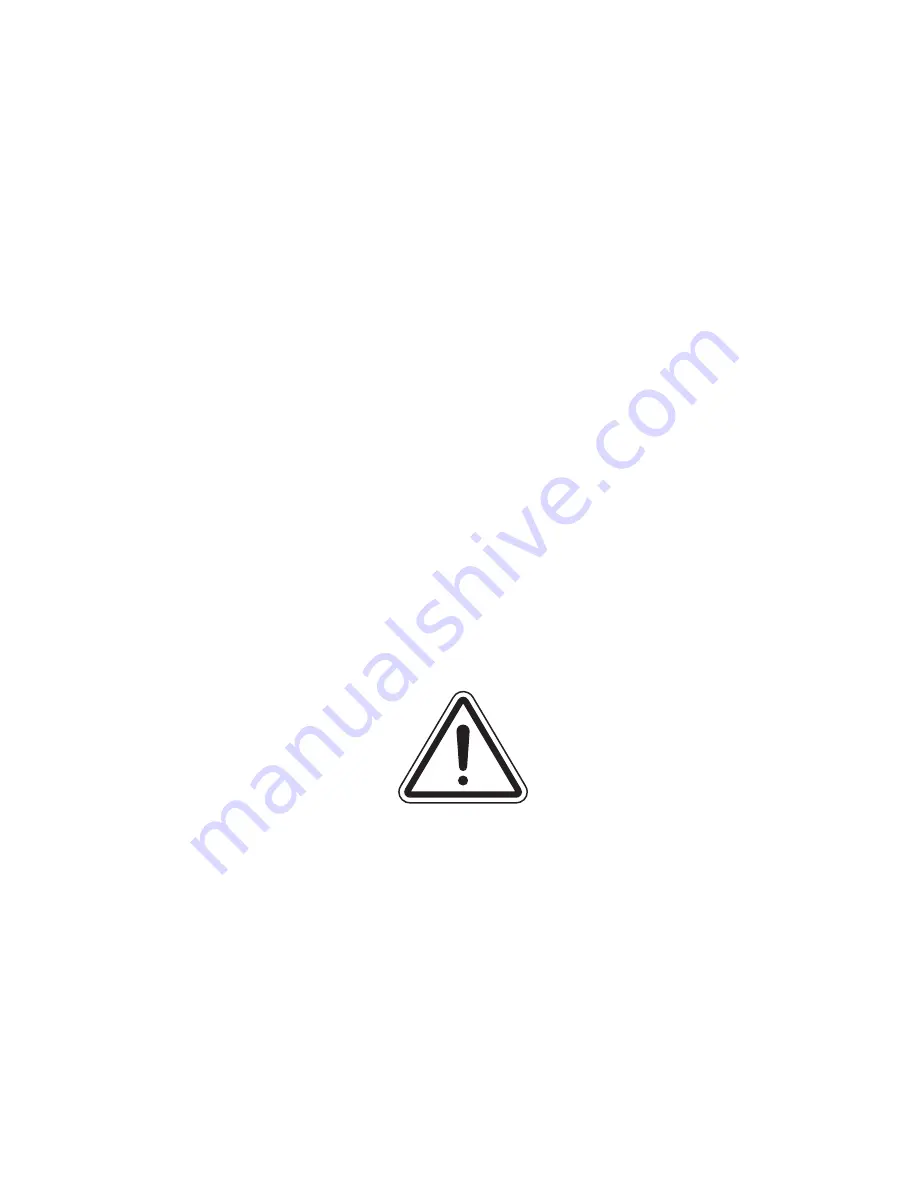
1.
Refrain from wearing loose fitting clothing on or around this piece of machinery. There are
many places that loose clothing may become wrapped or pulled into devices.
2.
Be aware of any moving parts on this machinery. Make sure that any person or persons
on or around this piece of machinery are aware of the dangers as well. There are many
places where injury may occur. Learn about your unit and the dangers of it. Always use
caution in the operation of this piece of machinery.
3.
Be sure that any individuals operating this equipment are trained and are aware of the
dangers of this equipment.
4.
Check for rocks, sticks, or anything that may cause bodily harm to you or damage your
unit.
5.
Never attempt to work on or repair this piece of equipment while it is running. The PTO
and/or any other power source must be completely disengaged while working on this unit.
6.
Those working around this unit should remain at least 100 feet from it while it is in
operation. The fans are able to propel objects at a high speed up to this distance.
7.
Be aware of the dangers of hydraulic systems. Hydraulic fluid is under very high pressure,
and may cause serious injury if it hits the facial area, especially the eyes.
8.
Shut down the entire system before checking hydraulic fluid level or adding fluid to the
system.
Hazards
Safety Instructions
Salford BBI Inc.
Page 11
Endurance Operator Manual 2019 V1
07/23/19