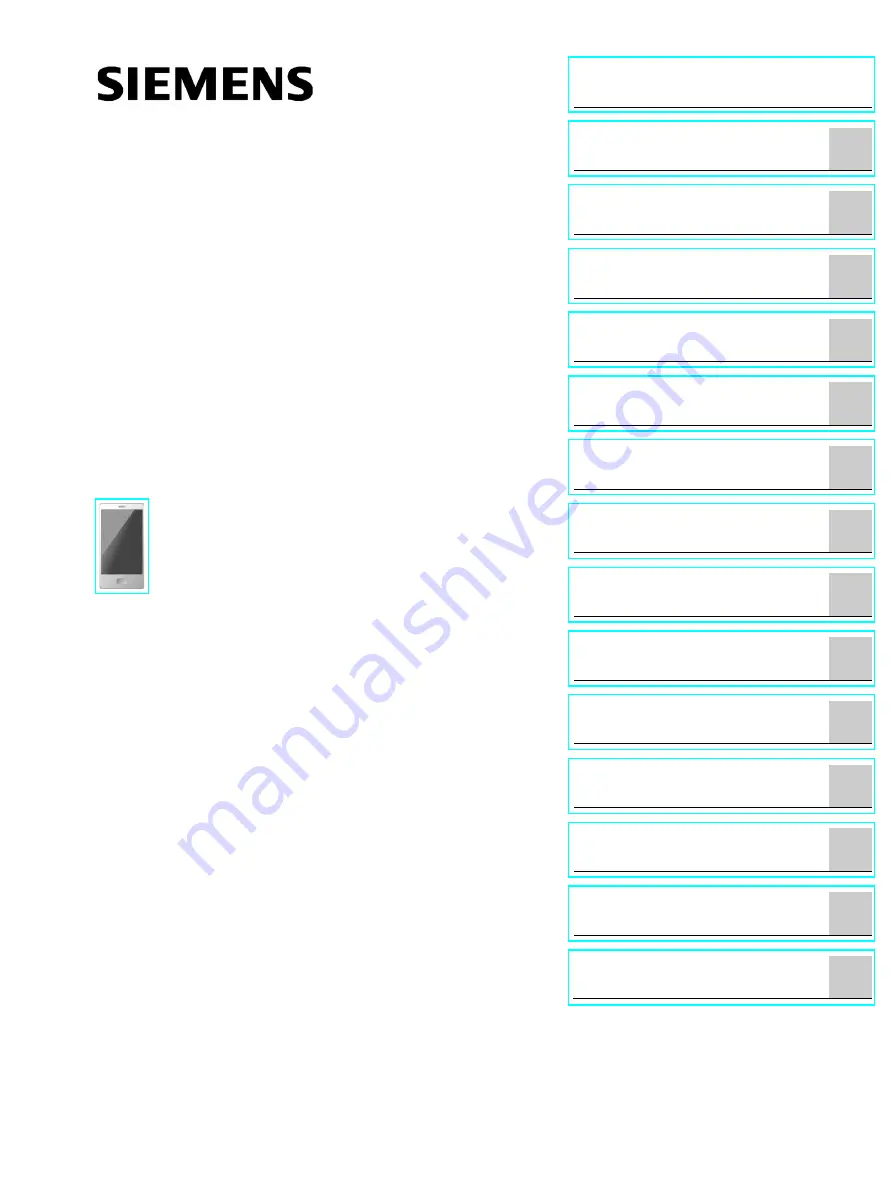
___________________
___________________
___________________
___________________
___________________
___________________
___________________
___________________
___________________
___________________
___________________
___________________
___________________
___________________
___________________
SIMATIC HMI
HMI devices
Mobile Panels 2nd Generation
Operating Instructions
09/2018
A5E33876626-AC