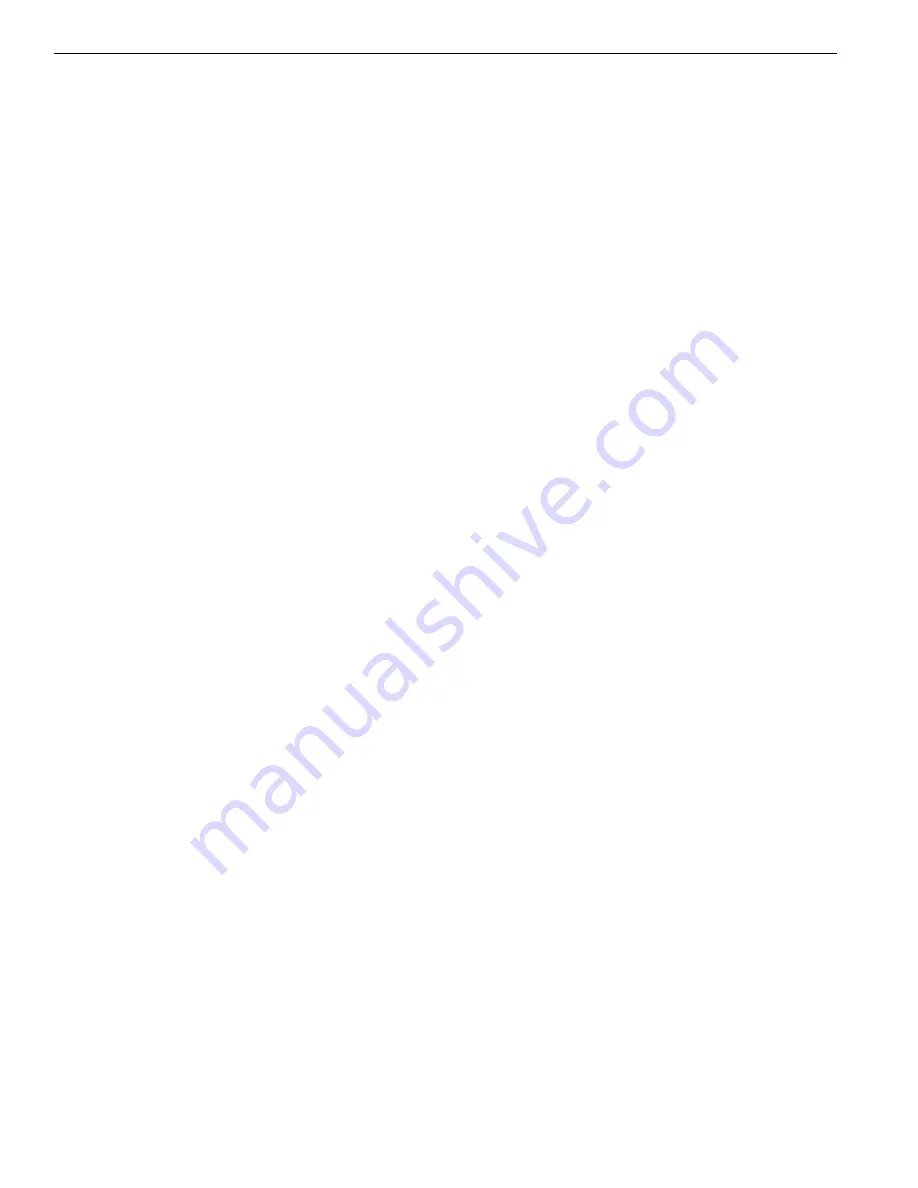
Description: The Three Phase Electric Motor requires all three power lines (all three phases) to be operative
else it will “single phase” causing extensive damage to the motor’s internal windings. Low voltage will also
a.
cause the same symptom. Low voltage is caused by an undersized power supply or generator, undersized
power lead wires to the System or motor, loose power wire, or connection at the motor or within the power
supply line, and “burnt” contacts on the motor starter relay (contactor).
b. Solutions:
a. Check wiring size and connections to, from, and in between the Power Supply and the electric motor.
Correct wire size or any loose wires.
b. Measure voltage at the motor during attempt to start it. If voltage drops more than 10% locate and correct
the reason.
c. Check the motor starter relay (contactor) for “burnt” contacts.
d. Ensure all three phases have power.
3. Problem: The Electric Motor makes an unusual “grinding” sound when operated.
a. Solutions:
a. Check to see if the fan is rubbing against the fan guard.
b. Replace motor, as required.
