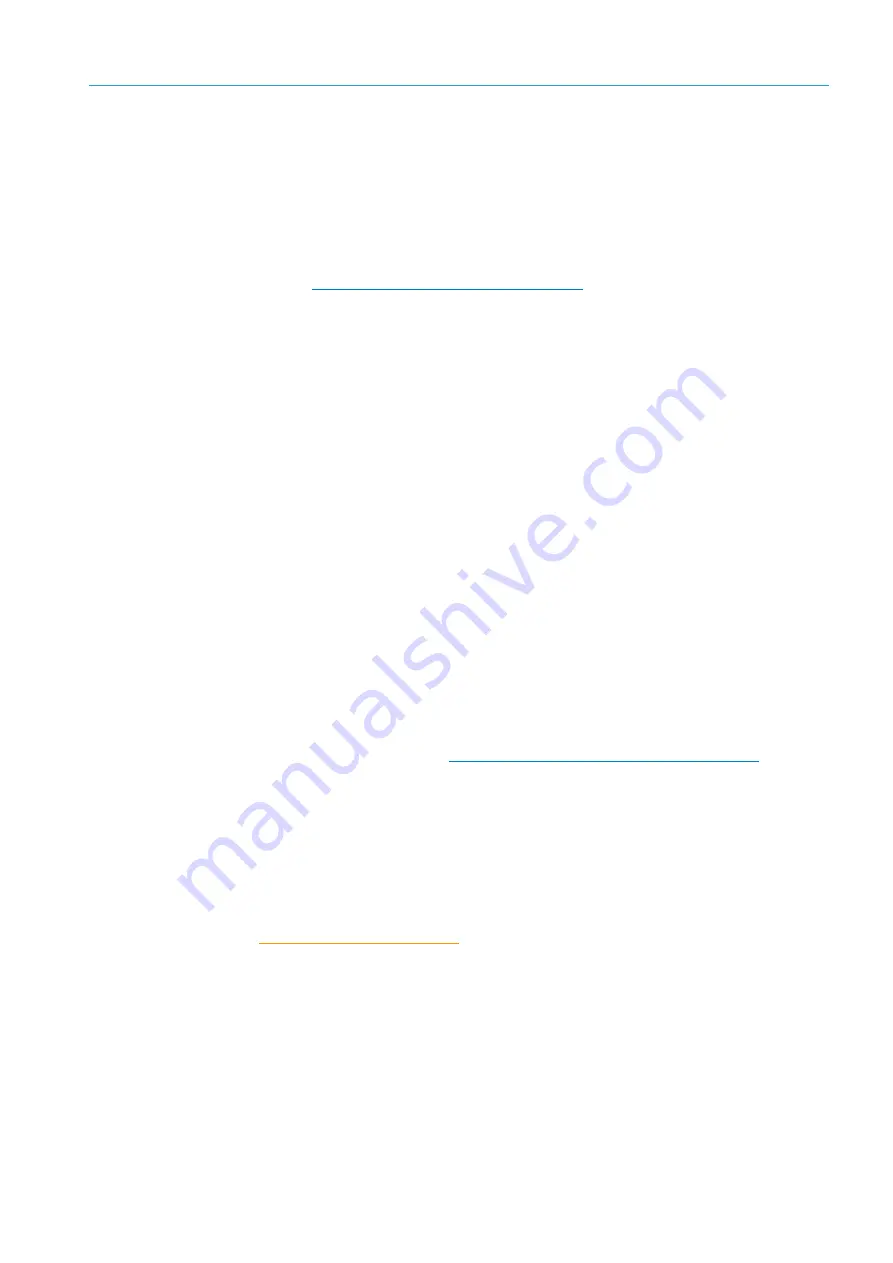
COMMISSIONING AND OPERATION
5
8024534 / / 2019-08-19
Operating Instructions | InspectorP Rack Fine Positioning
25
5.3.10
Completing configuration
After completing configuration, deactivating image output is recommended to achieve
the maximum computing power of the device. This achieves the highest speed in the
positioning process, and the throughput of the system is at its highest.
After successful parameterization using the SICK AppManager, creating a back-up of
the parameterization and saving it on the PC is recommended. Alternatively, the pa-
rameterization can be saved on a microSD memory card in the device via parameter
cloning,
see 4.1.3 “Saving parameter set”, page 15
5.4
Specification of the interface and interaction with the control
5.4.1
Communication process
In practice, we recommend activating the
Continuous measurement
parameter via
the control as soon as the automated storage and retrieval system approaches the tar-
get region and the positioning mark reaches the field of view of the device. As long as
continuous measurement is switched on, the device continuously records images and
evaluates them. The measurement results are transferred to the control cyclically. In
doing so, the device sends offset values of the center point of the positioning mark
compared to the center point of the defined target region to the control. The offset val-
ues are transmitted in micrometers. Determining the average value of the transmitted
offset values in the control and positioning the automated storage and retrieval sys-
tem according to this average value is recommended.
In order to switch between Single and Double deep modes, the control must report
which rack depth is to be approached by means of a command.
If the position of the device and the defined target region do not agree with the posi-
tioning mark on a rack in individual cases, take into account this deviation on the side
of the control. Do not reparameterize the device for this purpose.
5.4.2
Interfaces
The device offers an Ethernet interface with various communication protocols
(PROFINET, TCP/IP, UDP). The communication protocol used can be set using the
SOPASair operating software,
see 5.3.8 Setting up Ethernet interface, page 24.
In addition, the digital inputs and digital outputs can be used for communication with
the control.
PROFINET
If the PROFINET communication protocol is used, communication is done in Hand-
shake mode via the 32 input bytes or 32 output bytes. The control bytes (Ctrl bits) of
the PROFINET interface are not used.
Use the GSD file of the InspectorP63x. The GSD file can be downloaded at
Downloads
tab in the
Software
area.
The following SICK function blocks are recommended for receiving the measurement
results and transmitting the command:
•
S7 function block S7-1200/1500 TIA (hand-held / non-SOPAS devices, PROFIBUS,
PROFINET)
•
S7 function block S7-300/400 step 7 V5.5 (hand-held, non-SOPAS devices, PROFI-
BUS, PROFINET)