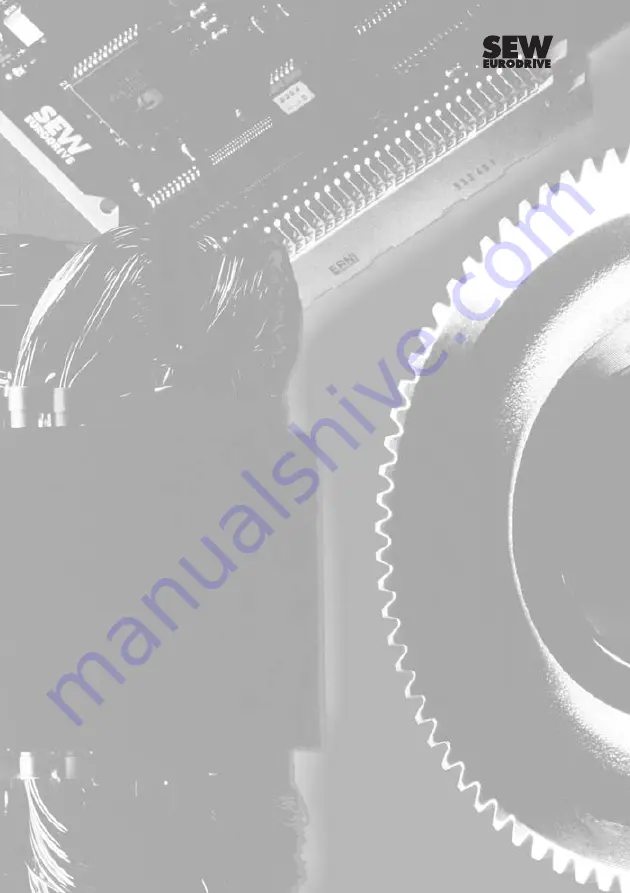
SEW-EURODRIVE GmbH & Co · P.O. Box 3023 · D-76642 Bruchsal/Germany · Phone +49-7251-75-0
Fax +49-7251-75-1970 · http://www.sew-eurodrive.com · [email protected]
Summary of Contents for INTERBUS UFI11A
Page 1: ...INTERBUS UFI11A Fieldbus Interface Edition 06 2002 Manual 1052 5114 EN ...
Page 2: ......
Page 65: ......
Page 66: ......
Page 67: ......