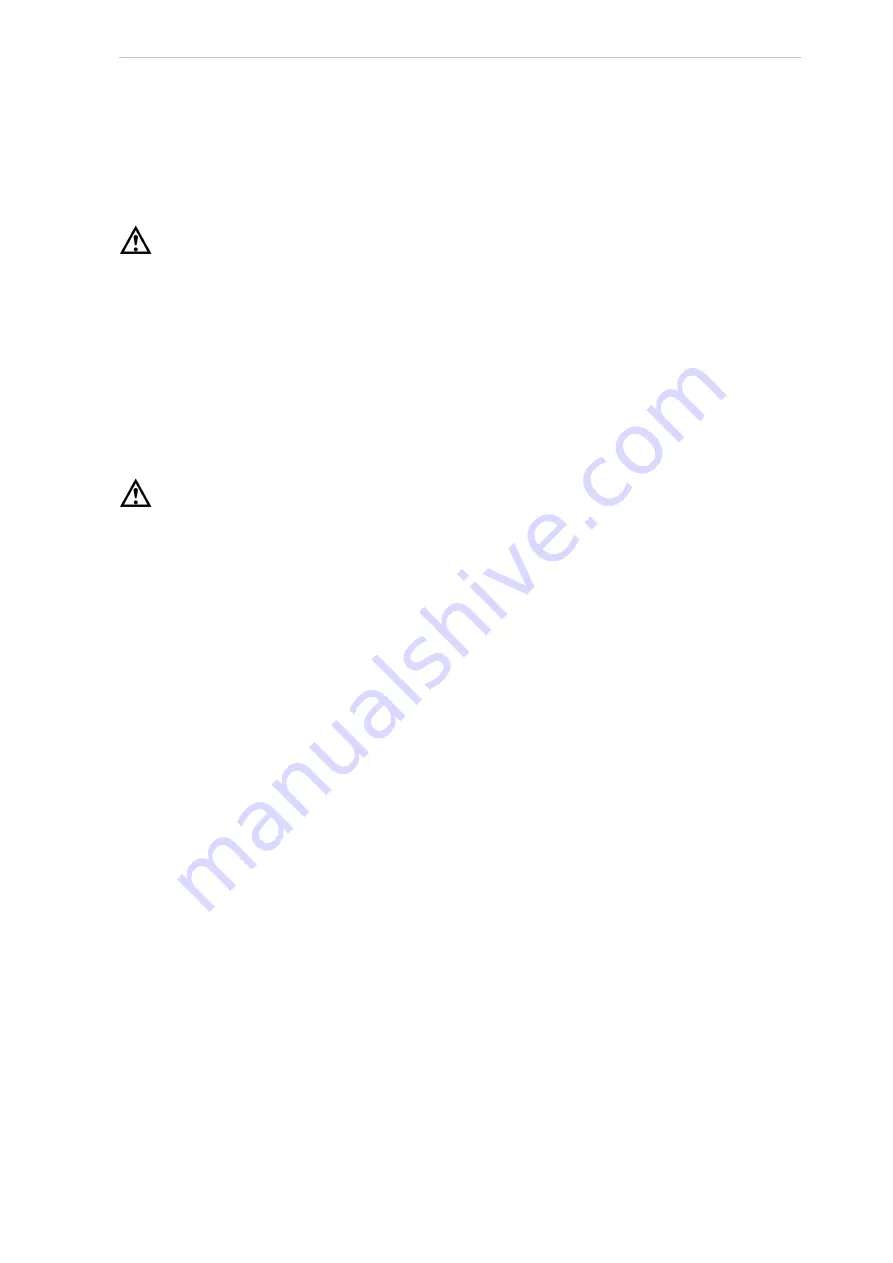
Operating manual - ChillPAC and LP ChillPAC Mk 3
54/68
010823 en 2021.06
7. Final disposal
7.1
Safety precautions
Danger!
Before dismantling the plant, read the safety precautions carefully.
Dismantling a refrigeration unit to be scrapped must be carried out safely.
Only competent refrigeration personnel must perform the dismantling as fundamental knowledge of re-
frigeration systems and the risks involved are required.
Before dismantling the unit, refrigerant and oil must be drained into suitable containers. Disconnect all
electrical connections to the unit and remove fuses in the main switchboard.
During the dismantling process, the individual machine parts and components must be sorted to ensure
proper disposal. Hazardous waste must be handled at a site complying with the prevailing national rules
and regulations.
Danger!
Be very careful when using cutting tools, such as angle grinders or flame cutters, during the dismantling
process, as pipes and the like contain oil residue and refrigerant, which may be toxic and/or flammable.
7.2
Waste disposal
Machine parts
When dismantling the plant, it is important to properly sort the parts that should be disposed of. The
compressor, frame, containers and so on belonging to the category of iron and metal scrap must be
brought to an approved scrap dealer who complies with the prevailing national rules and regulations.
Oil and refrigerant
Oil and refrigerant waste must be disposed of in accordance with the prevailing national rules and regu-
lations. Do not transport oil in open containers in a closed car.
Electric components
Electric and electronic products such as wiring, panels and hardware must be disposed of in accordance
with prevailing national rules and regulations.
Batteries
Used batteries, for example from the control system backup, must be disposed of in accordance with
prevailing national rules and regulations.