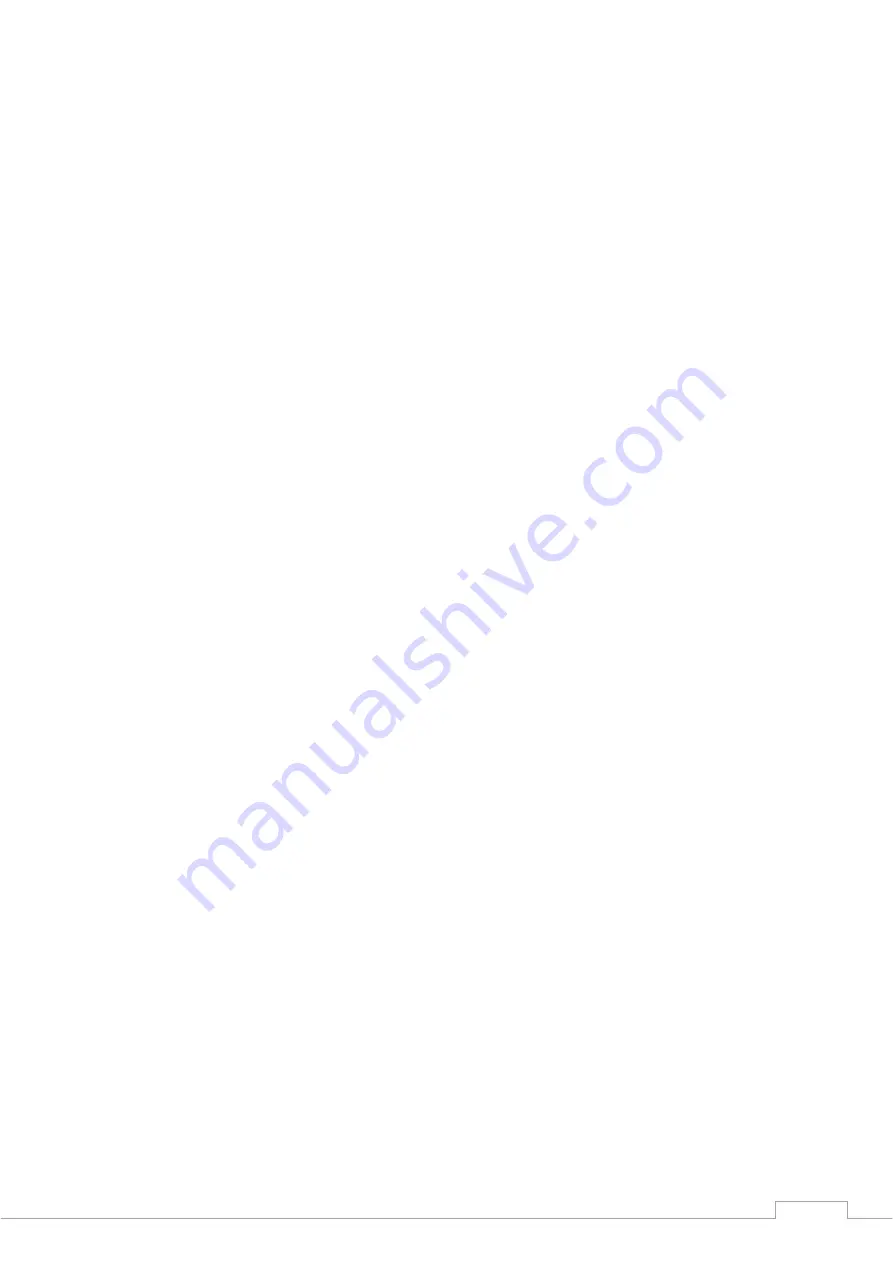
6
grateless, self-cleaning furnace in the from on the cast iron retort of goblet
shape
fan blowing the air into the chamber – retort
electronic temperature controller.
The fuel for combustion process is transported by means of a screw feeder from the
fuel hopper placed by the side of boiler.
All processes leading to fuel combustion together with the air delivered by blow-in
fan take place in the iron cast retort. Above the coal burner an iron cast deflector in
placed. The deflector radiator plate deflecting heat radiation onto a glow in order to
make combustible gases be burner completely and distribute fumes into the heat
exchanger uniformly. The cinder which has been formed in the final phase of
combustion process in moving towards the rim of the retort, and then drop down into
an ash pan chamber. For easier maintenance the chamber is provided with a drawer
pullout type.
Due to its efficiency, the combustion chamber burns such a quantity of fuel, which is
necessary to obtain the temperature set on the controller. The controller constantly
measures the temperature of water boiler. Depending on the results, it controls fuel
feeder and ventilator. At the same time the controller operates a circulation pump
(provided a heating installation is equipped with such pump). Detailed design,
functioning and operation description of the controller is attached to this controller
manual.
The boiler’s advantage, is a simple operation relaying on periodic coal bunker
refueling (the fuel bunker) and cinder removing from the ash drawer with no
requirement to stop the boiler. Once boiler is fired up, it does not call for further
service, and its operation may be practically continuous in the entire heating season.
Boiler may be also use beyond heating season in the configuration with hot utility
water boiler.
Tree- duct gas channel construction renders full utilization of gasses heat. In addition,
the upper part of combustion chamber is closed with a water jacket.
Gases are transferred into a chimney trough the smoke conduit situated at the back
of a boiler. The smoke conduit is equipped with smoke throttle, with in case in to high
chimney draught allows for its throttling. On the smoke conduit sidewall there is
washout whole. Combustion chamber door, and ash box door are placed on the
boiler’s front. For periodic cleaning operations and also for firing up a boiler, the retort
may be accessed through furnance door.
In the upper part of boiler, under the cover, there is a flap of upper washout hole
cover. It renders easy access to perform cleaning operation of the heat exchanger
cassettes. Lateral washout door are used for dust removing if accumulated.
To the upper part of the heat exchanger a hot water connector is welded. To the
lower part of it, on the back wall, a return water connector is welded. Blowdown
connection is placed on the boiler’s lateral wall.
The entire constructions is wrapped with insulation material, a mineral wool, which
fills the space between a head exchanger and boiler’s casing.