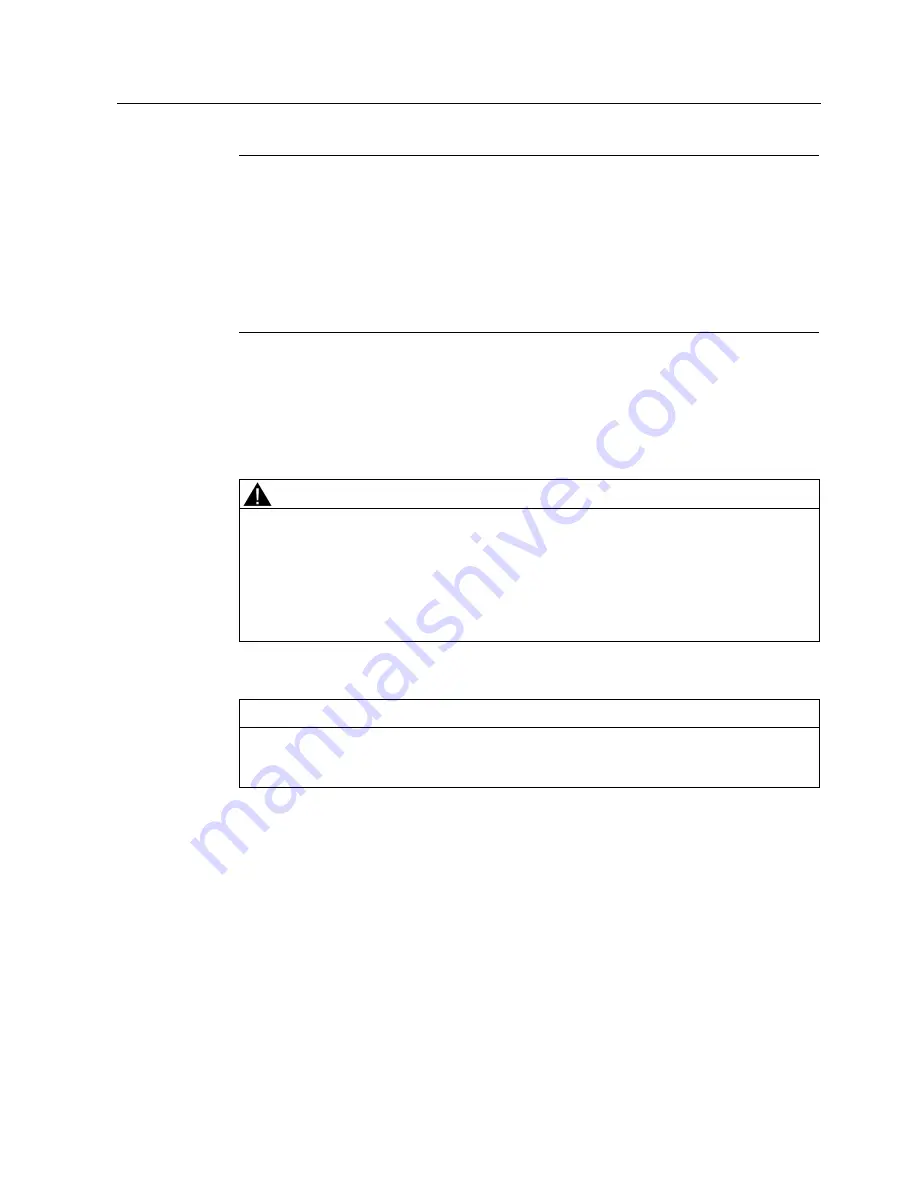
Installing
4.5 Purging
SITRANS SL
Operating Instructions, 12/2010, A5E01132948-04
65
Note
When continuous purging is needed, make sure that the purging gas rate is 3 to 5 l/min. This
rate assures that there is time enough to flush all measurement components out of the
sensor. Purging with nitrogen on the sensor side is almost always necessary for O
2
applications to avoid an offset caused by the oxygen of the air present in the unit. The cells
in the sensor head are then continuously purged with nitrogen. Particularly when (re)starting
the SITRANS SL O
2
, a sufficiently high flow of purging gas of approx. 3 to 5 l/min must be
provided for several minutes to ensure that all residues of oxygen are displaced. The flow of
sensor purging gas can subsequently be set to a lower value using the needle valve
(included in delivery).
4.5.2
Process side purging
This function is optional. With this option a needle valve is supplied with the analyzer. It is up
to the customer to mount it on the process interface.
WARNING
Observe that the use of this needle valve opens up into the process. The process must be
permanently monitored if it is under pressure. If any danger for personnel or equipment can
arise from the over pressurized process we recommended to mount a check valve on the
process interface to prevent flow out from the process.
Make sure that under no circumstances the process gas will intrude into the purging
system. This applies particularly to a cascaded sensor and process purging which
otherwise may lead to ingress of corrosive process gases.
CAUTION
Always install the purging system before you install the sensors to avoid damage to the
optics during the rest of the installation process. For optimal results use sensors equipped
for the specific purging type, supplied by Siemens AG.