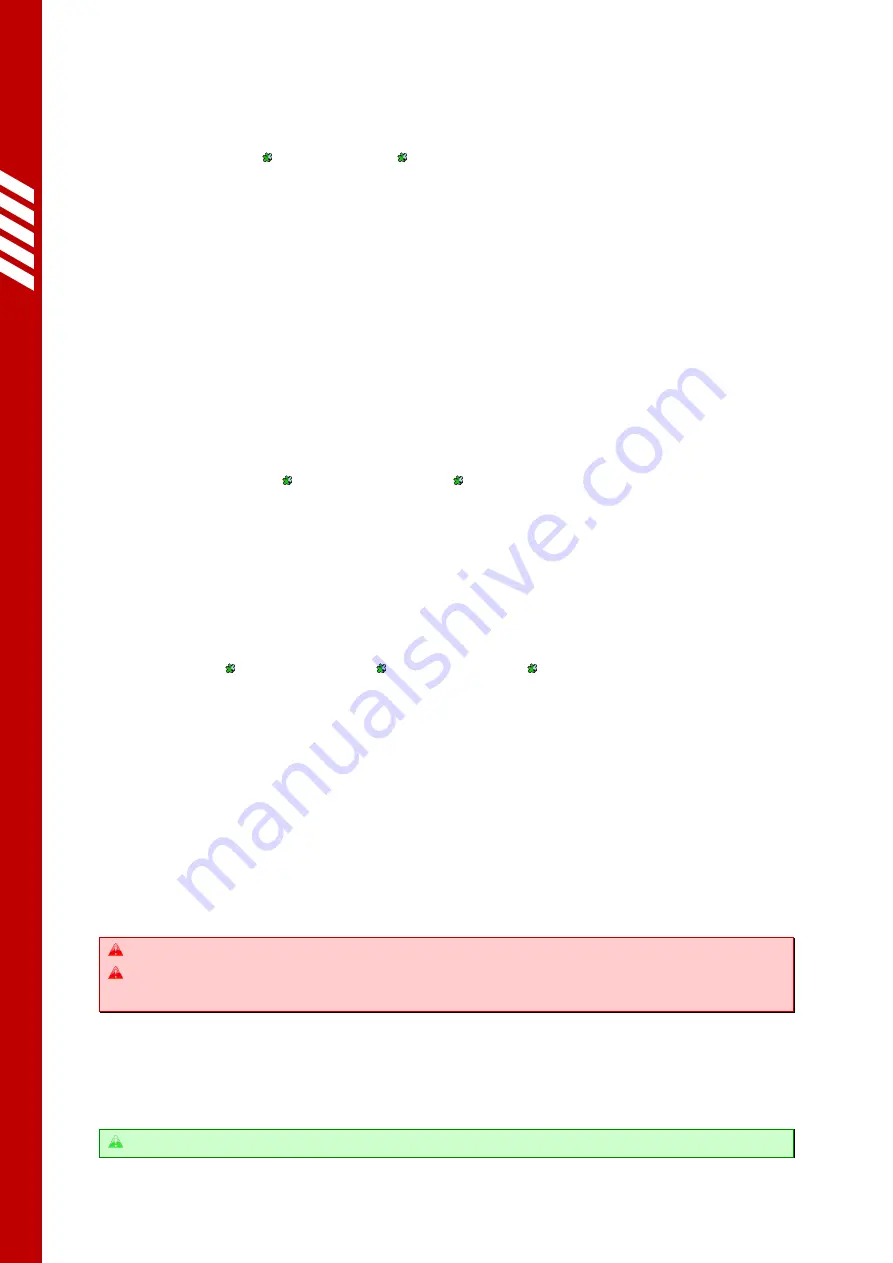
3.7
Hydraulic System
3.7.1
Powerpack
The hydraulic powerpack is supplied as a complete unit. The motor, pump, oil tank, and all
control valves are mounted into the centre manifold.
3.7.2
Control valves
The hydraulic system has four primary control valves:
3.7.2.1
Check valve
This is a one-way valve which prevents oil from flowing back through the pump when the
motor is stopped.
3.7.2.2
Pressure-relief valve
This is a spring-loaded valve which allows oil to flow back into the reservoir when the
hydraulic pressure exceeds its rated limit
–
usually from lifting an overweight bin, or from
operating the machine when the cradle is already at the top of the cycle.
3.7.2.3
Lowering valve
This is a solenoid-operated valve which opens when the LOWER button is pressed and allows
oil to flow back to the reservoir, lowering the cradle.
3.7.2.4
Lowering-speed valve
This is a pressure-compensating valve which limits the maximum flow rate of oil passing back
to the reservoir through the lowering valve
–
thus regulating the descent speed of the cradle
(regardless of the weight of the bin).
3.7.3
Lift ram
The lift ram is a single-acting displacement type, very robust and reliable, but easy to
maintain should the need arise. Hydraulic lines run from the powerpack to the lift ram.
3.7.4
Hydraulic fluid
The hydraulic system is designed to use mineral oil-based fluid with a viscosity grade of 22
(ISO VG22). Fluid with a higher viscosity grade may be used, but this will reduce the lowering
speed of the cradle and increase the likelihood of jams.
The hydraulic fluid should have physical lubricating and chemical properties as specified by:
-
Mineral Oil Based Hydraulic Fluids HL (DIN 51524 part 1)
-
Mineral Oil Based Hydraulic Fluids HL P (DIN 51524 part 2)
Ensure the cradle is completely lowered before replacing the hydraulic fluid.
The hydraulic reservoir has markings showing the recommended fill level. Do not fill
beyond this level unless specifically instructed by the manufacturer.
3.7.5
Maintenance
After every 12 months of operation the hydraulic fluid should be drained and replaced, as
per specifications in
. The intake suction-filter and the lowering valve should also be
removed and cleaned at this time.
See
Summary of Contents for Multi-Tip MT1200
Page 1: ...User Manual Simpro Multi Tip Original Instructions English v83 0 October 2022 USER MANUAL...
Page 3: ...User Manual Simpro Multi Tip Original Instructions English v83 0 October 2022 Page 2...
Page 43: ...User Manual Simpro Multi Tip Original Instructions English v83 0 October 2022 Page 42...
Page 47: ...User Manual Simpro Multi Tip Original Instructions English v83 0 October 2022 Page 46 9 Notes...