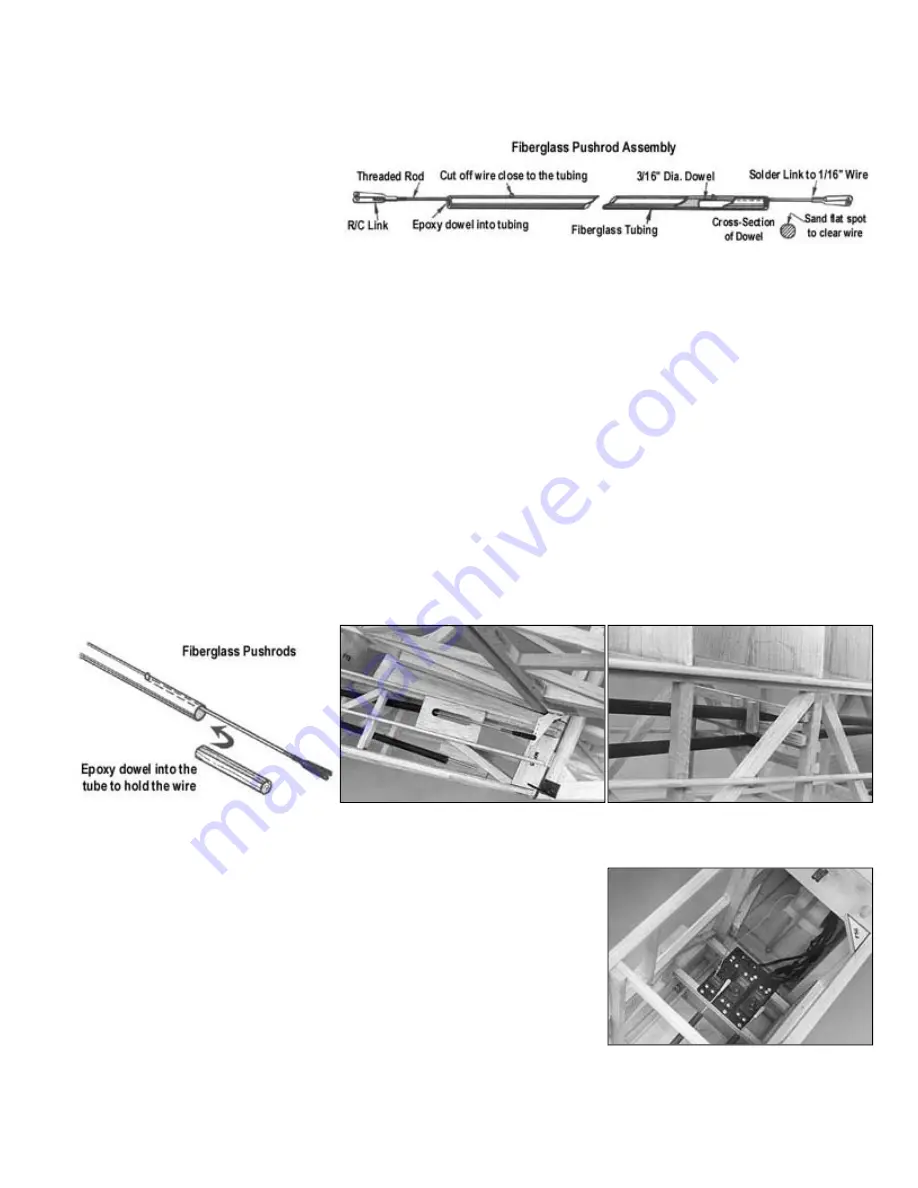
.
A long nylon control horn is supplied for the elevator. Install it on the bottom of the left elevator with #2x3/4" sheet metal
screws. Once installed, cut off the excess ends of the screws flush with the top of the nylon retainer plate.
Pushrod Assembly
Materials are supplied for building
fiberglass pushrods to link the elevator
and rudder servos to their control horns.
Make the control surface ends of the
pushrods first.
Put a 90° bend in the unthreaded end of the 4-40x8" threaded rod. Drill a 3/32" diameter hole 2" from the end of the
fiberglass pushrod tube. Slide the 4-40 rod into the tube, sticking the 90° bend through the hole.
Sand a flat spot on one side of the 3/16"x2-1/2" dowel until it can be squeezed into the tube alongside the 4-40 rod. When
you get the fit right, final assemble the parts into the tubes with epoxy glue. It should not be necessary to put any bends in
the 4-40 wires of either the elevator or rudder pushrod to get them to feed through the fuselage and hook up to the control
horns. It's a pretty straight shot if your servos are positioned side by side as shown in a previous photo. However you may
have to trim out a portion of the diagonal 5/16" sq. main frame balsa under the stab to clear the elevator pushrod wire.
Assemble the servo ends of both pushrods in the same fashion, only use 1/16" dia. x 8" music wire and solder links instead
of the 4-40 size hardware. After you've got the 1/16" wires and dowels epoxied into the tubes, feed the pushrods back into
the fuselage and hook up to the control surfaces. Center the 4-40 links on the threads at the tail end. Then measure and
cut off the 1/16" wires at the front, to the length which will allow the solder links to reach the servo arms. Protect the servos
with a rag while soldering the links onto the ends of the wires.
Your elevator and rudder pushrods should now be complete and operating freely. Fill in around the 4-40 pushrod wires
where they exit the fuselage with scrap sheet balsa, glued in flush with the stringers.
Brace the pushrods in the middle (near former F9) with 1/4" sq. scrap balsa to eliminate any possibility of in-flight vibration
or bowing problems. Criss-cross pieces of 1/4" sq. stick on all four sides of each push rod. Glue them to the 5/16" sq. main
frame balsa. Have the braces touching the pushrods, but not creating a bind.
Throttle Hookup
Either a standard or heavy-duty servo can be used for the throttle control on a .60
to .90 glow engine. A flexible steel cable pushrod with nylon outer tubing (*, such
as SIGSH559) is best for hookup of the throttle servo to the carburetor. Follow the
assembly instructions on the pushrod package.
Battery Pack
Due to the larger than normal battery drain from using heavy-duty servos, a 1000
mah receiver battery pack (*) is recommended. Wrap the battery pack in foam
rubber (*, such as SIGRF240) held on with rubber bands or masking tape, to
protect it from engine vibration. Secure it as far forward as possible in the nose
under the fuel tank.