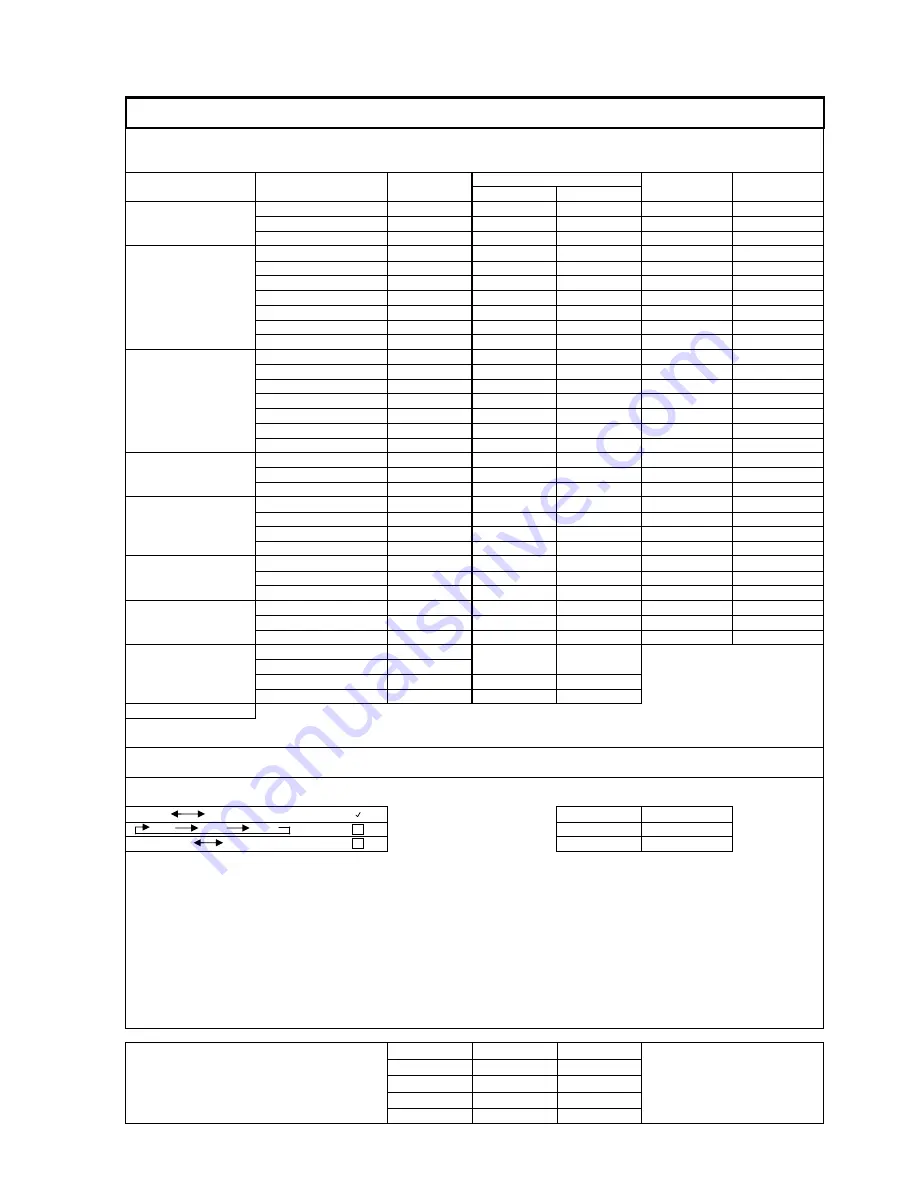
D-6
P
e
e
CYCLE 6: PROCESS NO DRYING
STEP
STEP
STEP
TEMPERATURE (°C)
WATER
DRAIN/HOLD
DESCRIPTION
STAGE
TIME (sec)
(1)
HEATING SP
GUARANTEE S
SUPPLY
PRESET
PREWASH
Fill
Cold
Washing
60
0
0
Drain
Drain
WASH-1
Fill
House Hot
Chem-1 Inject
15
Chem-1 Wash
180
60
0
Soaking
0
Neut-1 Inject
0
Neut-1 Circulation
0
Drain
Drain
WASH-2
Fill
House Hot
Chem-2 Inject
0
Chem-2 Wash
0
60
0
Soaking
0
Neut-2 Inject
0
Neut-2 Circulation
0
Drain
Drain
RINSE 1
Fill
House Hot
Washing
60
71
0
Drain
Drain
RINSE 2
Fill
House Hot
Rinse Aid Inject
(2)
15
Washing
180
87
83
Drain
Drain
RINSE 3
Fill
House Hot
Washing
0
0
0
Drain
Drain
RINSE 4
Fill
House Hot
Washing
0
0
0
Drain
Drain
EXHAUST
POV exhaust
0
-
-
Devaporizing
60
-
-
Drying - Steam
900
(3)
85
57
Cool Down
20
(4)
60
-
> cycle end <
Aqua-Pulse Settings:
SPRAY PATTERN:
SPRAY TIMES (sec):
RH LH
Right Hand Puls
10
RH LH Q/L
Left Hand Pulser
10
RH+Q/L LH+Q/L
Quick-Lock Puls
10
(1)
To disable STAGE or STEP enter '0' for time setting
(2)
Rinse Aid will be injected on the last rinse of the cycle
(3)
Duration after the drying temperature has reached to TEMPERATURE GUARANTEE S.P. setting
(4)
Duration after the drying temperature has fallen bellow HEATING S.P. setting
Scientek
Revision:
Date:
Name:
WASHER CONTROL SYSTEM
0
0
00-Jan-00
0
0
0
0
SW 6000 Series, Cart & Utensil Washer
Technology Corporation
0
0
0
PROGRAM CHARTS
0
0
A
Oct 01, 2007
D. Pekic
JOB #: Standard