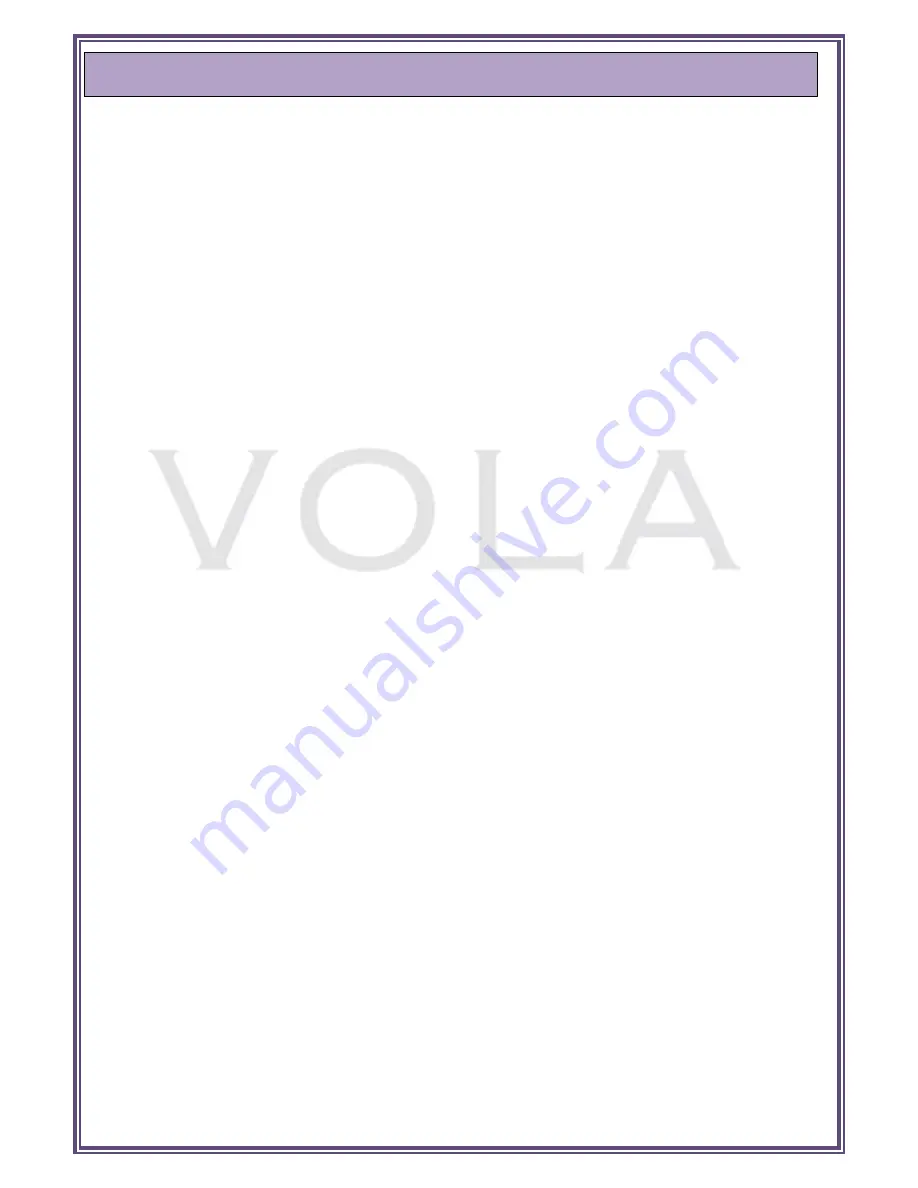
7
Gas Group
G20 Natural Gas CAT
I2H
Inlet Pressure
20 mbar
Max Input (gross)
5.3
Min Input (gross)
3.2
Setting Pressure
20 mbar
Gas Inlet connection
8mm Compression
Overall Height
596
Overall Width
500
Overall Depth
252
Recess Height
555
Recess Width
382
Recess Depth
250
Air Vent
N/A
Manual
Slide
Pilot Assembly &
Thermocouple
Thermaco NG
OXI-PG-82-460
Or
SIT NG9017
Thermaco NG
OXI-PG-82-460
Or
SIT NG4711
Valve
SEAGAS V4-78A A13
Teddingtons TESA
3173/011
Injector
STEROMATIC 360
STEROMATIC 360
Section 3: APPLIANCE INFORMATION