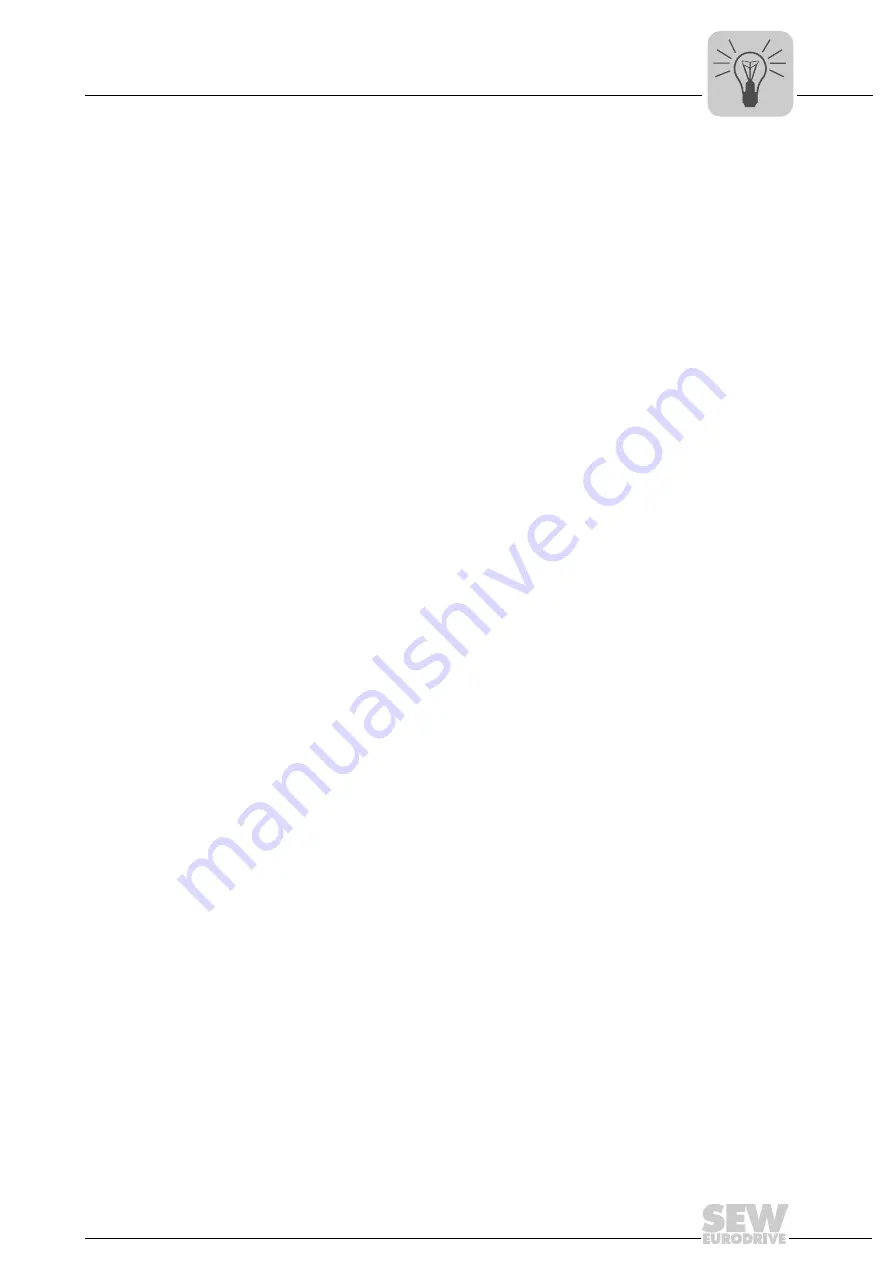
Manual – MOVI-PLC® advanced DHF41B DeviceNet and PROFIBUS DP-V1 Fieldbus Interfaces
49
7
Diagnostic procedures
Error Diagnostics for Operation on the DeviceNet Fieldbus
Step 3: Fault diagnostics
When DHF41B is in status "Connected" or "Module error", the data exchange between
master (scanner) and slave (DHF41B) is active. If it is still not possible to transmit data
to the IEC application of the MOVI-PLC
®
advanced
DHF41B via DeviceNet, the
following steps should help you to diagnose the error.
A Are the correct values for the process data words displayed in the PLC Editor?
If yes, continue with F.
B Is bit 0 in DeviceNet control register of the PLC set to "1" to activate process data
exchange?
C Are the process data words copied to the right offset in the Local I/O tag of the
DeviceNet scanner? Check the tags and scanner mapping.
D Is the PLC in RUN mode or does active forcing overwrite the transfer of the normal
process data words?
E If the PLC does not transmit data to DHF41B, refer to the documentation of the PLC
manufacturer for support.
F Are the process data words being used correctly in the IEC program?
G Was the communication interface configured and activated properly in the IEC
application using the MC_DeviceNetPDConfig function block (see chapter "Settings
in MOVI-PLC
®
advanced
DHF41B")?
H If the cycle time for exchanging process data is longer than expected, calculate the
bus load.
Example:
64 process data words from and to a DeviceNet slave are transmitted in ca. 11 ms
at a baud rate of 500 kBaud. When operating 2 units with 64 process data words
each, the shortest possible cycle time is about twice as long: ca. 22 ms. Halving the
baud rate means doubling the cycle time.
Summary of Contents for DHF41B
Page 2: ...SEW EURODRIVE Driving the world ...
Page 123: ...SEW EURODRIVE Driving the world ...