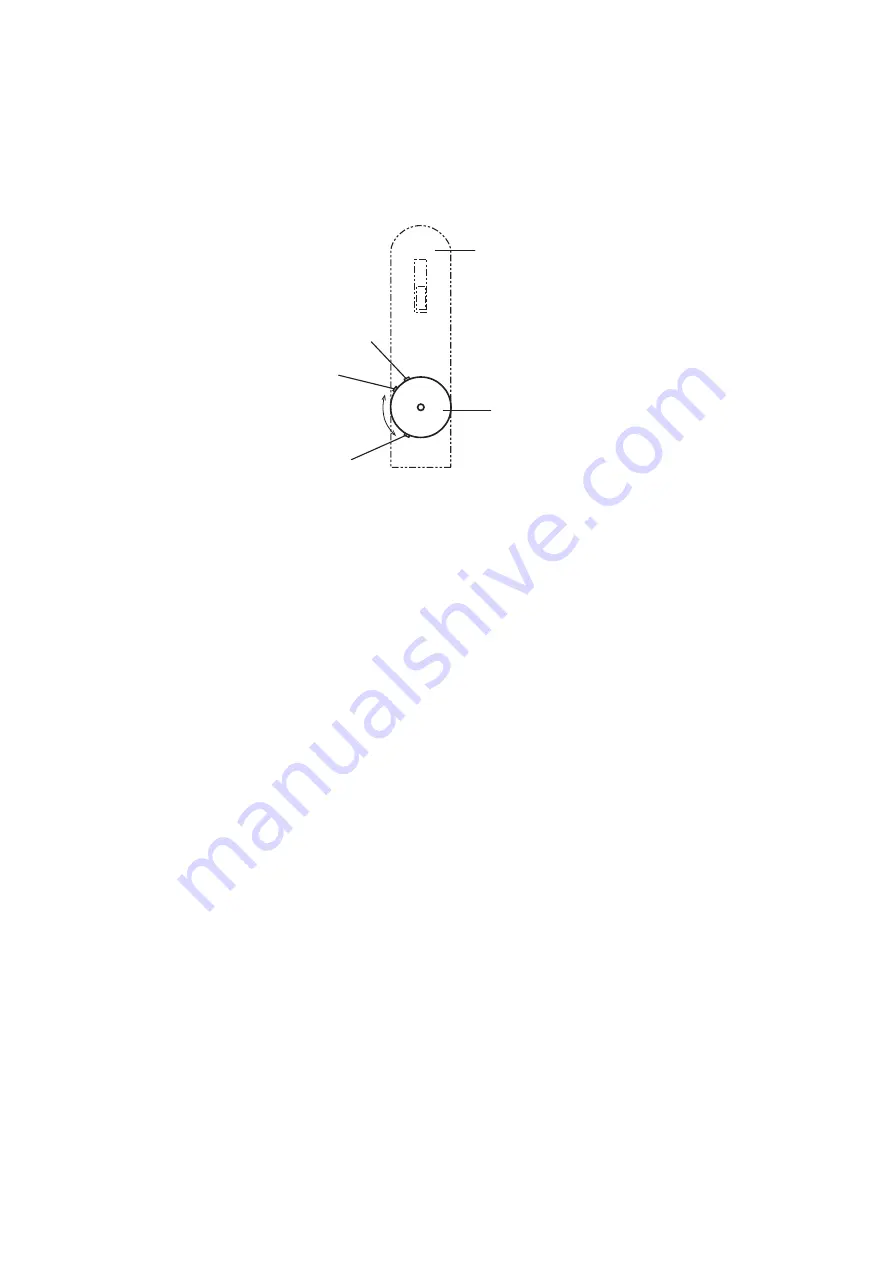
17
Adjust airflow rate by turning the airflow control valve in the range MIN position to
MAX position shown in Figure 9. Turning it over MAX position to STOP position
reduces the airflow rate due to valve structure.
3. HOW TO POLISH A WORK PIECE WITH THE FLEXIBLE POLISHING PAD
When the polisher rotation gets stable after the start, begin the polishing operation, Put
the flexible polishing pad slowly on the face to be polished when it comes in touch with
a work piece. Too much force to the pad would damage the work piece and cause
quick worn-out of the pad, and would not be an efficient polishing.
The efficient polishing depends on many elements, characteristics of work piece, the
flexible polishing pad, pressure between the flexible polishing pad and work piece, water
flow rate, skill of operator and polisher speed.
The operator would have an experience of optimum water flow rate. Contact of polisher
speed is utilized by airflow control value ( see Figure 1, page 6 ) The optimum polishing
speed, therefore, could not be specified in this instruction manual due to too many
elements.
Relation of r/min and compressed air pressure is shown in Figure 5 in page 8. The
operator would have an experience of optimum polisher speed.
4. CAUTIONS IMMEDIATELY AFTER USE
After the polishing operation, turn OFF the switch lever and place the polisher on floor
ensuring that its rotation is completely stopped. Failure to do so could cause accidents.
Inordinate impact to the polisher body could result in tear or crack of the polisher and
the flexible polishing pad. Handle them with good care.
Switch Lever
Stop
Max.
Min.
Airflow Control Valve
Figure 9 Airflow Control Valve
Summary of Contents for PA-2
Page 2: ......