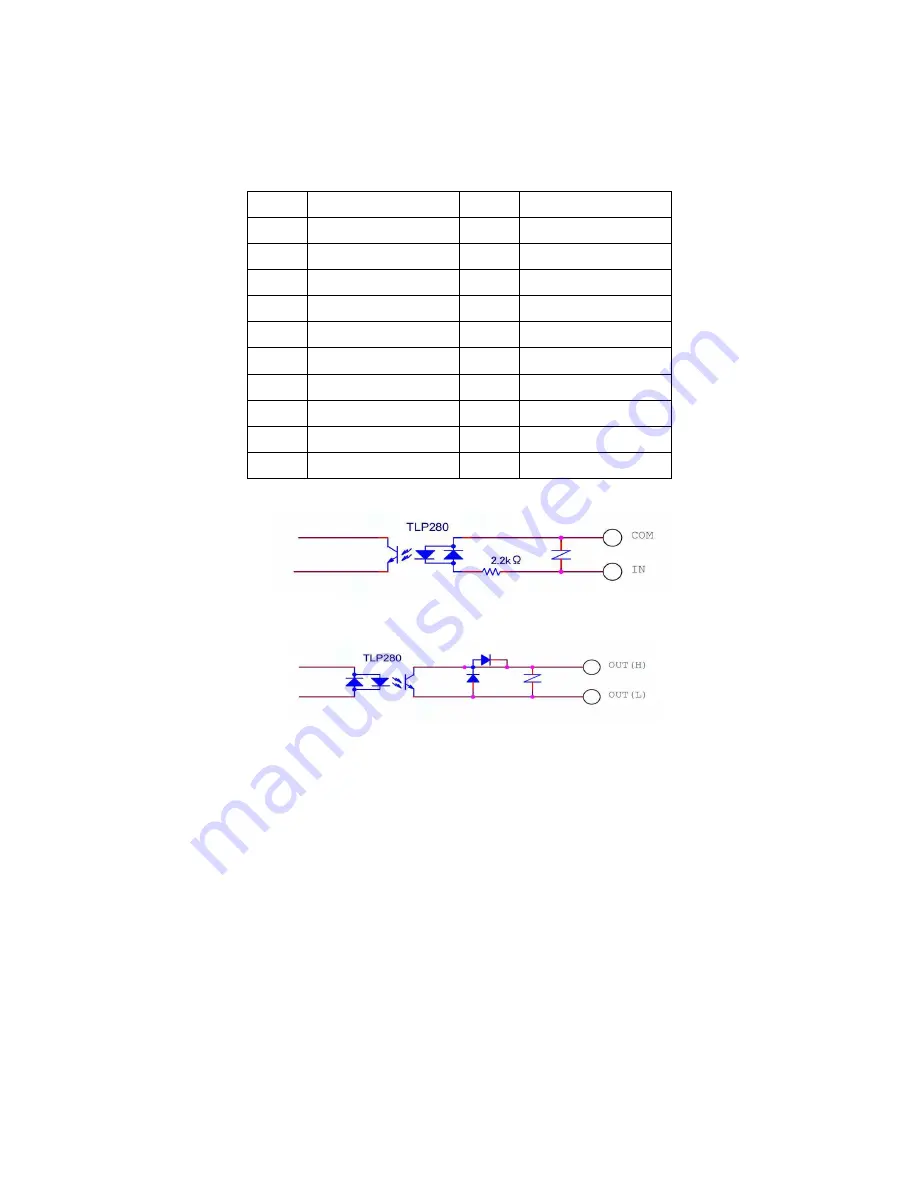
Copyright 2018, SIGMAKOKI Co.,Ltd.
70
6-2.Connector Pin Assignments
6-2-1 I/O Connector
No.
Description
No.
Description
1
IN COM
11
IN1
2
IN2
12
IN3
3
IN4
13
-
4
-
14
-
5
OUT1 (H)
15
OUT1 (L)
6
OUT2 (H)
16
OUT2 (L)
7
OUT3 (H)
17
OUT3 (L)
8
OUT4 (H)
18
OUT4 (L)
9
-
19
-
10
+V (DC24V)
20
GND
Connector 10220-52A2PE (by Sumitomo 3M Limited) used
Figure 5-2-1
:
IN1
~
4 Input Circuit Diagram
Figure 5-2-2
:
OUT1
~
4 Output Circuit Diagram