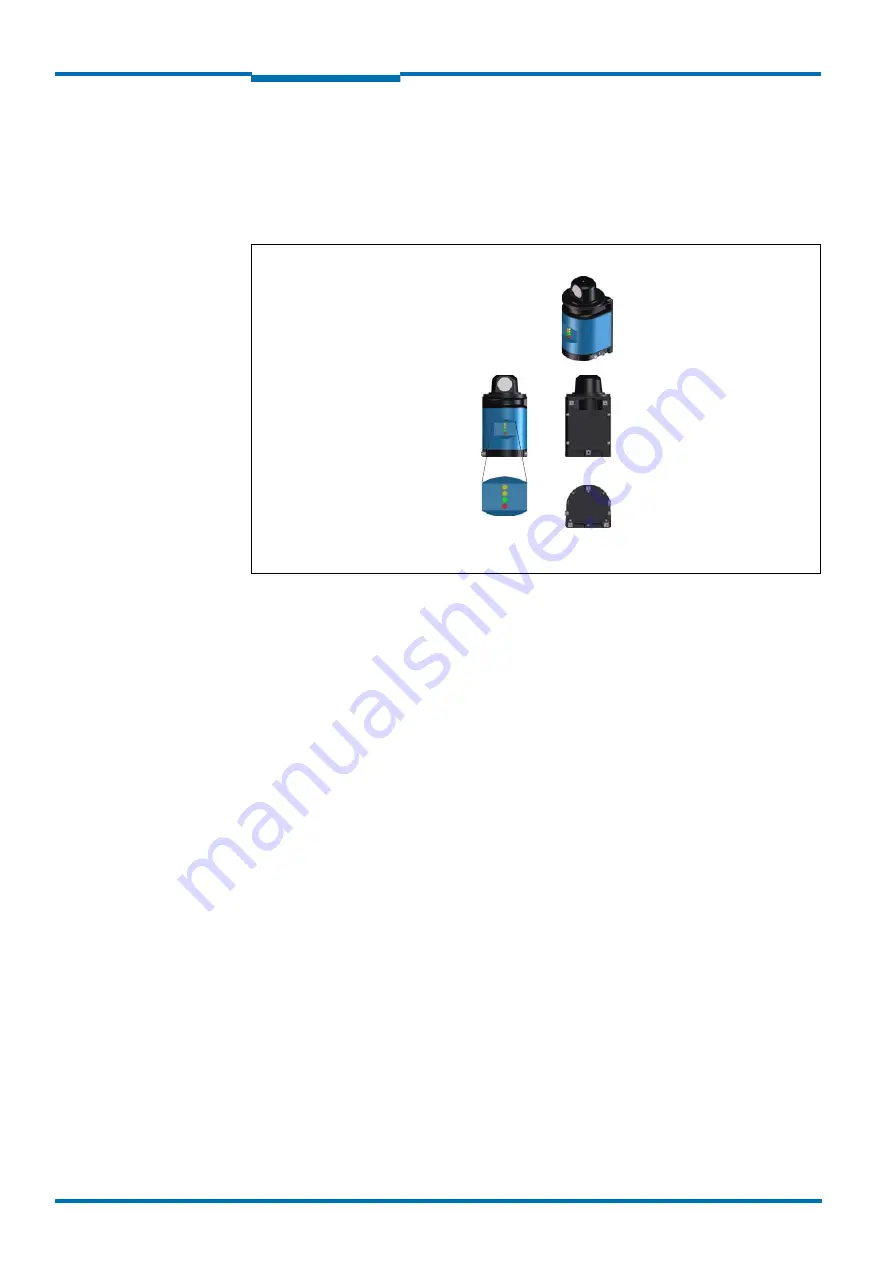
Product description
24
© SICK AG · Germany · All rights reserved · Subject to change without notice
8013889/ZML0/2017-06-09
Operating Instructions
NAV350 Laser positioning sensor
Chapter
3
3.7
Navigation
In the
NAVIGATION
operating mode the NAV350 determines its own current position on the
route during the movement of the AGV. This action is performed based on reflectors posi-
tioned in fixed locations in the surroundings. The detection of three reflectors is sufficient
to determine the position.
Fig. 10:
Determination of the position by the NAV350 by means of the detection of reflector
placements
For position output …
•
an absolute coordinate system with an origin must be defined (as a rule in a corner of
a building, see
section 3.10.4 “Absolute coordinate system” on page 38
).
•
reflectors must be fitted along the route (see
section 3.10.6 “Reflector placements” on
page 40
). These reflector are either measured and their coordinates saved in the
NAV350 or they are taught-in by the NAV350 (mapping).
The NAV350 passes the position data to the AGV’s vehicle computer on request. The vehicle
computer steers the AGV along the programmed and therefore pre-defined route and cor-
rects any course deviations that occur with the aid of the NAV350.
3.7.1
Operating principle of the NAV350 during determining position
During position determination, the NAV350 has three operational statuses:
•
initial positioning
•
continuous positioning
•
Virtual positioning