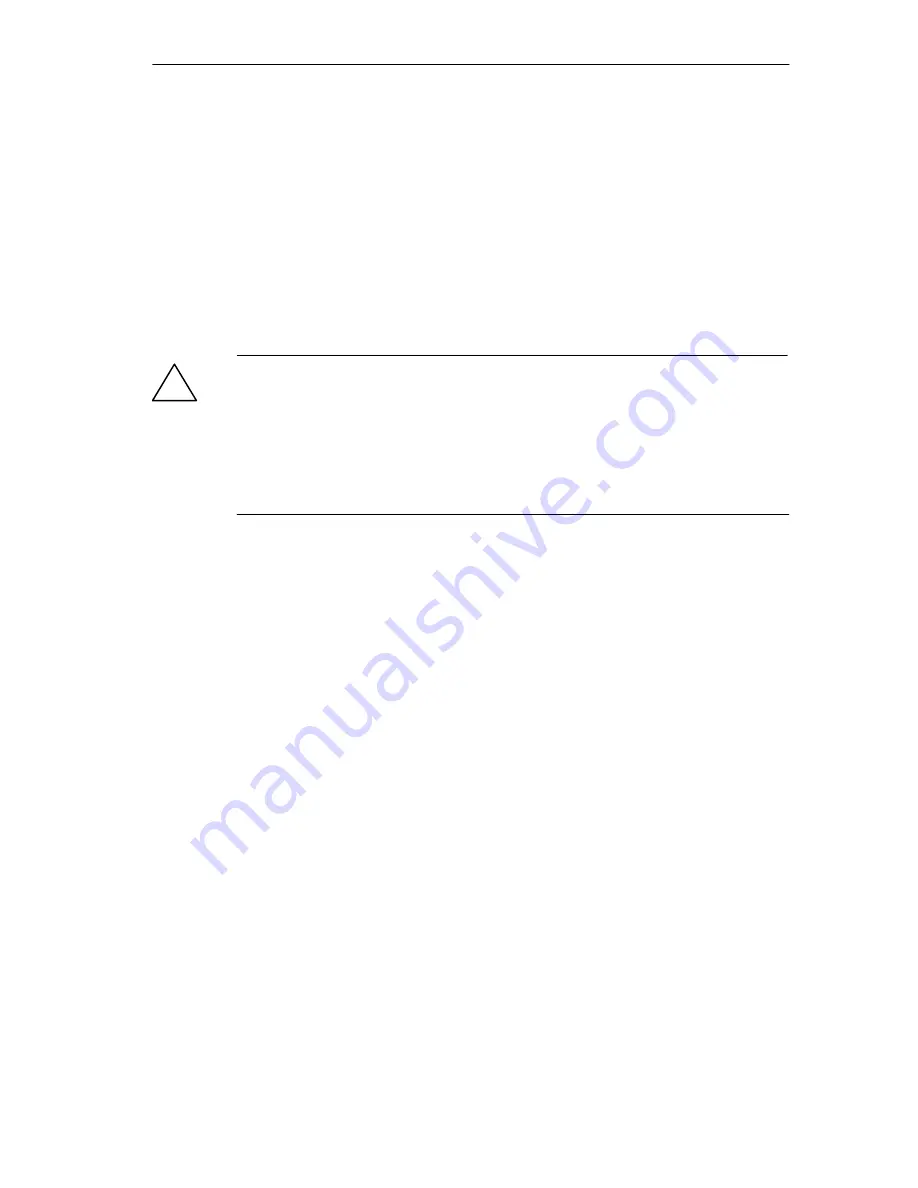
Assembling and Installing Systems
A-15
S7-400 and M7-400 Programmable Controllers Hardware and Installation
A5E00069481-04
A.6
Equipotential Bonding
Potential Differences
Potential differences can occur between separate system components, leading to
high transient currents; for example, if cable shields are fitted on both sides and
grounded at different system components.
Potential differences can be caused by different electrical
supplies.
!
Caution
This can result in damage.
Cable shields are not suitable for equipotential bonding.
Use the prescribed cables exclusively (e.g. those with a 16 mm
2
cross-section).
Ensure also that the cable cross-section is adequate when installing MPI/DP net-
works, since otherwise the interface hardware may be damaged or even des-
troyed.
Equipotential Bonding Conductor
You must reduce the potential differences by laying equipotential bonding
conductors to ensure that the electronic components used function correctly.
Observe the following points for installing an equipotential bonding conductor:
•
The lower the impedance of the equipotential bonding conductor, the higher the
efficiency of the equipotential bonding.
•
Where two sections of an installation are interconnected via shielded signal
lines whose shields are connected to the ground/protective conductor at both
ends, the impedance of the additional equipotential bonding conductor must not
exceed 10% of the shield impedance.
•
The cross-section of an equipotential bonding conductor must be rated for the
maximum circulating current. In practice, equipotential bonding conductors with
a cross-section of 16 mm
2
have proved to be effective.
•
Use equipotential bonding conductors made of copper or zinc-plated steel.
Provide a large-area contact between the cables and the ground/protective
conductor and protect them from corrosion.
•
Lay the equipotential bonding conductor in such a way that the surface between
the conductor and the signal lines is as small as possible. (see Figure A-5).