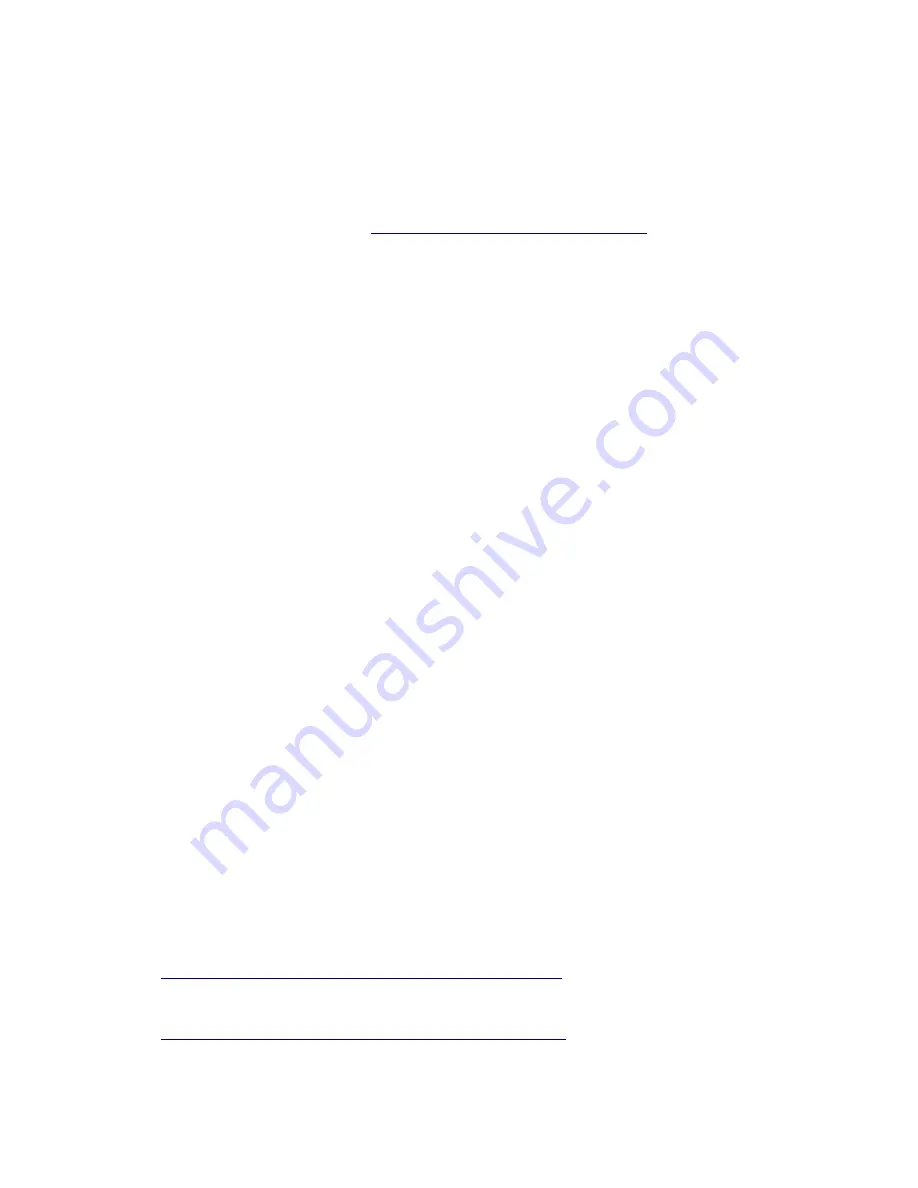
Using a focused air flow, lower air flow and the step up technique I just described, you
won't see a significant drop in hot end temperature and you won't see a tell tale sign on the part
that the user 'Polygonhell' mentions. PLA has this interesting property that if you change the
extrusion temp at the hot end, it has a visible effect on surface sheen of the part from matte to
gloss as you raise the temperature.
RichRap has written an excellent post
about how he uses
this phenomenon when printing decorative vases. Although he was varying the hotend
temperature, a similar effect can occur with improper air cooling.
I'm also an advocate of using off-platform cooling. By this I mean strategically placed
(ducted) fans that direct air to problematic areas of a print. These can be mounted to your
vertical columns or simply sat on the bed if it is not too hot. With ducting, you can reduce the air
flow considerably and keep the cooling right on a "hot spot". This technique does require
manual adjustment, repositioning, etc. But, it you are trying to print a really tricky part, it might
be the only way to do it. Frankly, the part cooling capabilities of desktop 3D printers is extremely
primitive at this point. It's fine for the majority of objects you might print but as we push the
envelope on what's possible, part cooling is one area that needs some more work to automate
it.
Consider this, the way I maintain very tight tolerances on the rotating spindle and hub
assemblies on my fly fishing reels is to use a low beam of air cooling on the spindle as it's
printed. This "locks" the filament in place in a very predictable way. Once I printed a few parts
and measured them to make sure there was little variation, I incorporated that into the design to
get exactly the tolerance these parts required.
Calibration things:
This first set is a 20mm diameter cylinder, 0.6mm tall. There are 3 variations and the all
width is the first part pf the STL file name. Start with the pt4mmx20mm-cylinder.stl if you have
0.4mm nozzle orifice. You can use these to:
1) get first layer adhesion to the bed
2) first layer thickness (stop the print after first layer and measure it)
3) total print height (should be about .6mm)
4) X-Y calibration (should be 20mm diameter)
5) eliminate blobbing and other surface artifacts - follow the guide above, print slow,
adjust retracts, etc. KEEP NOTES!
pt3mmx20mm-cylinder.stl
http://forum.seemecnc.com/download/file.php?id=8207
pt4mmx20mm-cylinder.stl
http://forum.seemecnc.com/download/file.php?id=8208
42