4. Problem: The High Pressure Pump makes an unusual “grinding” sound when operated.
a. Description: The pump will make a grinding noise if its drive shaft has been forced into the pump body. The
Electric Motor and Pump are coupled with a “Flex Coupler” specially designed for use with this specialized
pump. Never replace the Flex Coupler with another make or style. ALWAYS leave 3/32 in. (2mm) spacing
between the two mating Flex Couplers. ALWAYS ensure that the Safety Bell Housing attached to the electric
motor and the pump seats evenly on both ends. Internal spacing of moving components within the High
Pressure Pump hold to very tight tolerance. Any debris larger than 10 micron entering the High Pressure
Pump will cause abrasion to the pump’s internal parts, and will cause an audible grinding noise. Hard debris,
such as sand or metal, will cause the pump to “freeze up” and will cause extensive damage to the internal
parts of the pump. If the System incorporates a Multi Media Filter use caution to not allow sand to enter the
High Pressure Pump. When changing Prefilter Elements use caution to not allow debris to enter the High
Pressure Pump. Damage to the High pressure Pump caused by debris is the responsibility of the person
performing maintenance to the System, is the liability of the person performing maintenance to the System,
and is not covered by the Sea Recovery warranty.
b. Solutions:
a. Check spacing between the motor’s and pump’s flex coupler. Spacing must be minimum 3/32 in. (2mm)
and maximum 1/8 in. (3mm).
b. Check Safety Bell Housing to ensure it is flush and secured to both the motor and pump.
c. Check Pump for signs of foreign debris entering the inlet.
5. Problem: Decreased Pressure
a. Description: The High Pressure Pump flow and or pressure have decreased from normal. As with all High
Pressure Pumps, over time of operation flow and pressure will decline due to internal wear. Under normal
use and care no significant pressure or flow loss will occur for 8,000 hours of operation or longer. Do not
confuse low feed water flow and low feed water pressure with a High Pressure Pump problem. All positive
displacement pumps must receive a specific flow at a minimum pressure else cavitation will occur. Check
to ensure that the Booster Pump is delivering at least 4.5 U.S. Gallons (17 Liters) Per Minute of feed water
at 10 to 40 PSI (69 to 276 kPa) at the Inlet of the High Pressure Pump. Note: Systems operating on 50 Hz
power will deliver 3.75 U.S. Gallons (14.2 Liters) Per Minute of feed water.
b. Solution: If Feed Water Flow and Pressure into the High Pressure Pump are within minimum specifications,
and if the electric motor is rotating at the proper rotation (the proper cycles are present from the power
source) yet the High Pressure Pump has lost Flow and or Pressure then return the High Pressure Pump to
Sea Recovery for servicing.
Aqua Matic Compact 450-1800
118
Summary of Contents for SRC Aqua Matic 1400-2
Page 2: ......
Page 3: ...Aqua Matic Compact 450 1800 Owner s Manual Manual PN B651140001 ...
Page 4: ......
Page 12: ......
Page 30: ......
Page 47: ...Commissioning 45 ...
Page 48: ......
Page 49: ...47 ...
Page 64: ......
Page 67: ...65 Commissioning ...
Page 68: ......
Page 75: ...73 ...
Page 96: ......
Page 125: ...123 ...
Page 134: ......
Page 137: ...Chapter 10 Appendix 135 ...
Page 138: ......
Page 139: ......
Page 140: ......
Page 142: ......
Page 143: ...Single Phase Electrical Motor Wiring 141 Appendix ...
Page 144: ...Three Phase Electrical Motor Wiring Aqua Matic Compact 450 1800 142 ...
Page 145: ...Three Phase Transformer Wiring 143 Appendix ...
Page 146: ...New System Initial Readings Form Aqua Matic Compact 450 1800 144 ...
Page 147: ...Daily System Readings 145 Appendix ...
Page 148: ......
Page 149: ...Chapter 11 Exploded Parts Views 147 ...
Page 150: ...Pre Installation Matrix Drawings Aqua Matic Compact 450 1800 148 ...
Page 170: ...Aqua Matic Compact 450 1800 168 ...
Page 175: ...2 8 11 5 10 7 9 3 16 4 15 6 14 13 12 17 22 21 20 19 19 18 24 23 173 ...
Page 177: ...2 8 11 5 10 7 9 3 6 4 15 12 13 14 19 18 23 24 21 20 17 16 22 175 ...
Page 179: ...2 4 3 19 15 11 12 9 10 8 14 17 16 10 13 5 6 18 7 21 20 177 ...
Page 181: ...21 3 2 18 14 10 11 7 16 15 9 12 4 5 17 20 19 8 6 13 179 ...
Page 183: ...2 4 3 18 14 21 11 9 10 8 13 16 15 10 12 5 6 17 7 20 19 181 ...
Page 185: ...9 16 3 7 4 5 2 13 12 14 15 17 28 27 19 11 10 6 25 26 23 1 29 8 24 183 ...
Page 187: ...9 15 3 7 4 5 2 13 12 14 26 25 17 11 10 6 23 24 21 1 27 8 22 185 ...
Page 189: ...9 15 3 7 4 5 2 13 12 14 26 25 17 11 10 6 23 24 21 1 27 8 22 187 ...
Page 191: ...25 23 24 9 16 8 22 20 19 3 28 17 14 12 1 2 7 30 11 10 6 21 29 26 13 4 5 18 27 189 ...
Page 193: ...23 21 22 9 15 8 20 18 17 3 26 14 12 1 2 7 28 11 10 6 19 27 24 13 4 5 16 25 191 ...
Page 195: ...23 21 22 9 15 8 20 18 17 3 26 14 12 1 2 7 28 11 10 6 19 27 24 13 4 5 16 25 193 ...
Page 212: ......
Page 213: ...Chapter 12 Electrical Diagrams Foldouts 211 ...
Page 216: ......
Page 218: ......
Page 219: ......
Page 220: ......
Page 221: ......
Page 222: ......