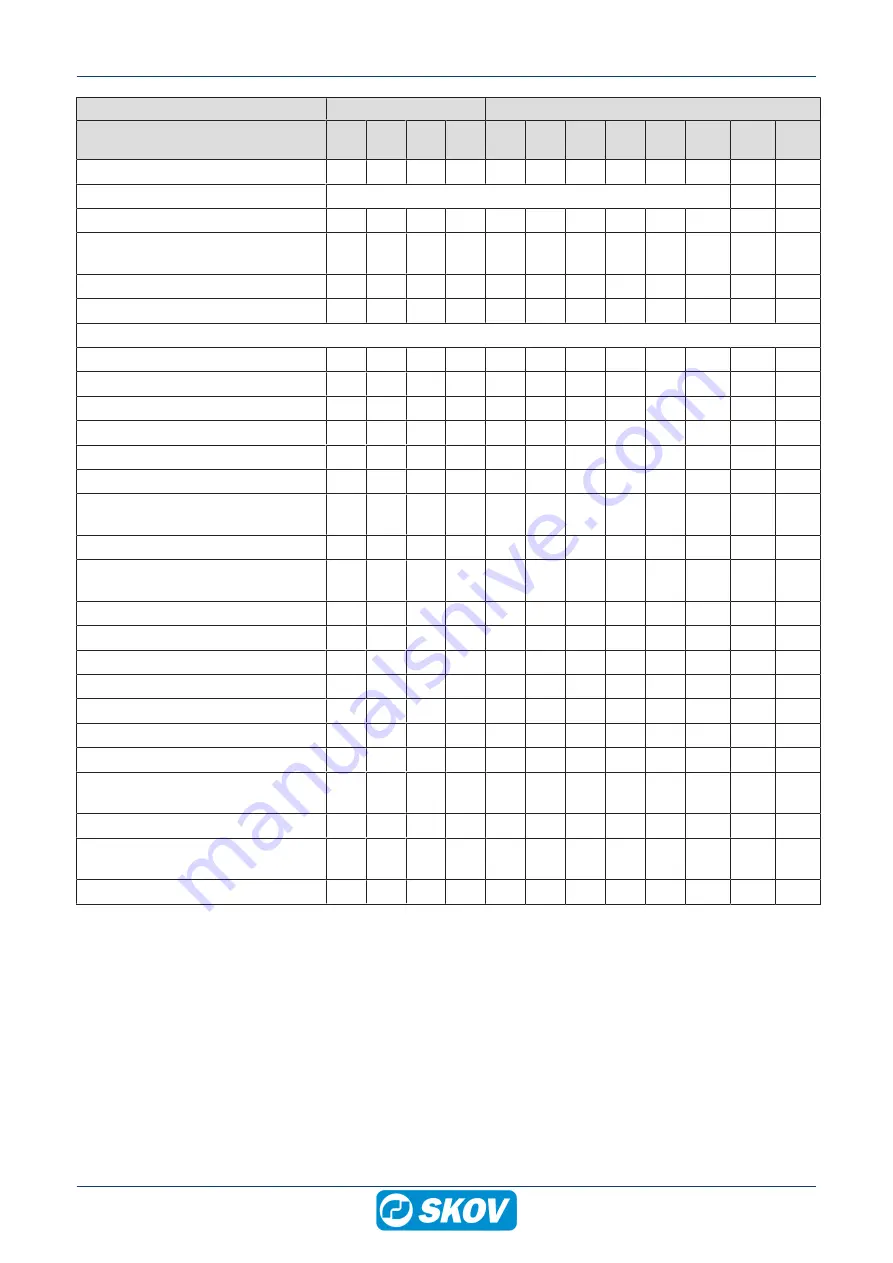
DOL 535 • DOL 539
64
Technical Manual
DOL 534 Climate
DOL 535 Production
System software
LPV
CT
T
Nat. Bro
P
Bre
L
Bre
M
Bre
S
Lay
L
Lay
M
Lay
S
24-hour clocks
1
1
1
1
10
4
10
10
10
10
8
6
Egg counter
Egg counter
32
16
32
8
1
Egg counter positioning input termi-
nals
6
4
Egg sizes
X
X
Egg weight
X
X
X
X
X
Miscellaneous
Number of houses per controller
1
1
1
1
1
1
1
1
1
1
1
1
User-defined inputs
6
6
6
6
6
6
Interval timers
6
6
6
6
6
1
Auxiliary sensor
8
8
8
4
Reference values
X
X
X
X
X
X
X
X
X
X
X
X
Key values
X
X
X
X
X
X
X
X
Curve control (temp., humidity, min.
vent, max. vent.)
X
X
X
X
X
X
X
X
X
X
X
X
History curves
X
X
X
X
X
X
X
X
X
X
X
X
In-between function (soaking/wash-
ing/drying/disinfection)
X
X
X
X
Catching
X
X
X
X
X
X
X
X
X
X
X
Ventilation boost
X
X
X
X
User-defined front views
X
X
X
X
X
X
X
X
X
X
X
X
Frost protection of empty section
X
X
X
Three password levels
X
X
X
X
X
X
X
X
X
X
X
X
Comprehensive alarm functions
X
X
X
X
X
X
X
X
X
X
X
X
Operation and alarm logs
X
X
X
X
X
X
X
X
X
X
X
X
Support of emergency opening DOL
278T
X
X
X
Energy consumption monitoring
8
8
8
8
8
8
8
8
8
8
8
8
Status on equipment (current sen-
sor)
64
64
64
64
Remote Access (via FarmOnline)
X
X
X
X
X
X
X
X
X
X
X
X
* Only for production of broilers on floor.