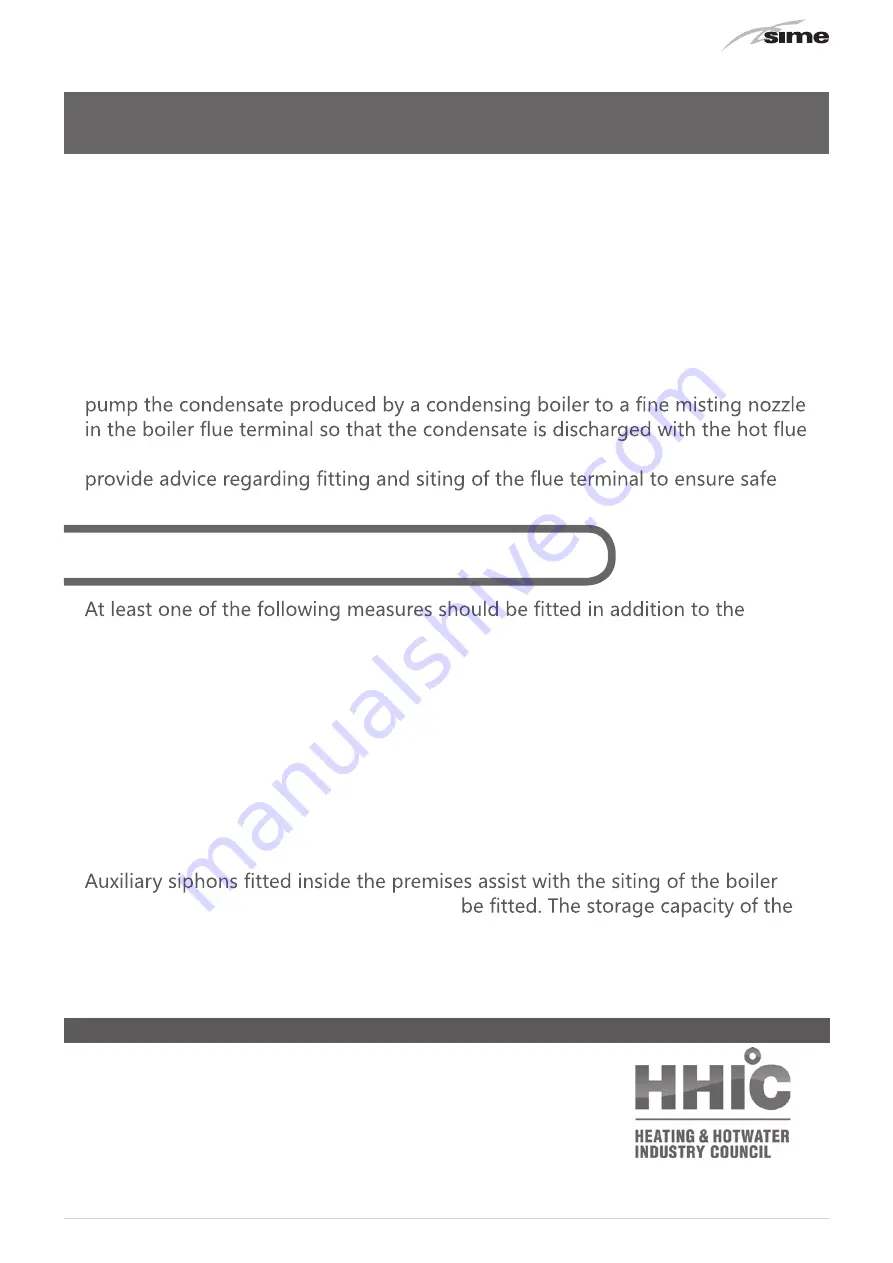
69
External Connections
Alternative Solutions
Cold weather protection methods approved or endorsed by boiler manufacturers
and/or service organisations may be adopted if these are considered suitable by
the parties involved. It is the responsibility of the manufacturer of these products
to ensure they have completed the necessary testing or calculations to ensure
the product offers suitable protection to prevent the condensate pipe from
freezing. The product manufacturer should provide information as to what level
of external temperature and for what time period the product can protect against
sub-zero temperatures, i.e. -15°C for 48 hours. BS6798 refers to devices that
gas. (BS6798 section 6.3.8 note 4). The boiler manufacturer’s instructions will
disposal of the condensate.
Additional Measures
measures detailed above for external condensate discharge pipes
•
Insulate external pipe with a minimum thickness of insulation to be 19mm
“O” class PVC coated material.
•
Fit trace heating – with insulation as recommended by manufacturer.
•
Fit internal auxiliary(additional) high volume syphon unit
Auxiliary Syphon – Fitted Internally
where an external condensate pipe
must
auxiliary siphon increases the volume of condensate discharge reducing the risk
of freezing. A further reduction in the potential for the pipe to freeze is achieved
when combined with the external insulation requirements.
October 2018 Issue 1.0
Summary of Contents for 8116910
Page 4: ...4 ...
Page 14: ...14 ...
Page 54: ...54 9 EXPLODED VIEWS Frame ...
Page 55: ...55 Hydraulic assembly ...
Page 56: ...56 Exchanger Combustion ...
Page 57: ...57 Control panel ...
Page 58: ...58 Gas valve Air gas duct Fan ...
Page 79: ...79 ...