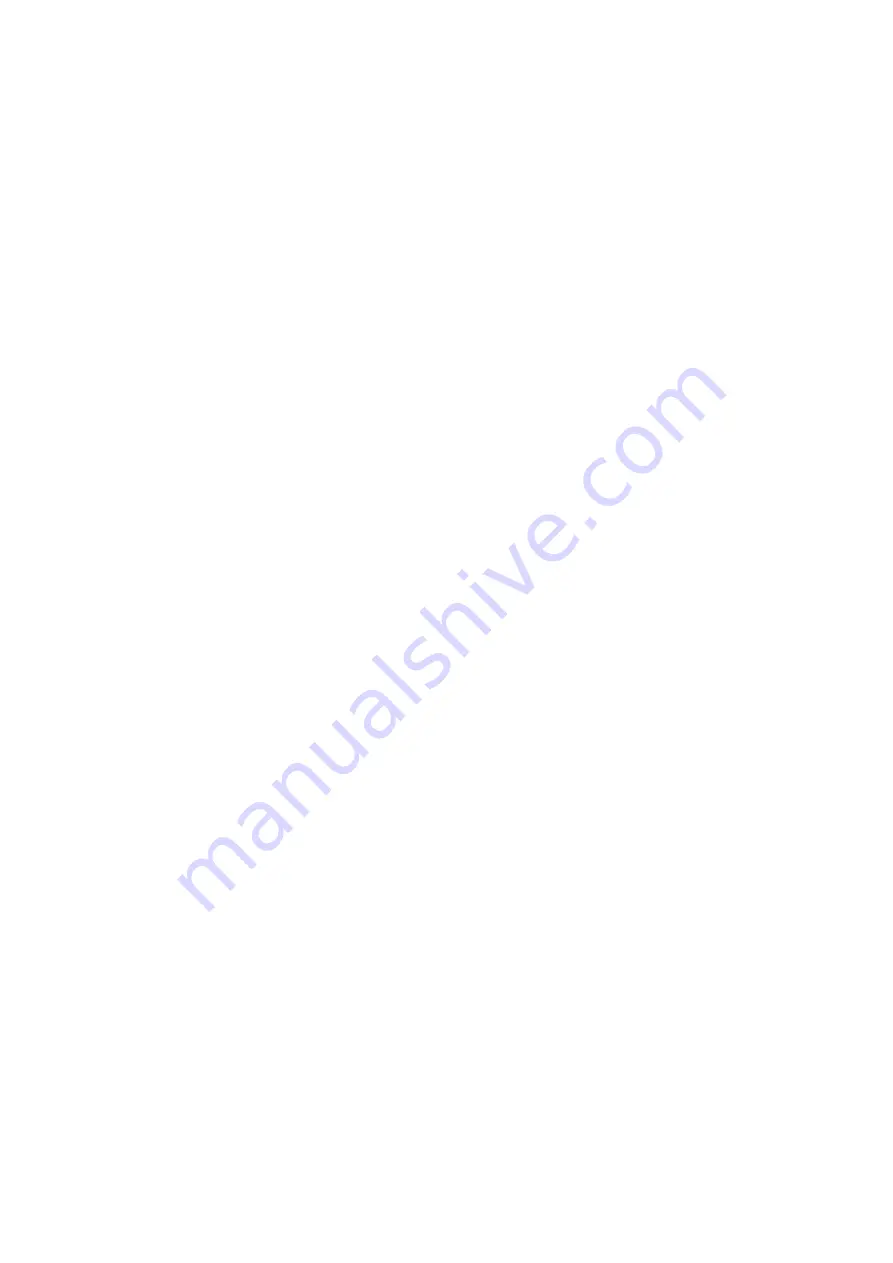
9
• A horizontal and vertical space of at least 20mm
from the lower surface of the cooking hob and at
least 20mm from the downdraft must be foreseen
so as to create a passage for the air necessary to
cool the product (refer to the above illustration).
• There must be an opening of at least 50mm the
whole width of the kitchen unit in the lower and
rear part of the furniture to allow for the passage
of air to avoid the product overheating.
• Ensure that the passage of air in the lower part of
the kitchen unit permits a constant flow of air to
cool the product, i.e., a vent in kicker.
• Fitting the oven underneath the cooking hob is
possible with fan-cooled ovens. Before installing
the oven, remove the rear wall of the kitchen
unit where the oven will be fitted into the kitchen
furniture.
There must also be a minimum aperture of 5mm
in the front part and above all in the lower part
of the kitchen furniture to ensure an adequate
passage of air necessary to cool the product.
PRE-INSTALLATION CHECKS
Connect all of the electrical components to the unit
and motor to make sure both the unit and the motor
are functioning properly.
(NOTE: The motor plug is fitted with a dummy
plug - with the exception of SEM1 motor - to
protect the connection from dust. Ensure the
red dummy plug is removed and replaced
with the two pin motor plug from the power
transformer box. Failure to do so will result in
only two speeds operating).
Before installing the product, check that all
components are not damaged. If any components
are damaged, contact the retailer and do not go
ahead with the installation.
Before installing the downdraft, remove the safety
spacer highlighted in the photograph
(Fig. 1, Page 38).
Furthermore, carefully read all the instructions as
follows:
• Utilise an air extraction duct that has a maximum
length of not more than 7 metres.
• Limit the number of curves in the duct because
each curve reduces the efficiency of the
extraction equal to 1 linear metre (E.g., if two 90°
curves are utilised, the length of the duct must
not exceed 5 metres in length).
• Avoid drastic changes of direction.
• Utilise a duct with a 200mm diameter along its
whole length.
• Utilise a duct that is manufactured from material
approved to the norm. The supplying company
will not respond to problems of flow capacity or
noise if there is a lack of respect of the previously
mentioned instructions and the guarantee will be
annulled.
1. Position the support bracket of the downdraft in
the rear part of the realised aperture (refer to Fig.
2).
2. The bracket must be positioned approximately
two/three millimetres from the upper surface of
the worktop, as shown in Fig.3.
3. Fix the support bracket of the downdraft to the
worktop by utilising the screws supplied in the
case of wood worktops. For worktops realised in
materials different to wood, utilise the appropriate
screws.
4. Utilise the upper and lower holes positioned in the
support bracket of the downdraft in accordance
with the thickness of the worktop into which the
product is installed.
5. Fix the two worktop reinforcement telescopic
structures to the lower sides of the support
bracket of the downdraft, as shown in Fig. 4.
6. After fixing the reinforcement structures, adjust
their telescopic travel so as to reach the base
underneath (Fig. 5). Fix the structure to the base
underneath utilising the screws supplied.
7. Check that the worktop is perfectly level then
block the travel of the structures utilising the four
self-threading screws, positioned as in Fig. 6.
8. Insert the downdraft into the installed support
bracket (refer to Fig. 7). The fixtures positioned
on the downdraft must coincide perfectly with the
support bracket installed in the kitchen unit (refer
to Fig. 8).
9. Install the cooking hob ensuring that the opening
at the rear of the product coincides perfectly with
the downdraft (refer to Fig. 9).
Summary of Contents for S-DDH1.1
Page 6: ...6 TECHNICAL DRAWING...
Page 38: ...38 INSTALLATION GUIDE FIG 1 FIG 3 FIG 5 FIG 2 FIG 4 FIG 6...
Page 39: ...39 FIG 7 FIG 9 FIG 11 FIG 8 FIG 10 FIG 12...
Page 40: ...40 FIG 13 FIG 15 FIG 14 FIG 16...
Page 44: ...44...