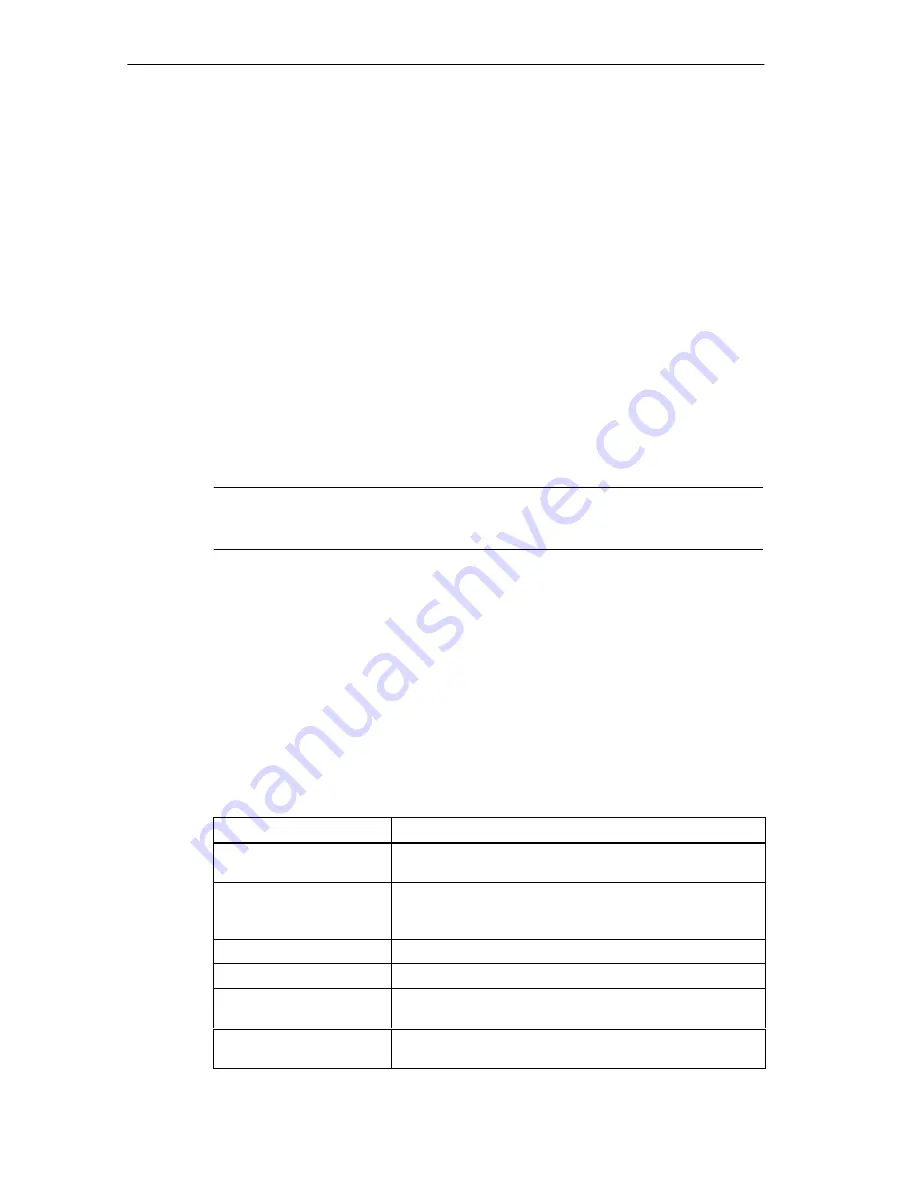
Wiring the S7-400
4-14
S7-400 and M7-400 Programmable Controllers Hardware and Installation
A5E00069481-04
4.9
Grounding
Introduction
Grounding in accordance with regulations and conscientiously implemented is the
prerequisite for proper functioning of a programmable controller.
Each individual component of the S7-400 and of the controlled system must be
properly grounded.
Ground Connections
Low-resistance ground connections reduce the risk of electric shock in the event of
a short-circuit or faults in the system. Moreover, proper grounding (low-impedance
connections: large surface area, wide-area bonding) together with the effective
shielding of lines and devices reduces the effect of interference on the system and
the interference signal emissions.
Note
Always ensure that operating currents do not flow via ground.
Protective Ground
All equipment of Safety Class I and all large metal parts must be connected to the
protective ground. This is essential to ensure that the user of the installation is
reliably protected from electric shock.
Furthermore, this serves to discharge interference transferred via external power
supply cables, signal cables, or cables to I/O devices.
Shown in Table 4-2 are the grounding methods required for the individual
components.
Table 4-2
Methods of Protective Grounding
Device
Grounding Method
Cabinet/frame
Connection to central ground point, e.g. ground bus, via
cable with protective conductor quality
Racks
Connection to central ground point via cable with
10 mm
2
min. cross-section, when racks are not installed in a
cabinet and not interconnected via large metal parts
Module
None; automatically grounded via backplane bus when fitted
I/O device
Grounded via power plug
Shields of connecting
cables
Connection to rack or central ground point (avoid ground
loops)
Sensors and actuators
Grounding according to specifications applying to the
system