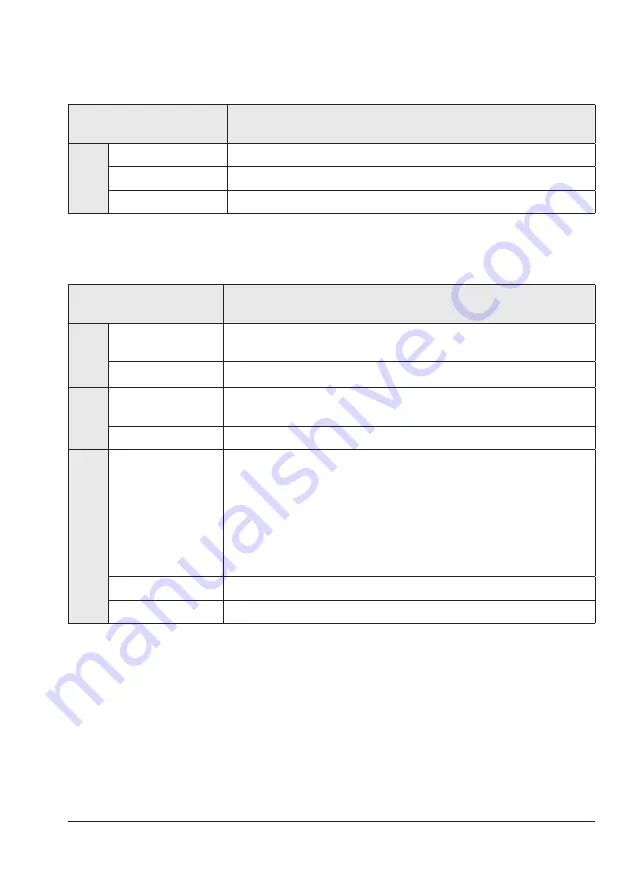
EB 8387-5 EN
99
Appendix
Error codes – Recommended
action
Condensed state message active, when prompted,
Err
appears.
When fault alarms exist, they are displayed here.
78
Option parameters
Error in option parameters.
Status classification
[Maintenance required]
Recommended action Return positioner to SAMSON for repair.
Diagnosis errors
Error codes – Recommended
action
Condensed state message active, when prompted,
Err
appears.
When fault alarms exist, they are displayed here.
79
Extended diagnostics
Messages are generated by the EXPERTplus extended diagnostics
(
u
EB 8389 on EXPERTplus valve diagnostics).
Status classification
Maintenance required (cannot be classified)
80
Diagnostic parame
-
ters
Errors not critical to closed-loop operation.
Status classification
Maintenance required (cannot be classified)
81
Reference test
canceled
Error occurred during plotting the reference graphs for drive signal y
steady-state (
d1
) or drive signal y hysteresis (
d2
)
•
Reference test canceled
•
Reference line for drive signal y steady-state or drive signal y hyster-
esis was not adopted.
Error messages are not yet saved in a non-volatile memory. They cannot
be reset.
Status classification
[Maintenance required]
Recommended action Check and, if necessary, perform a new reference test.
Summary of Contents for 3731-5
Page 71: ...EB 8387 5 EN 71...
Page 102: ...102 EB 8387 5 EN...
Page 103: ...EB 8387 5 EN 103...
Page 104: ...104 EB 8387 5 EN...
Page 105: ...EB 8387 5 EN 105...
Page 106: ...106 EB 8387 5 EN...
Page 107: ...EB 8387 5 EN 107...
Page 110: ...110 EB 8387 5 EN...
Page 111: ...EB 8387 5 EN 111...