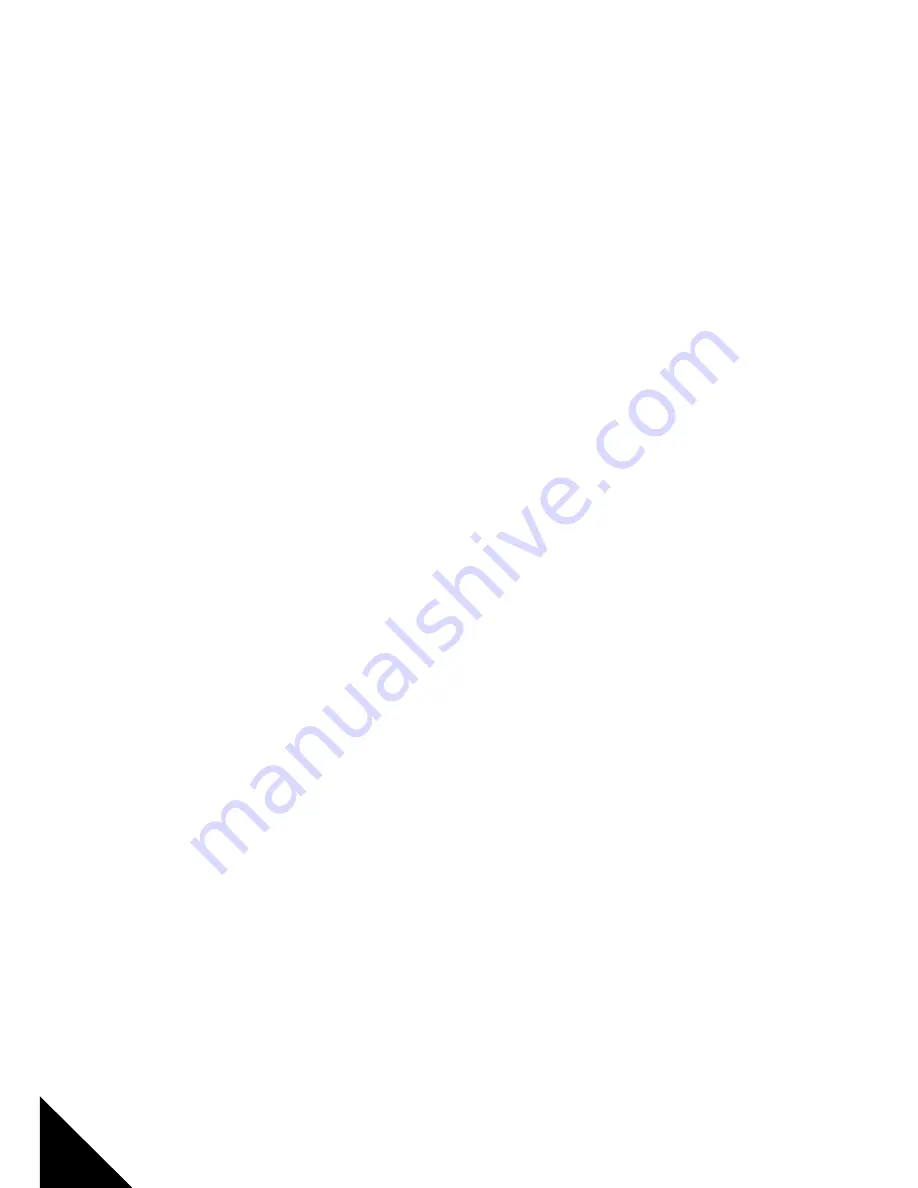
30
Before you start any cycle of calibration, you should “parking” the second extruder on the left side of
the printer and set it with the provided magnet. Automatic calibration cycles are designed to access
all calibration screws with a single extruder.
Manual Calibration
This operation should be carried out with the tip of the nozzle clean, residue-free material. For clean-
ing of the nozzle there refer to Chapter 10.
Manual calibration is intended to make a macroscopic adjustment of floor with a sheet of paper that
should be positioned between the floor and the extruder.
When you enable this function, the plan is to “0” theoretical level and the extruder is positioned se-
quentially in the four corners of the press. Adjust the Allen screw clockwise to lower or counterclock-
wise to raise plan. Make sure that the sheet of paper (for example a bit clipped from an A4 sheet by la-
ser printer) you stick with struggling between the glass plate and the extruder. Repeat the operation
by pressing the knob to move the extruder on the next corner and remember that each adjustment
on a corner effect, although slightly, on the other.
When the regulations will be ultimate extruder tip must brush against the print plan in all respects,
without ever touching it.
Automatic Calibration
Automatic calibration prints rectangles made with one layer on top, allowing you to assess the adhe-
sion of the material to the press and to figure out if the plan is leveled properly observing the extru-
sion width must be equal at all points of the perimeter. A tight stretch indicates a greater distance
between press and extruder plan (too low), while a sudden large discolored motto indicates a plane
too high. Going to touch the tip of the screwdriver wrench strokes closer, you’ll notice that is a depar-
ture from the press: this is a further sign of a flat area that is too low.
This procedure provides an input into the function, and then with one click starts the warm-up and
zeroing of the various coordinates; When the extruder is 230° starts the first rectangle. Considering
the result you can intervene on the four screws at the corners and, after the adjustments, press on
the knob to verify the result through the tracking of a second rectangle. After this round of tinkering,
the machine draws a cross in the center of the rectangle to test the result.
Regulating final leg of axis Z
There is also, for subsequent regulations that require only a rapprochement or removal of the nozzle,
the ability to adjust the Z limit, running ahead or by delaying it. To adjust the limit switch interven-
tion Z let’s turn the black knob on bottom of machine (see picture); clockwise increase the distance
plate-nozzle going to decrease the total travel of Z, while turning it counterclockwise decrease the
distance plate-nozzle, lengthening the total travel of Z.
Summary of Contents for Next Generation
Page 1: ......
Page 2: ......
Page 3: ...SHAREBOT Next Generation USER S MANUAL...
Page 4: ......
Page 10: ...10...
Page 14: ...14 1 SD Card entry...
Page 15: ...15 1 Power cable socket 2 Power switch 3 Label with Identification Code 1 2 3...
Page 18: ...18...
Page 66: ...Sharebot S r l Via Montello 18 23895 Nibionno LC info sharebot it...