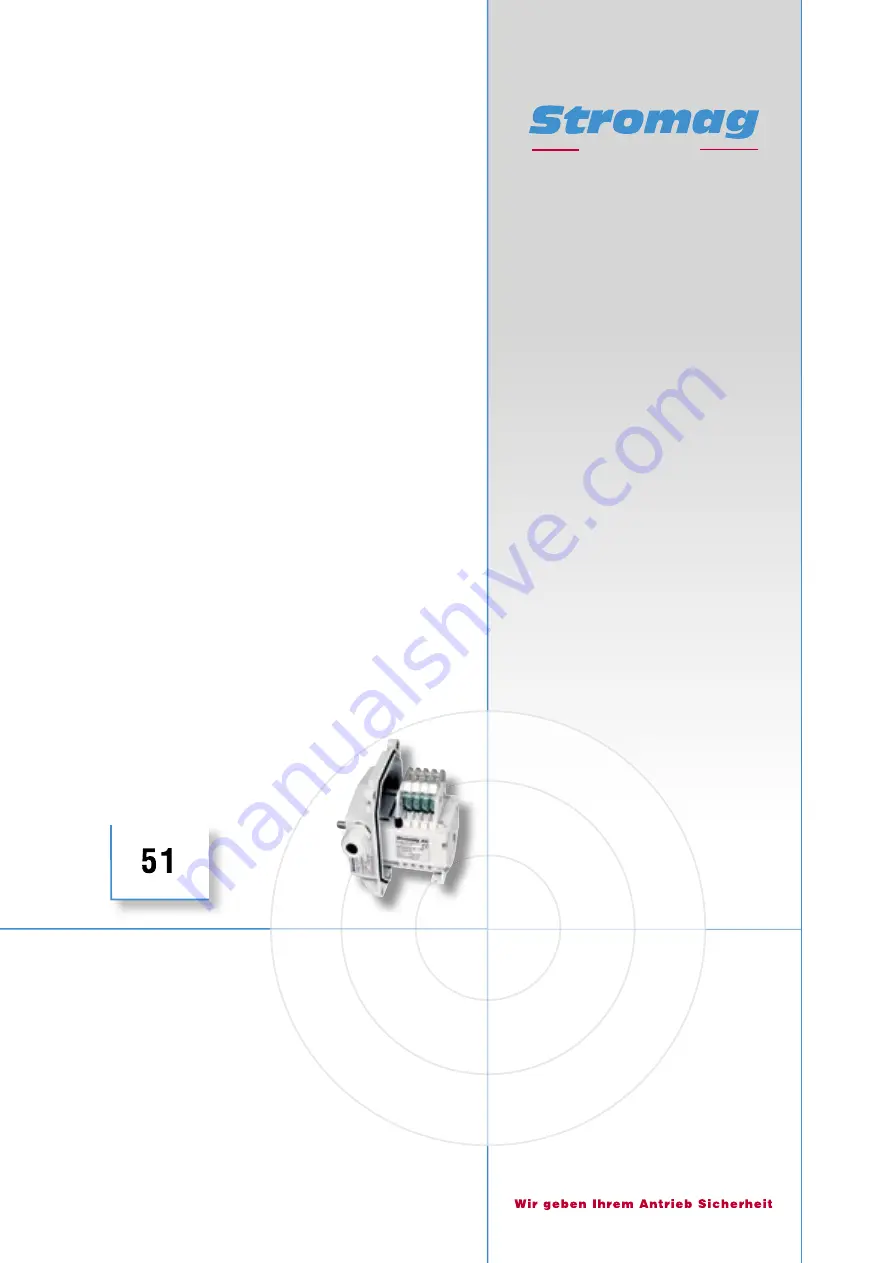
- Planetengetriebe: Kunststoff
- Präzise
- Sehr einfach einstellbar
- Gehäuse: Kunststoff oder Aluminumguss
- Planetary gears: plastics
- Precise
- Very simple adjustment
- Housing: Plastics or aluminium cast
Getriebe-Nocken-
Endschalter
Serie 51 / 51 DZ
Geared Cam
Limit switches
safety in motion
Summary of Contents for SIMOTICS 1LA
Page 36: ......
Page 85: ...49 ...
Page 88: ...COD 1261 R3 INDUSTRY PROCESS AND AUTOMATION SOLUTIONS w w w b o n f i g l i o l i c o m ...
Page 89: ... i Bonfiglioli Trasmital 300 series Installation use and service manual ATEX INCLUDED ...
Page 130: ... Bonfiglioli Trasmitol 41 ...
Page 132: ......
Page 135: ...SPRING APPLIED BRAKE WITH ELECTROMAGNETIC RELEASE 38 mm Page 2 of 2 180 Volts 16 39599 ...